An In-Depth Look at 3.2mm 7018 Welding Electrode Factories
Welding electrodes, an essential component in the welding process, play a pivotal role in various industries, from construction to manufacturing. Among the myriad of electrode types, the 3.2mm 7018 welding electrode stands out for its exceptional performance and versatility. This article will delve into the world of factories that specialize in producing these high-quality welding consumables.
3.2mm 7018 welding electrodes are known for their low hydrogen content, making them suitable for critical applications where strength and crack resistance are paramount. The '70' in the name signifies the tensile strength of the weld, while the '18' refers to the low hydrogen classification. These electrodes are typically used in heavy-duty welding tasks, such as in shipbuilding, bridge construction, and pressure vessel fabrication.
Factories manufacturing 3.2mm 7018 welding electrodes operate with precision and stringent quality control measures. The production process begins with the selection of raw materials, which often includes high-grade steel wire, flux, and other additives. These materials are then compounded, cleaned, and coated to create the final electrode. The coating is crucial, as it not only provides shielding but also influences the welding characteristics.
State-of-the-art machinery and advanced technology are employed in these factories to ensure consistency and efficiency
State-of-the-art machinery and advanced technology are employed in these factories to ensure consistency and efficiency
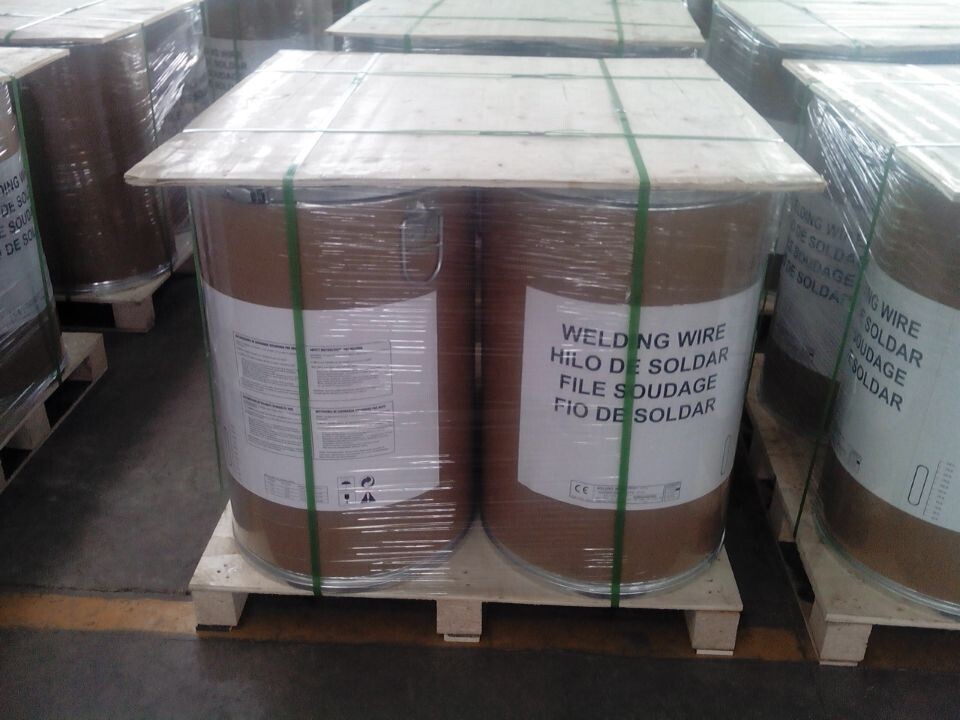
State-of-the-art machinery and advanced technology are employed in these factories to ensure consistency and efficiency
State-of-the-art machinery and advanced technology are employed in these factories to ensure consistency and efficiency
3.2mm 7018 welding electrode factories. Automated winding machines create the precise diameter and length of the electrodes, while computer-controlled ovens maintain the ideal temperature for coating curing. Quality checks are performed at every stage, from material sourcing to the finished product, adhering to international standards like AWS (American Welding Society) or ISO.
Environmental sustainability is another key aspect of these factories. They strive to minimize waste generation and promote recycling, utilizing eco-friendly production methods and energy-efficient equipment. Health and safety of the workforce are also prioritized, with regular training programs and adherence to industry safety norms.
The global market for 3.2mm 7018 welding electrodes is competitive, with numerous factories scattered across Asia, Europe, and North America. Each factory has its unique selling points, be it specialized coatings, customized sizes, or rapid delivery services. Some have even ventured into research and development, constantly innovating to improve electrode performance and durability.
In conclusion, 3.2mm 7018 welding electrode factories are the backbone of a critical industry, ensuring the production of reliable welding materials that support numerous engineering feats worldwide. Their commitment to quality, safety, and innovation underscores the significance of these electrodes in modern manufacturing and construction. As technology continues to evolve, we can expect these factories to push the boundaries of welding electrode technology, further enhancing performance and efficiency.