Understanding the 3 32 Welding Rod 7018 A Factory Perspective
In the world of welding, the selection of the right welding rod is paramount for achieving optimal results. One such highly regarded option is the 3/32 diameter 7018 welding rod. This article delves into the specifics of this welding consumable, focusing on its usage and manufacturing process from a factory standpoint.
The 3/32 7018 welding rod is a low-hydrogen electrode that is commonly used in various welding applications due to its exceptional mechanical properties. The '3/32' refers to the diameter of the rod, which is a standard size used for precision welding tasks where a smaller, more controlled heat input is required. The '7018' part of the code denotes the American Welding Society (AWS) classification system, indicating that this rod has a tensile strength of at least 70,000 PSI and features a low hydrogen content, making it ideal for critical joints and structures.
In the factory, the production of these rods begins with the selection of high-quality raw materials. The primary component is steel, which is carefully sourced to ensure consistency and reliability. The steel is then coated with a flux material, which plays a crucial role during the welding process. It protects the weld from atmospheric contamination, improves the flow of the weld metal, and helps in the removal of impurities.
Once the steel wire is coated, it undergoes a series of heat treatments to remove hydrogen and ensure a low hydrogen content. This is a critical step as excessive hydrogen can lead to hydrogen-induced cracking, compromising the integrity of the weld This is a critical step as excessive hydrogen can lead to hydrogen-induced cracking, compromising the integrity of the weld
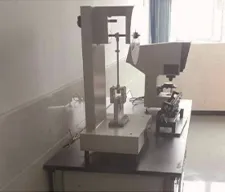
This is a critical step as excessive hydrogen can lead to hydrogen-induced cracking, compromising the integrity of the weld This is a critical step as excessive hydrogen can lead to hydrogen-induced cracking, compromising the integrity of the weld
3 32 welding rod 7018 factory. The rods are then sized and cut to the specified length, typically 36 inches, before being packaged for distribution.
The 7018 welding rod's factory production also emphasizes quality control. Each batch undergoes rigorous testing to verify its mechanical properties, including tensile strength, impact resistance, and ductility. These tests ensure that the rods meet the stringent AWS standards, guaranteeing consistent performance in the field.
From a welding perspective, the 3/32 7018 rod offers several advantages. Its small size allows for precise control, making it suitable for thin sheet metals or intricate welding jobs. The low hydrogen content reduces the risk of cracking, while the higher tensile strength provides robust welds capable of withstanding heavy loads.
In conclusion, the 3/32 7018 welding rod is a testament to the precision and attention to detail in welding rod manufacturing. Factories producing these rods understand the importance of quality, safety, and performance, ensuring that each rod that leaves the factory floor is a reliable tool in the hands of the welder. Whether it's for automotive, construction, or machinery repair, the 3/32 7018 welding rod stands as a symbol of the fusion between technology, engineering, and skilled craftsmanship.