Welding sticks, also known as welding electrodes, are indispensable components in the welding world, fulfilling the critical task of delivering the necessary filler material and creating a stable arc between the welding machine and the workpiece. For professionals aiming to enhance their proficiency or for businesses looking to optimize their welding operations, understanding the selection and application of welding sticks is crucial.
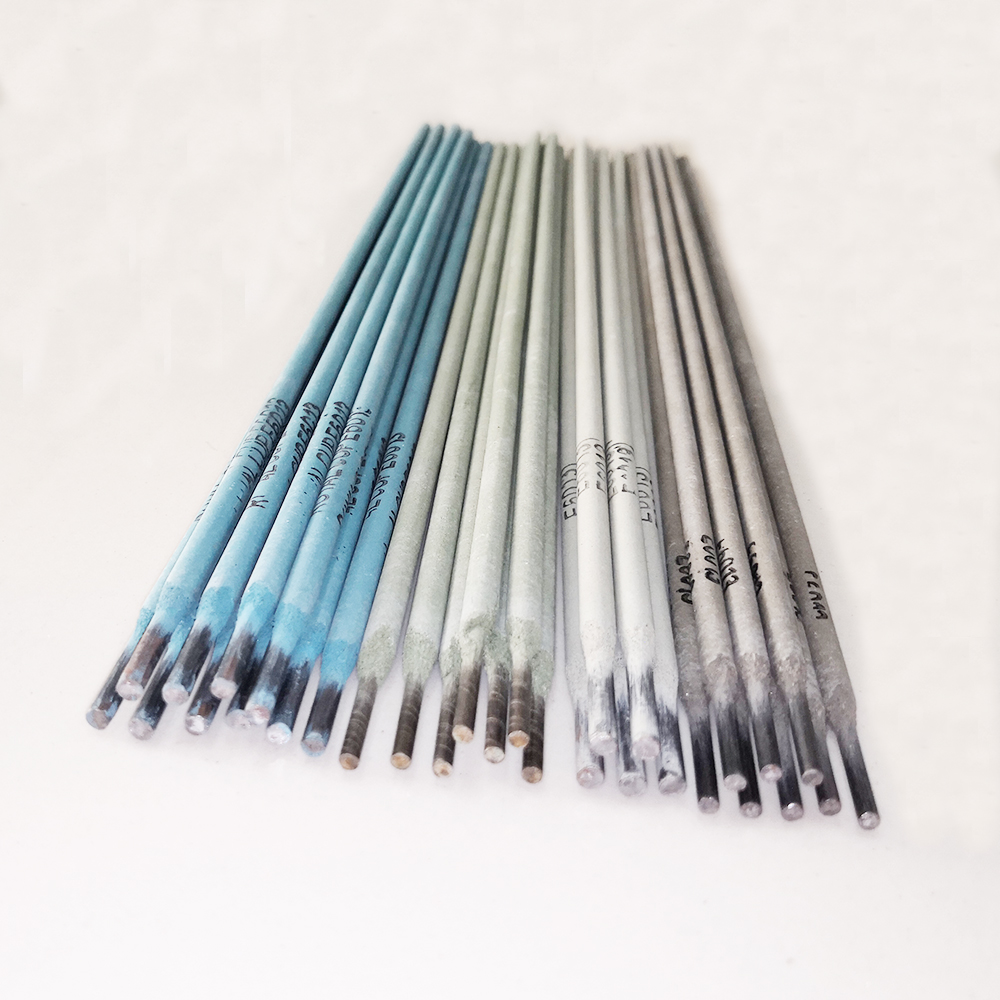
In practical hands-on experience, welding sticks have shown their versatility across diverse sectors from automotive repairs to construction and shipbuilding. A comprehensive grasp of their types and applications can significantly affect the outcome of welding projects. The most common welding electrode types include mild steel, stainless steel, and aluminum, each catering to specific metal types and project requirements. Professionals with hands-on experience often favor mild steel electrodes—such as the E6011 or E7018 models—for their reliability and excellent penetration capabilities, particularly beneficial in structural welding applications.
From an expertise standpoint, choosing the correct welding stick involves analyzing several factors the material of the workpiece, the position of the weld, and the desired mechanical properties of the weld. For instance, the E7018 electrode is revered for its low-hydrogen properties, making it ideal for critical applications that require high tensile strength and crack resistance. It's important for professionals to align their electrode choice with their welding machine's capabilities, ensuring compatibility and optimal performance.
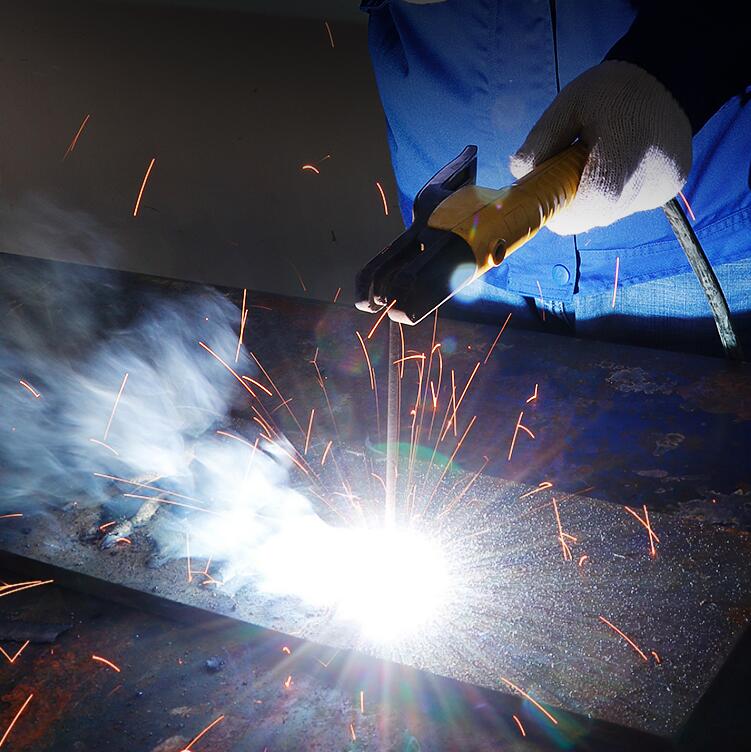
Maintaining expertise in this domain also involves staying updated with technological advancements and new product developments. Manufacturers are continually innovating to provide electrodes with improved flux compositions that reduce spatter, enhance arc stability, and produce smoother welds. Leveraging such advancements can provide substantial benefits, from reducing overall welding time to achieving aesthetically superior welds, thereby increasing project efficiency and quality.
welding stick
Authoritativeness in welding requires the amalgamation of experience, continuous learning,
and methodical practice. Welding instructors and industry veterans often emphasize the importance of mastering various welding positions with varied electrodes to build a diversified skill set. Practicing vertical, horizontal, overhead, and flat welds with different welding sticks equips welders with the flexibility to tackle numerous scenarios with confidence.
Trustworthiness, a critical attribute in the welding profession, is built upon the credibility of the decisions regarding welding stick selection and application. Professionals rely on their accumulated knowledge and industry standards, such as the American Welding Society (AWS) classifications, to guide their choices. This adherence to recognized standards ensures the structural integrity and safety of welded projects, thereby establishing trust with clients and stakeholders.
For those who aim to refine their welding skills or make informed purchasing decisions, accessing resources, forums, and communities where experienced welders share insights can be invaluable. These platforms often feature reviews on the latest products, troubleshooting tips, and discourse on best practices, all essential for enhancing your welding strategy.
In essence, welding sticks are not merely tools but integral elements that define the quality, efficiency, and reliability of welding operations. Expertise in their application not only propels individual professional growth but also reflects in the excellence of the welded structures and projects, ensuring safety and durability for years to come.