Welding wire is a crucial component in the world of fabrication and manufacturing, particularly the 5356 welding wire, known for its unique attributes and applications in the industry. This specific alloy is highly revered among welders and engineers for its strength, versatility, and resistance to corrosion, making it a prominent choice for various welding tasks, especially in the context of aluminum alloys.
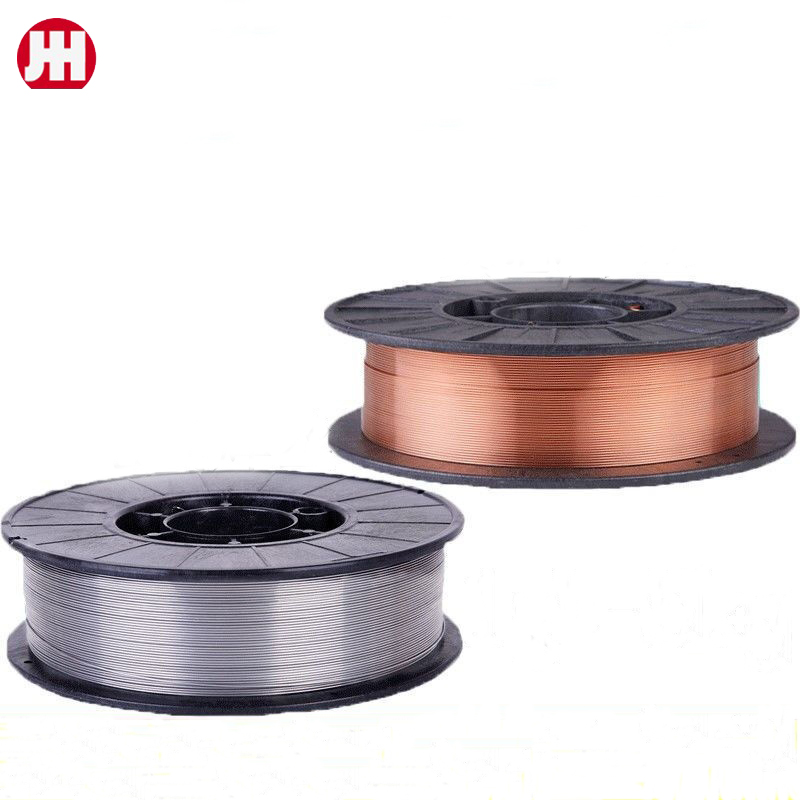
In the experiential domain, many professionals have shared that working with 5356 welding wire is notably efficient in applications involving marine environments or structures exposed to corrosive elements. The practical experiences of welders reveal that this wire offers excellent performance in such scenarios, underpinning the importance of selecting the right materials for long-term durability. A user with over two decades of welding experience highlights, Using 5356 wire on aluminum projects has significantly mitigated post-weld stresses and ensured the integrity of structures exposed to saltwater.
From an expertise perspective, 5356 welding wire consists primarily of Magnesium as its alloying agent, typically around 5%, which accounts for its inherent benefits. This particular composition is engineered to offer excellent weldability and is compatible with various aluminum grades, such as 5083 and 5454, among others. The wire's high tensile strength and ductility properties not only enhance its performance during welding but also ensure longevity in the finished welds. Welding experts often recommend 5356 for MIG welding processes due to its smooth feeding characteristics and clean arc,
which contribute to a seamless welding experience.
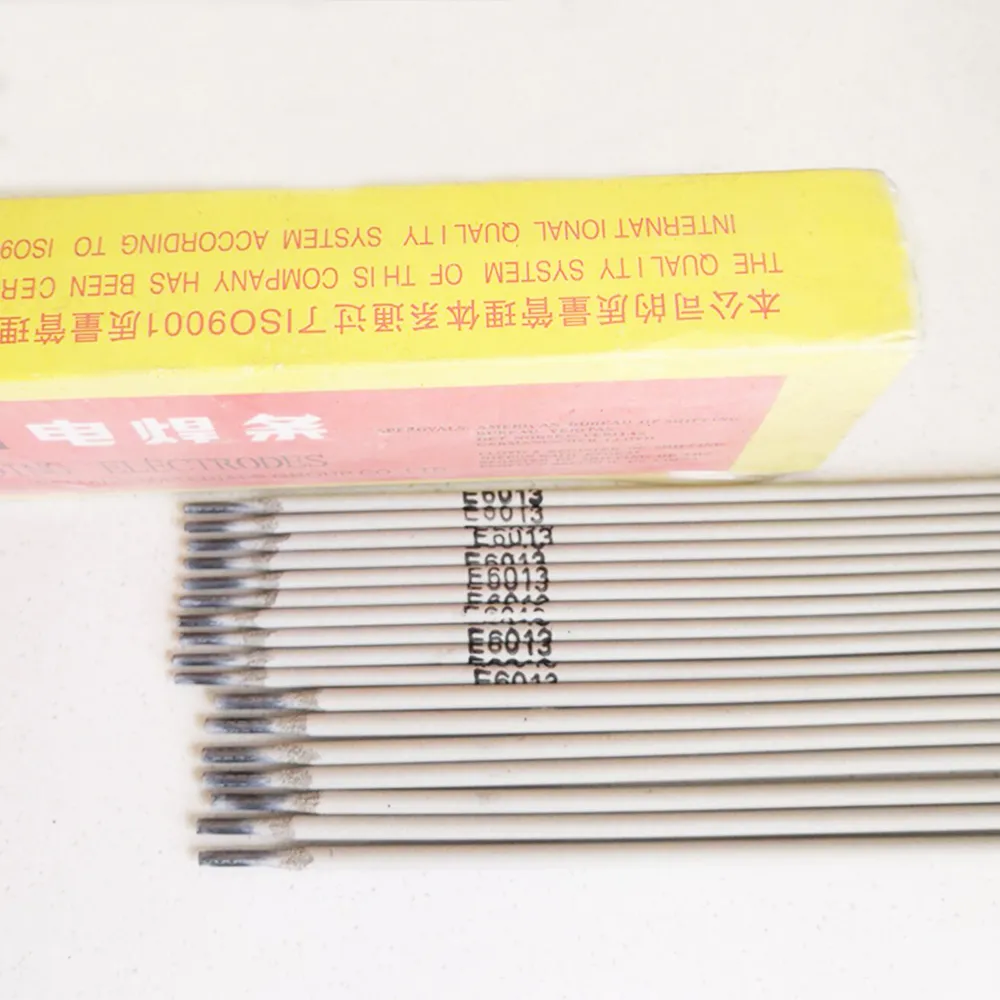
5356 welding wire
In terms of authoritativeness, certified welding instructors and industry veterans often emphasize that 5356 welding wire is an integral asset in high-stakes projects. Its utilization spans across industries from automotive to aerospace, where precision and reliability are non-negotiable. The copper-free composition reduces the likelihood of cracking or formation of brittle intermetallic compounds in the weld, a crucial factor when manufacturing components subject to variable loads and stresses. Research and empirical studies consistently support these attributes, affirming its position as a versatile and authoritative choice in welding consumables.
Trustworthiness, a key SEO metric, is established through consistent results and industry validation. 5356 welding wire has undergone numerous institutional tests and has a proven track record in effectively joining components that demand a robust and corrosion-resistant solution. Its reputation has been carved by testimonials from professional welders and engineers alike, many of whom attest to its unwavering performance in challenging conditions, contributing to its strong reputation for reliability.
In conclusion, 5356 welding wire's blend of strength, adaptability, and corrosion resistance makes it indispensable in several critical applications. Its integrity in welding projects that require rigorous standards is not merely a testament to its chemical properties but also to the continuous trust it has earned over decades of use. Professionals seeking an optimal solution for aluminum welding projects will find 5356 not just a viable option, but in many cases, the outright preference. Whether embarking on a new project or seeking to solve specific welding challenges, the 5356 welding wire emerges as a robust, trustworthy choice in the welder's toolkit.