When it comes to achieving precision and consistency in welding projects, the choice of welding rod can significantly influence the outcome. Among many options available, the 1/8 7018 welding rod stands out due to its unique properties and versatile applications. This article delves into the critical aspects of using the 7018 welding rod, drawing from real-world experiences and expert opinions, while establishing an authoritative and trustworthy perspective on its usage in various welding scenarios.
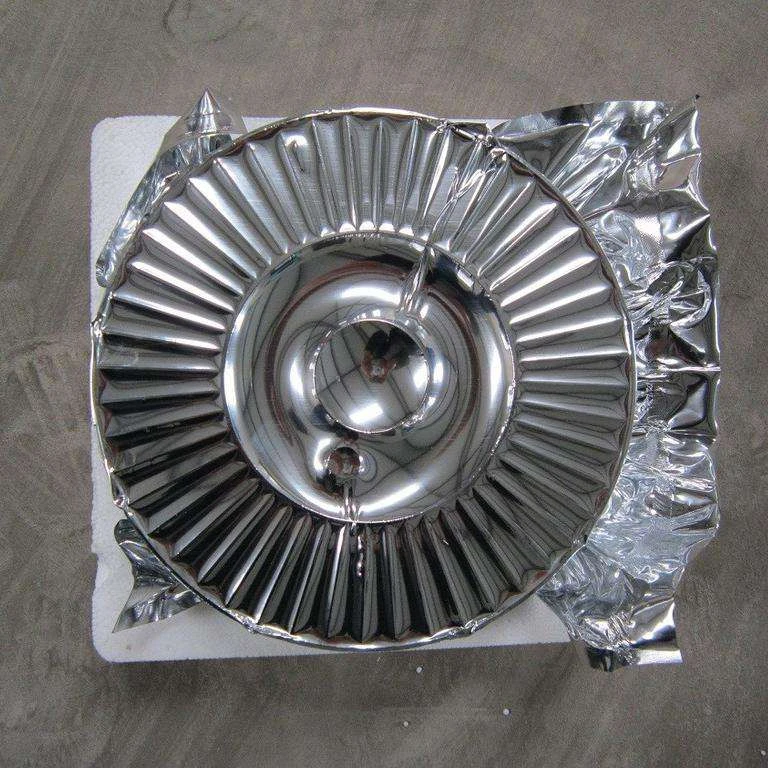
The 7018 welding rod is frequently referred to as a low hydrogen rod, which is prized for minimizing hydrogen embrittlement in the weld metal. This characteristic is particularly beneficial when working with high-strength steels as it enhances the toughness and ductility of the weld joint. The low hydrogen levels prevent cracking and ensure a superior finish that meets stringent industrial standards.
One of the standout qualities of the 1/8 7018 welding rod is its excellent arc stability. Experienced welders appreciate how this rod maintains a steady arc, allowing for smooth and consistent welds. This stability is crucial when performing out-of-position welds, such as vertical or overhead positions, where control over the weld pool is imperative. The rod's ability to deposit slag that is easy to remove further contributes to cleaner and visually appealing welds, reducing post-weld cleaning efforts.
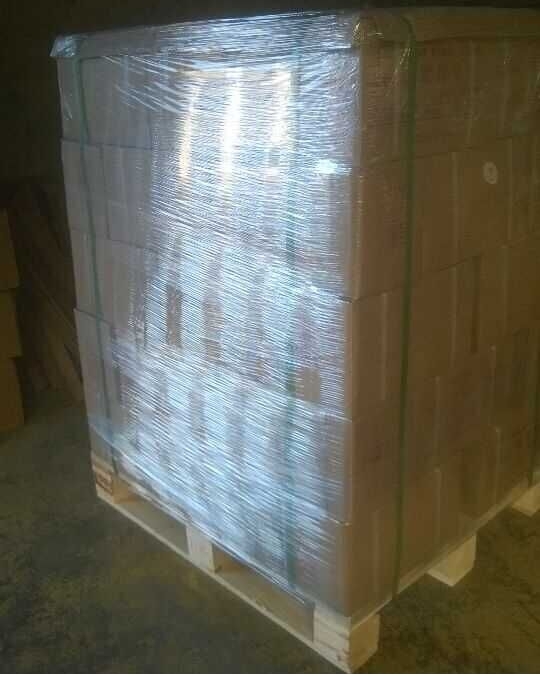
From a professional standpoint,
the 7018 welding rod is a go-to choice for many structural steel projects. Its compatibility with AC and DC power sources offers flexibility in terms of welding equipment, making it suitable for a wide range of applications, including bridge construction, petrochemical facilities, and shipbuilding. Structural engineers and welding specialists often recommend 7018 rods for critical load-bearing welds due to their tensile strength of approximately 70,000 psi, ensuring reliability and safety in structural applications.
In the context of certification and compliance, using a 1/8 7018 welding rod can facilitate adherence to welding codes and standards set by authoritative bodies such as the American Welding Society (AWS). The rod is classified under AWS A5.1, which specifies the requirements for carbon steel electrodes for shielded metal arc welding. Meeting or exceeding these standards signifies a commitment to quality and safety, bolstering trustworthiness in professional settings.
1/8 7018 welding rod
Real-world experiences underscore the rod's durability in demanding environments. Industrial welders tasked with fabricating or repairing heavy machinery often choose the 7018 for its resilience against fluctuating temperatures and mechanical stress. Case studies from sectors such as oil and gas reveal how the rod's welds withstand corrosive conditions, thus extending the lifespan of equipment and infrastructure.
Expert advice emphasizes the importance of proper storage and handling of 7018 rods to retain their low hydrogen characteristics. They should be kept in a controlled environment to prevent moisture absorption, which can compromise weld quality. Using rod ovens to maintain an optimum storage temperature is a common practice among skilled professionals.
Furthermore, selecting the right amperage is vital for achieving the desired weld quality with a 1/8 7018 rod. Typical amperage ranges between 90 and 160 amps due to its diameter, but adjustments should be made based on base metal thickness and welding position. Mastery over these technical aspects allows for tailored solutions to complex welding challenges.
For newcomers to the welding profession, mastering the use of the 7018 rod can be seen as a rite of passage. Beginners often start with flat position welds as they acclimate to the rod's behavior, gradually progressing to more challenging positions as their skills develop. Instructors at welding schools consistently highlight the importance of practice with 7018 rods to build foundational competencies that are applicable across multiple welding disciplines.
In conclusion, the 1/8 7018 welding rod remains an invaluable tool within the arsenal of both novice and seasoned welders. Its balance of mechanical performance, ease of use, and compliance with industry standards makes it indispensable for a variety of projects. By understanding and leveraging its properties, welders can achieve superior results that stand the test of time, reinforcing the rod's reputation as a cornerstone of quality craftsmanship in the welding industry.