When considering welding techniques for cast iron materials, the use of cast iron MIG welding wire emerges as a versatile and reliable option. Welding cast iron is notorious for its challenges due to its high carbon content, which can cause cracking if not handled correctly. However, with the right approach and tools, these challenges can be effectively managed.
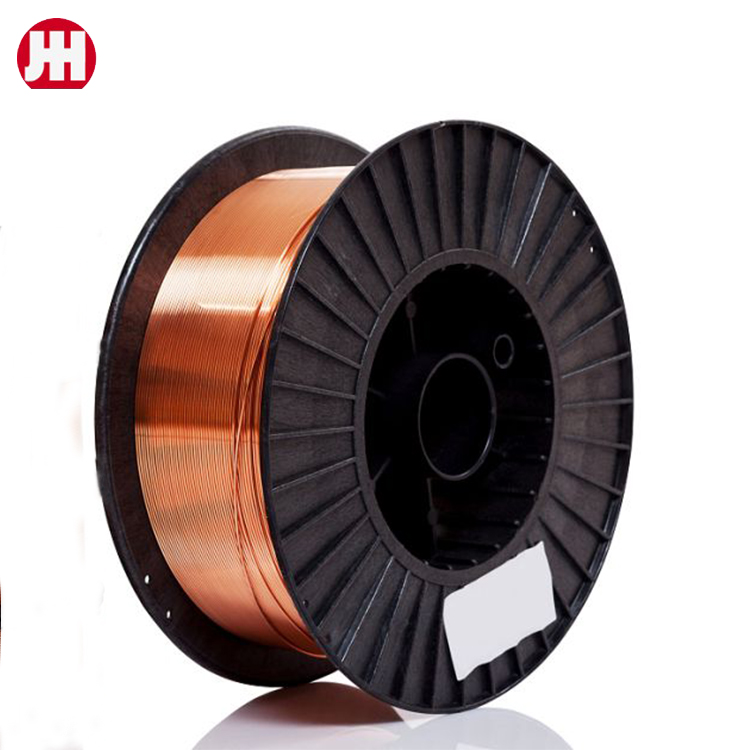
Cast iron MIG welding wire is specifically designed for use with MIG welders to join or repair cast iron components. The wire's composition typically includes a nickel-copper alloy, which helps to minimize thermal stress and cracking during the welding process. This alloying also aids in ensuring strong metallurgical bonds between welds, enhancing structural integrity.
One of the primary advantages of using cast iron MIG welding wire is its ease of use. Unlike traditional welding methods that require specialized skills, MIG welding is more accessible to hobbyists and professionals alike. This accessibility makes it an attractive option for industries such as automotive repair, construction, and maintenance operations.
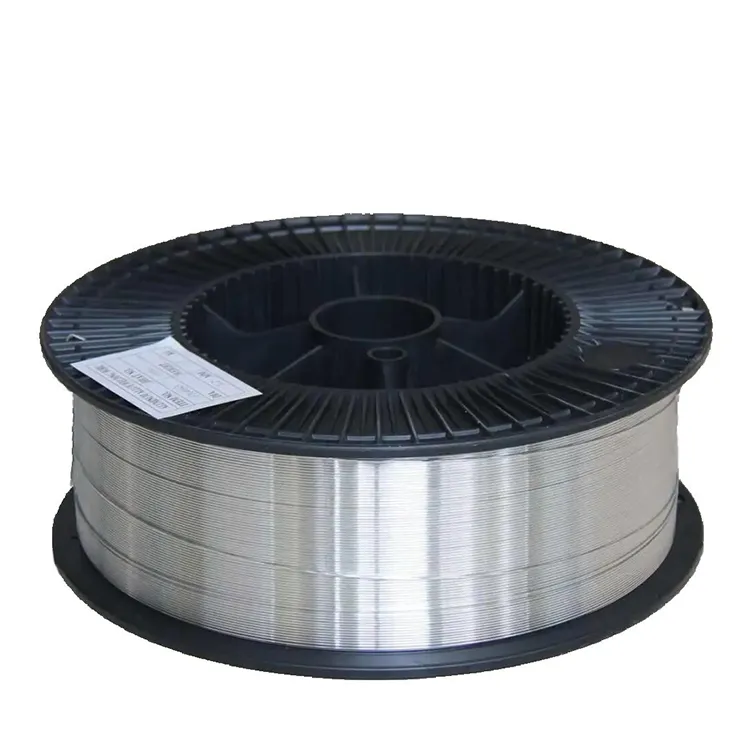
It's essential to understand the importance of pre-weld preparation when using cast iron MIG welding wire. Cleaning the cast iron surface to remove any rust, grease, or paint is crucial to ensuring a successful weld. Furthermore, the material should be heated gently before welding to reduce thermal shock, which is a leading cause of cracks. A slow cooling process post-welding further decreases the chances of structural failures, making temperature control a critical factor during the entire welding operation.
Expertise in MIG welding can transform a daunting task into a straightforward, effective process. Professionals trained in handling cast iron materials using MIG welding techniques can attest to the significant reduction in post-weld defects. By managing heat input and understanding how to control the ambient environment during welding, experts can create robust joints that withstand stress and time.
cast iron mig welding wire
Products using cast iron MIG welding wire have gained a reputation for improved durability and support. Automotive parts repaired using this method tend to last longer, offering greater performance reliability. In the world of construction, structures and machinery parts restored with cast iron MIG welding demonstrate enhanced resilience against wear and tear, thereby reducing downtime and maintenance costs.
When discussing authority in the field of welding, many industry standards and professional bodies acknowledge the effectiveness of MIG welding for cast iron. Research and studies from leading welding organizations underline how advancements in welding wire technology have made it possible to tackle cast iron's challenges head-on. Industry leaders have consistently recommended this method as it combines technical sophistication with practical application.
Trustworthiness in welding practices is paramount, especially given the risks involved when dealing with cast iron components. Transparent practices involve educating users about the welding process, the importance of wire selection, and suitable MIG welder settings. This knowledge builds trust with end-users and stakeholders who rely on durable, long-lasting repairs and joints.
Implementing cast iron MIG welding solutions requires not just theoretical understanding but also practical experience. Welders attest to the nuanced requirements of cast iron, where experience plays a crucial role in overcoming procedural hurdles. The welding community often shares insights and developments, further fostering an environment of collective learning and shared expertise.
In the end, the careful selection of cast iron MIG welding wire combined with expert technique and a deep understanding of cast iron behavior leads to exceptional results. This trifecta ensures that welded components not only fulfill immediate demands but continue to perform efficiently over time. As industries evolve and push the boundaries of material engineering, the application of reliable welding practices such as these will remain integral to maintaining and enhancing the quality and longevity of critical infrastructural and mechanical systems.