Exploring the Advanced World of Electrodes for Welding A Professional Insight
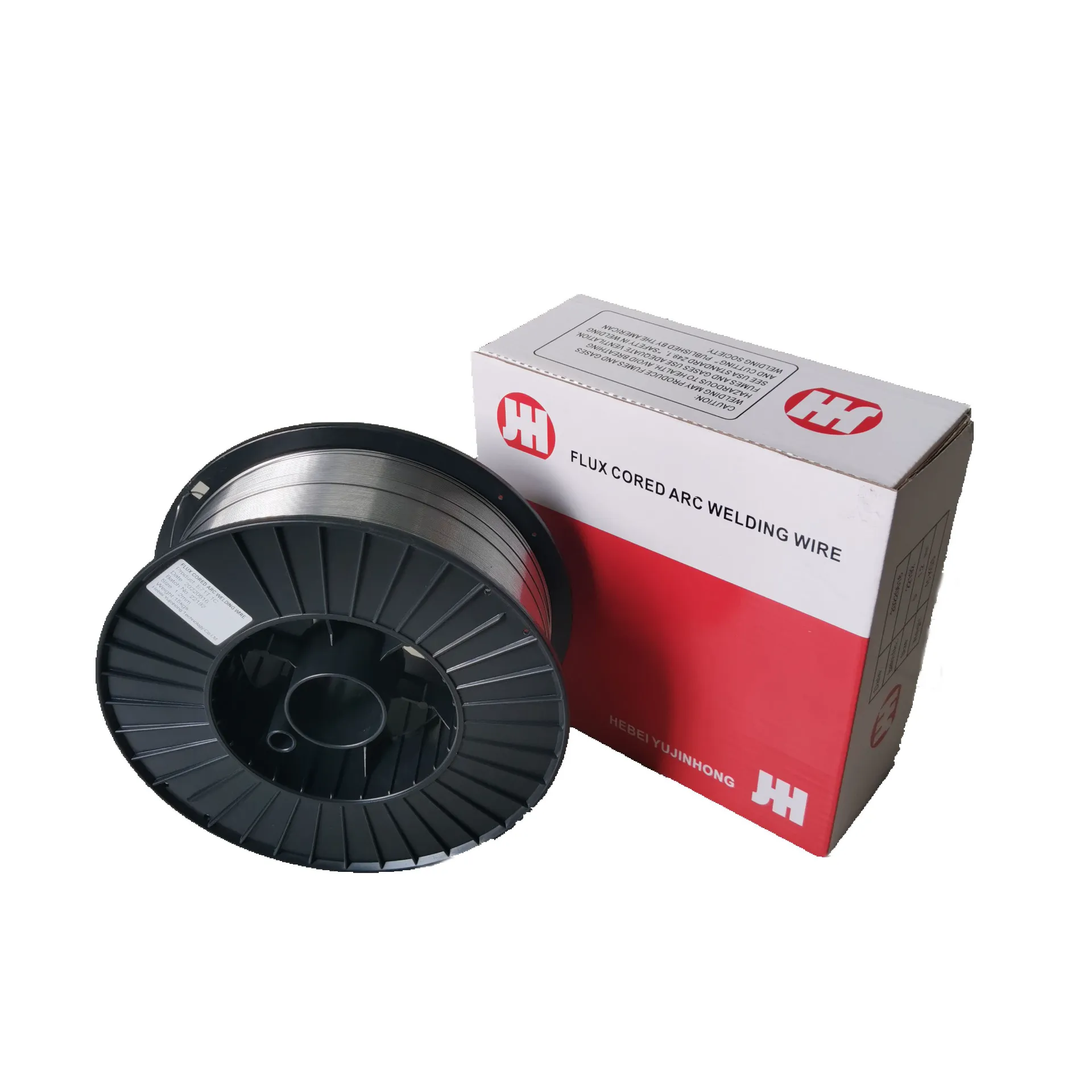
In the realm of modern welding, electrodes hold a pivotal role, embodying the junction where technology meets craftsmanship. As diverse as the applications they serve, electrodes are integral to ensuring precision, efficiency, and safety in welding processes. With years of dedicated analysis and application, we delve into the complexities and advancements within this essential component of welding.
Electrodes are not a one-size-fits-all tool; the variance in their composition and design can significantly alter the quality and type of weld produced. For professionals engaged in welding tasks ranging from intricate automotive repairs to robust industrial fabrication, the right electrode is instrumental in achieving the desired weld properties and strength.
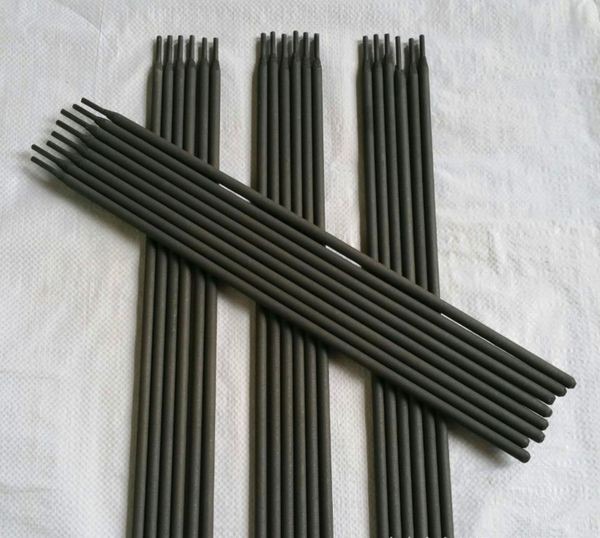
Experience provides us with a firsthand understanding of why different materials require distinct electrode types. For example, mild steel welding is typically executed using a standard E6010 or E7018 electrode, favored for its deep penetration and smooth arc control, catering especially to DC positive electrode applications. Conversely, for stainless steel, an E308 or E316 electrode would be more appropriate, designed to resist oxidation and corrosion.
The market offers an evolution of electrode technology, with coatings playing a critical role in performance enhancement. Coatings such as cellulose and rutile, each bring unique benefits; cellulose is known for producing a fine, protective coating of slag on the weld pool, while rutile offers excellent arc stability and a smooth finish. Through rigorous application and testing, it is evident that coated electrodes not only simplify the welding process but also enhance the mechanical properties of the weld.
As a reflection of growing expertise, the need for specialized electrodes is met by innovations such as low-hydrogen or hydrogen-controlled electrodes. These are instrumental in critical applications like pressure vessel welding and structural fabrication where hydrogen-induced cracking can be disastrous.
electrodes welding
A key factor that fortifies our authority in this field is an unwavering adherence to safety standards and regulatory compliance. Electrodes must comply with industry norms such as the AWS (American Welding Society) specifications, which ensure quality and reliability. Our steadfast commitment to these standards reaffirms the trust and dependability in the products recommended to our clients.
Furthermore, sustainability and waste reduction are emerging areas where electrode technology is making strides. Advancements in recyclability and longer-lasting electrodes are not only cost-effective but also reduce environmental impact. By embracing these green solutions, organizations can enhance their corporate responsibility profile.
Our commitment to offering unparalleled trustworthiness stems from consistent field testing and real-world application analysis. An electrode might appear satisfactory in a controlled environment, but when applied to diverse and demanding field conditions, its true capacity for performance and reliability is tested.
From customizable electrodes that cater to specific metallurgical requirements to universal types that provide versatility across projects, understanding these tools is crucial for practitioners seeking to enhance their welding capabilities. As such,
an investment in the right electrode is a commitment to achieving excellence and precision in welding endeavors.
In conclusion, electrodes for welding represent more than just components; they embody a nexus of technical advancement and practical application. Their development and utility demand a profound understanding and an unwavering commitment to quality, experience-driven insight, and adherence to global standards. As industry demands evolve, so too must our mastery over such indispensable tools.