Understanding the nuances of welding can elevate the quality of your projects, whether you're an enthusiastic hobbyist or a seasoned professional.
A tool that often stands at the core of successful welding endeavors is flux core wire. This product embodies a fusion of technical ingenuity and practical application, making it indispensable in the world of welding.
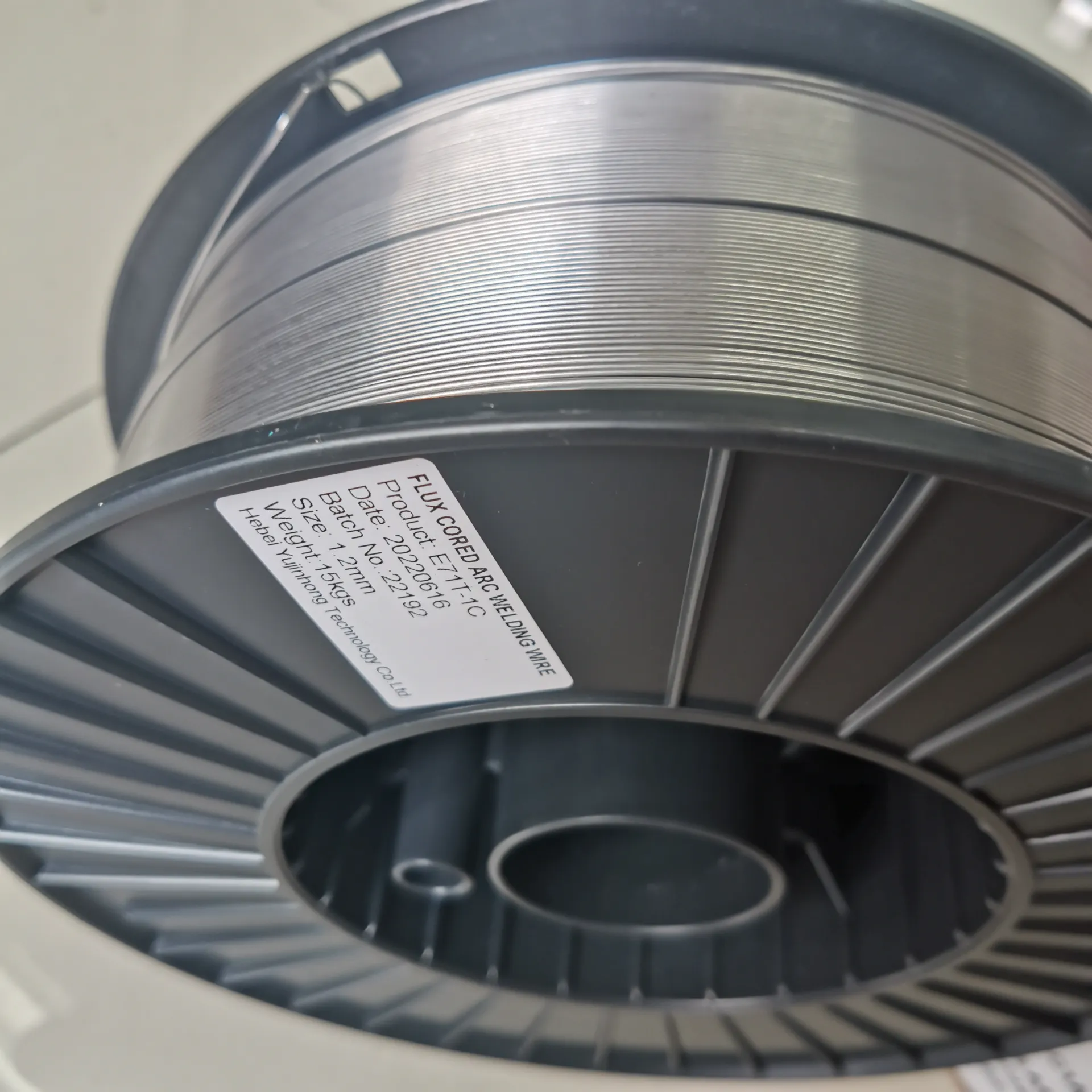
At its essence, flux core wire is designed to simplify and enhance the welding process. It operates through a method known as Flux-Cored Arc Welding (FCAW), which caters to various welding demands with its self-shielding capabilities. Unlike the traditional welding methods that require external shielding gas, flux core wire is imbued with flux at its core, providing protection against atmospheric contamination. This innovation not only streamlines the welding setup but also broadens the scope of outdoor welding by reducing the susceptibility to wind interference.
Welding professionals often gravitate towards flux core wire for projects that require deep penetration and strong welds. Its proficiency is particularly pronounced when working with thicker materials or in out-of-position welding scenarios. Structures that endure high stress such as shipbuilding, pipeline outfits, and heavy machinery manufacturing significantly benefit from this method. The welding arc produced is intense, ensuring robust fusion and dependable results even in challenging positions.
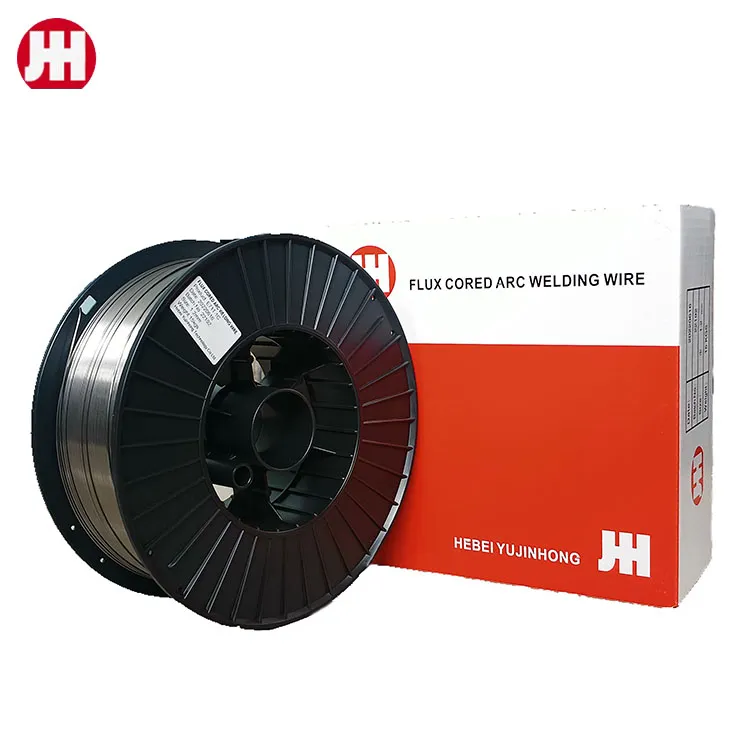
Flux core wire also allows for a continuous feed in the welding process, a feature which optimizes productivity by reducing downtime between electrode changes. This continuity not only enhances efficiency but significantly diminishes the likelihood of defects in the final weld. The result is a cleaner and more aesthetically pleasing seam that requires minimal post-weld finishing.
Transitioning to the specifics of flux core wire selection, the market offers myriad options tailored for distinct applications. It's crucial to match the wire's properties with the base materials being welded. For instance, certain wires are formulated for mild steel, while others excel with stainless or galvanized steel. Understanding the welding environment – such as the presence of contaminants, joint configurations, and expected mechanical stresses – guides the appropriate wire choice.
welding flux core wire
Quality control and certification play pivotal roles in selecting flux core wire. Reputable manufacturers undergo rigorous testing to ensure their products meet industry standards. Compliance with standards such as AWS (American Welding Society) classifications is a testament to a product’s reliability. This certification guarantees the wire will perform consistently under specified conditions, lending confidence to professionals who rely on them for critical applications.
Moreover, advancements in the manufacture of flux core wire are shaping the future of welding technology. Improvements in wire formulations are reducing spatter and increasing deposit rates. Similarly, innovations in wire feeding mechanisms enhance the precision and control, allowing for smoother welds. Staying abreast of these technological advancements can provide welders with a strategic advantage, leading to superior outcomes.
Safety is an indispensable consideration. When using flux core wire, precautions must be taken to protect against fumes and heat exposure. Proper ventilation and usage of protective gear are mandatory to safeguard against health hazards. Understanding and adhering to these safety protocols not only protects the operator but also sets a standard for professionalism and care in the workplace.
For those delving into the specialized realm of flux core wire, resources and continued learning are invaluable. Industry forums, authoritative guides, and expert consultations can provide insightful advice and troubleshooting tips. Establishing a network of knowledgeable professionals enriches understanding and enhances problem-solving acumen, directly impacting the quality and efficiency of the welding work.
In conclusion, flux core wire represents a cornerstone of modern welding. Its unique properties and advantages over traditional options make it an invaluable tool in a welder’s arsenal. By integrating the right techniques, understanding material compatibility, and staying informed about industry advancements, professionals can leverage flux core wire for superior welding outcomes. This combination of experience, expertise, authoritativeness, and trustworthiness is what transforms welding from a task into an art form.