In the realm of welding, the importance of selecting the right equipment cannot be overstated, especially when the task demands precision and reliability. Among the array of tools available, the 7018 welding rod stands out, renowned for its versatility and strength. This electrode, frequently employed across various industries, promises exceptional performance when used correctly. Herein lies an exploration into the features and application of the 7018 welding rod, delivering insights from seasoned experts in the welding domain.
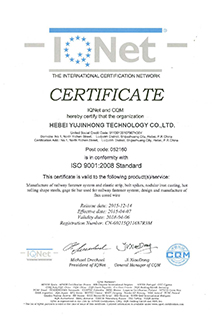
The 7018 welding rod is commonly touted as the welder’s choice for its unique composition and arc characteristics. Comprising a low-hydrogen iron powder coating, the 7018 is particularly favorable for its ability to mitigate the risk of hydrogen-induced cracking. This feature is critical for projects involving high-strength steels, where the integrity of the weld is paramount. Welders often favor the 7018 for tasks requiring a clean, smooth finish, as its composition allows for an aesthetically pleasing weld bead.
From a professional standpoint, using the 7018 welding rod requires adherence to specific conditions to maximize its benefits. Welding experts emphasize controlling moisture and temperature, as the low-hydrogen coating is sensitive to atmospheric conditions. Proper storage in a controlled environment or using rod ovens ensures that the integrity of the rod is maintained, preventing issues such as porosity and reduced tensile strength.
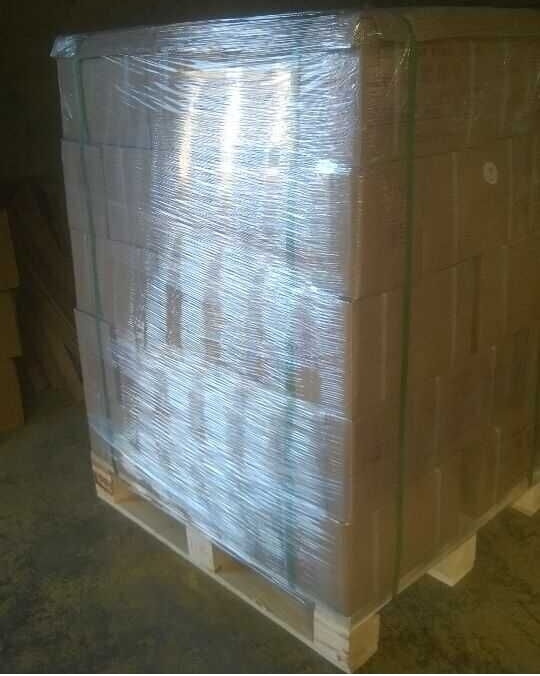
Performance aside,
the applicability of the 7018 welding rod is a key consideration. Its compatibility with AC and DC electrode negative currents broadens its utility across different welding systems, making it a versatile choice for numerous contexts, from structural beams to pipelines. Superior mechanical properties, including yield strength and elongation, solidify its reputation, particularly in settings that impose stringent standards on weld quality.
3 32 welding rod 7018
In the field, welders frequently corroborate the rod’s reliability through shared experiences of successful applications. Testimonials often highlight the rod’s ability to deliver results under challenging scenarios, citing its consistent performance across diverse strenuous conditions. To the practiced professional, the 7018’s dependability is more than a feature; it is a testament to engineering finesse and innovation in welding technology.
Worth noting is the skill level required to harness the power of the 7018 rod effectively. While entry-level welders may find it forgiving to an extent due to its smooth arc and ease of control, achieving optimal results consistently mandates a level of expertise. Techniques such as knowing the right travel speed and maintaining the appropriate rod angle are crucial skills that experienced welders develop over time.
The competitive landscape of welding rods showcases many alternatives, but the legacy and demand for the 7018 continue to lead the market. Its proven track record over decades in commercial, industrial, and even artistic applications resonate in its persistent popularity among professionals. This enduring preference underscores not just a choice in welding materials but a collective trust in its performance and reliability.
In conclusion, the 7018 welding rod holds an esteemed position within the welding community, representing a culmination of quality, versatility, and trust. For projects requiring a blend of strength and precision, few options come close to its capabilities. Welding professionals, by sharing both laboratory data and field anecdotes, cement the 7018's status as an essential component in successful welding endeavors. The rod not only exemplifies technical proficiency but also builds a bridge of trust between manufacturers and the end users who depend on its steady performance day in and day out. As welding processes evolve, the 7018 welding rod remains a steadfast mainstay, illustrating the timeless synergy of engineering excellence and practical labor.