Selecting the best flux core wire for your welding projects, such as the .030 diameter option, goes beyond mere specification and invites a deeper understanding rooted in both practical experience and professional expertise. The .030 flux core wire represents a balance of accessibility and performance, making it a reliable choice for both novice welders and seasoned professionals.
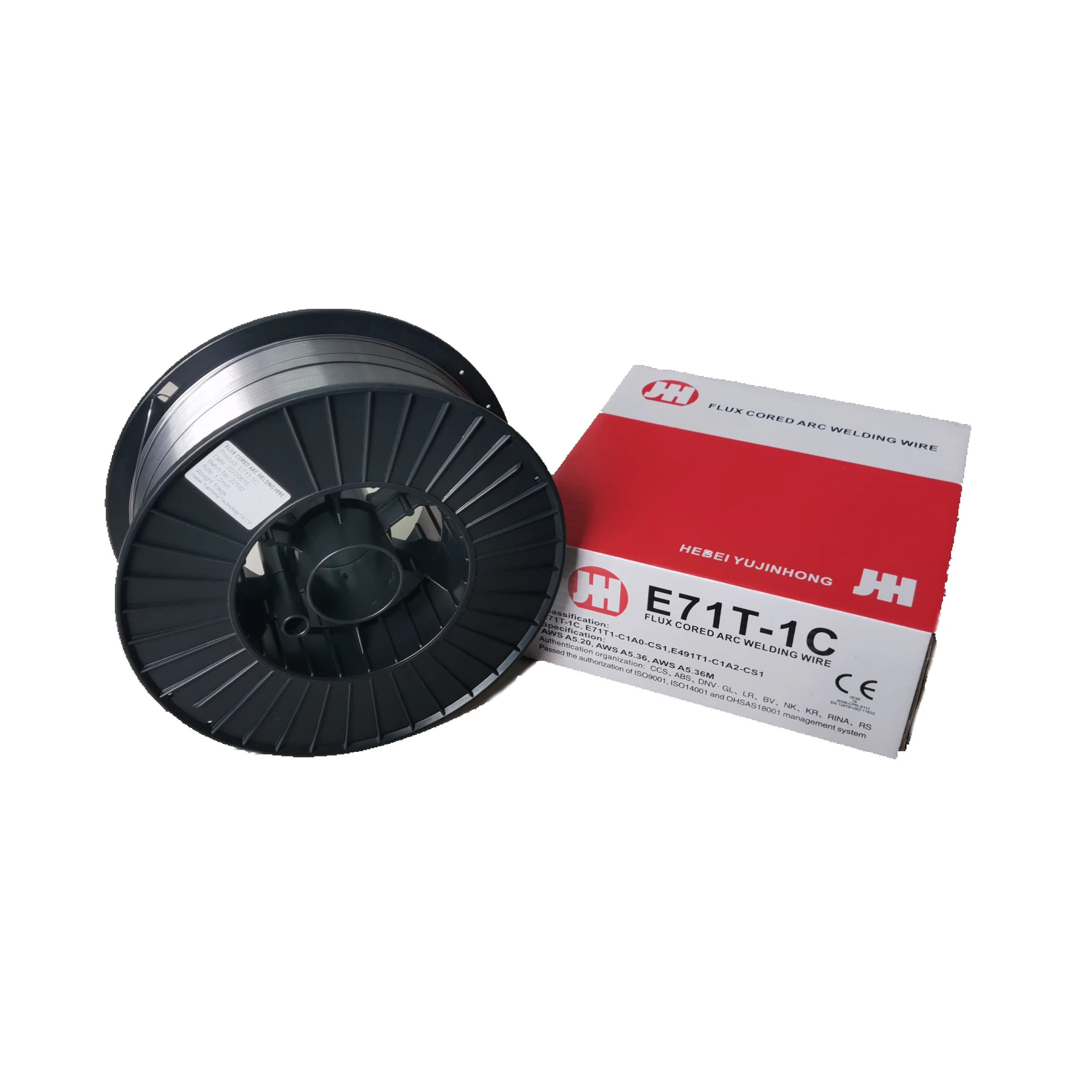
The flux core wire .030, often identified with the type of welding known as flux-cored arc welding (FCAW), is a versatile medium that grants users the flexibility to operate in diverse conditions. Its design eliminates the need for an external shielding gas, which is advantageous for outdoor welding environments where wind could disrupt gas coverage and affect weld quality. The wire expertly contains its own protective shield, ensuring robust and consistent results.
In terms of professional applications, the .030 flux core wire is particularly suited for thinner materials, generally in the range of 18 gauge to roughly 1/4 inch thick. Its diameter enables excellent control over the welding arc, making it ideal for precise work common in automotive repairs and creative metalwork. The wire’s performance is characterized by its smooth arc and minimal spatter, attributes crucial for maintaining a steady workflow in high-pressure scenarios.
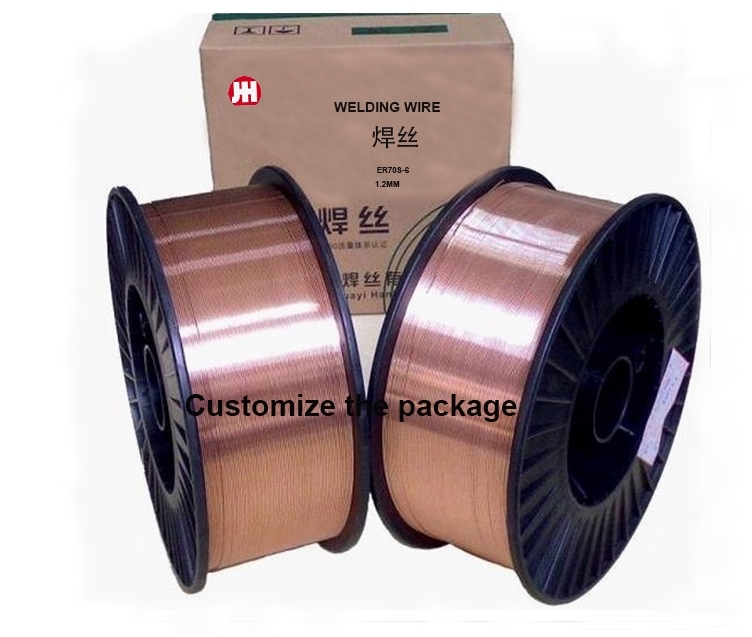
From an expertise standpoint, the type of wire you choose can significantly influence the efficiency and quality of your projects. Wires with a .030 diameter are known for providing superior control, allowing for a cleaner and more precise bead. They are also well-suited for scenarios where the quality of the finish is as important as the structural integrity of the weld, such as in decorative pieces or detailed metal sculptures.
flux core wire .030
Authoritatively, flux core wire users are advised that despite its advantages, the use of .030 wire demands a precise understanding of heat settings and travel speeds. Manufacturers such as Lincoln Electric and Hobart Welding endorse these wires for their adaptability and ease of use, yet underline the need for professional calibrations and settings to maximize effectiveness and ensure safety. Proper training on welding machines, wire feed speed, and voltage settings acclimates operators to obtain the best results, providing assurance in the quality of their workmanship.
Trustworthiness in choosing a flux core wire extends to the user's commitment to understanding the material's limitations and potential. Feedback from industry veterans highlights the essential practice of test welding on scrap material before committing to a project. This practice not only builds familiarity with the wire characteristics but also instills confidence in the user, nurturing a trustworthy relationship with the materials used.
The compatibility of .030 flux core wire with numerous types of welding equipment also broadens its appeal, providing a seamless experience for users who work across various machines. It's crucial that welders pay attention to their machine’s capacity, as mismatched wire and machine combinations can lead to unsatisfactory outcomes or equipment damage. This due diligence ensures a credible choice and builds a reputation for reliability among peers and clients.
In summary, selecting the right flux core wire in the .030 size is more than just a technical decision—it is a testament to the user's dedication to quality, precision, and safety. For anyone looking to enhance their welding craftsmanship, the experience and expertise required to master this type of wire are well worth the investment. Whether working independently or as part of a collaborative team, welders can significantly benefit from this wealth of knowledge, making informed decisions that underpin their projects' success.