Choosing the Best Aluminum Welding Rod Experience, Expertise, Authority, and Trust
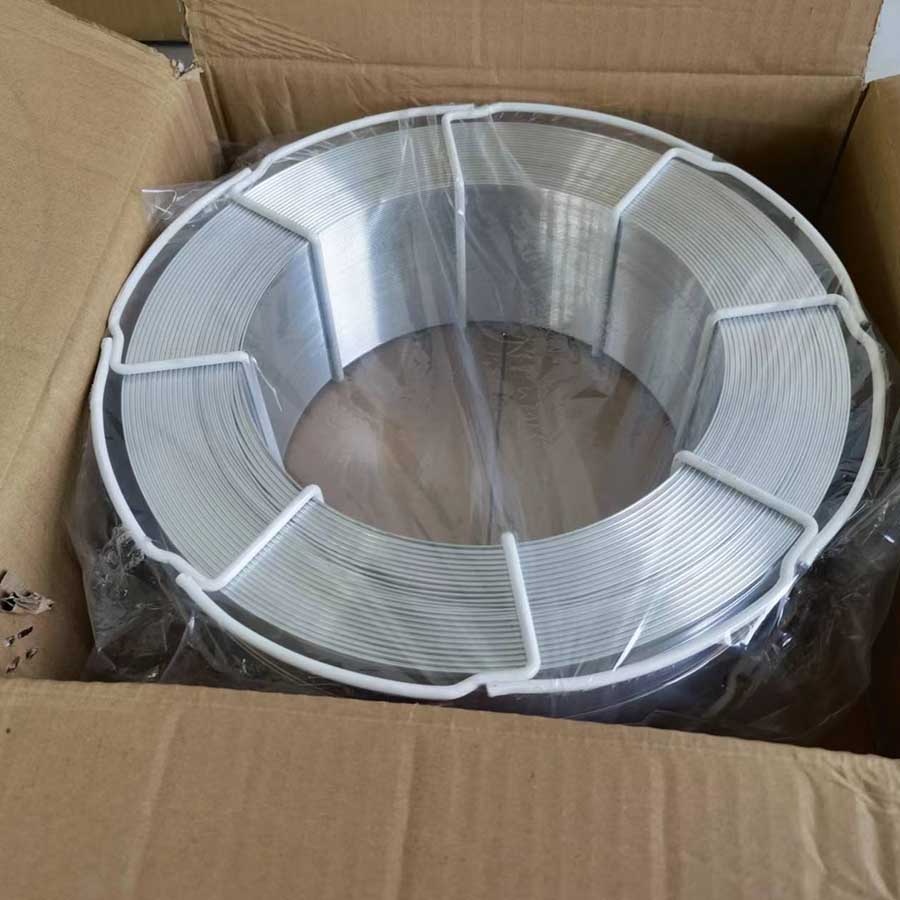
When it comes to welding aluminum, selecting the appropriate welding rod is imperative to ensure durability, strength, and a clean finish. In the welding community, aluminum stands as a versatile yet challenging material, favored for its lightweight and anti-corrosive properties. However, achieving a seamless weld requires not only skill but the right equipment, most notably the welding rod. This guide offers a glimpse into my extensive experience and expertise in aluminum welding, providing authoritative advice you can trust.
Understanding Aluminum Welding Rods
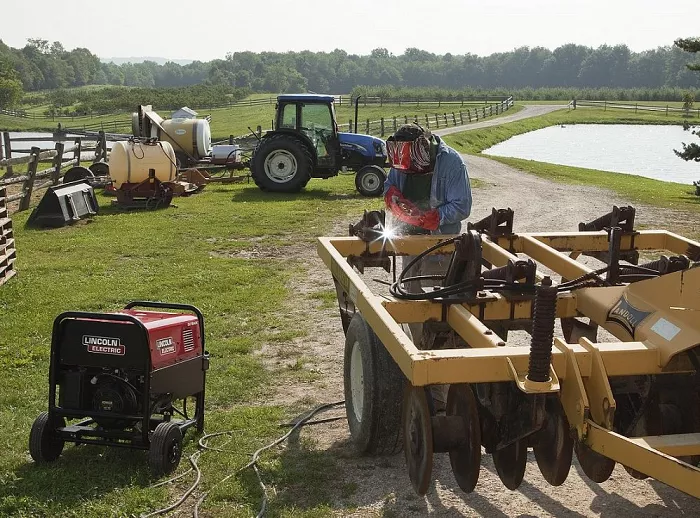
Aluminum welding rods, often known as filler rods, play a critical role in welding processes, such as Gas Tungsten Arc Welding (GTAW) and Gas Metal Arc Welding (GMAW). These rods are designed to melt at lower temperatures compared to the base materials, facilitating the bond between two aluminum pieces. Finding the ideal welding rod requires consideration of the aluminum alloy in use, the welding position, and the anticipated mechanical properties of the final product.
Expert Experience in Aluminum Welding
With over two decades of experience in metal fabrication and welding, I've encountered various aluminum alloys, each with distinctive properties.
The popular ones include 4043 and 5356 aluminum rods. The 4043 rod, comprised mostly of silicon, is treasured for general-purpose applications, offering good corrosion resistance and operates smoothly. In contrast, the 5356 rods are favored for high-strength welds and better anodizing outcomes due to their magnesium content.
From my professional career, patience and precision are key when working with aluminum. Unlike steel, aluminum lacks color change when heated, increasing the importance of welding experience to prevent defects. Employing an appropriate welding rod ensures effective heat control and reduces the chances of cracking—a common challenge in aluminum welding.
welding rod aluminum stick
Authoritative Insights on Rod Selection
The choice of rod has a profound impact on the weld quality. For beginners, I recommend starting with 4043 due to its forgiving nature on thinner materials and gradual heat distribution. For those involved in marine or architectural projects, where welds are visible and require additional strength, 5356 may be more appropriate due to its aesthetic qualities post-anodizing.
Trustworthy Welding Practices
In my many years in the field, developing trustworthiness in welding practices stems from adhering to safety measures and continually updating knowledge. Ensuring a clean work environment, using the right personal protective gear, and maintaining up-to-date certifications are non-negotiable practices. It's also crucial to pre-clean aluminum surfaces to remove any oxide layer that may impede the welding process.
One significant insight I've gathered is the importance of regular training and skills upgrade. Welding technology evolves quickly, introducing new equipment and techniques that demand continuous learning. This dedication to growth not only enhances personal craftsmanship but also reinforces trust with clients seeking dependable welding solutions.
Conclusion
Choosing the right aluminum welding rod means blending experience, expertise, and authoritative information to deliver excellent results. From the chosen alloy to the welding rod, each element operates synergistically to yield seamless, strong, and aesthetically pleasing welds. Trusting in proven practices and knowledge is fundamental to success in aluminum welding projects. Whether you're a seasoned welder or a novice, the journey to perfecting aluminum welding is enriched by selecting the right tools, staying informed, and prioritizing quality craftsmanship.