7024 welding electrodes have emerged as a versatile and reliable solution in the world of metal fabrication and repair. These electrodes, known for their exceptional performance, are specifically designed to meet the demands of welding applications involving low to medium carbon steels. A good understanding of their unique characteristics can make a significant difference in the quality and efficiency of welding projects.
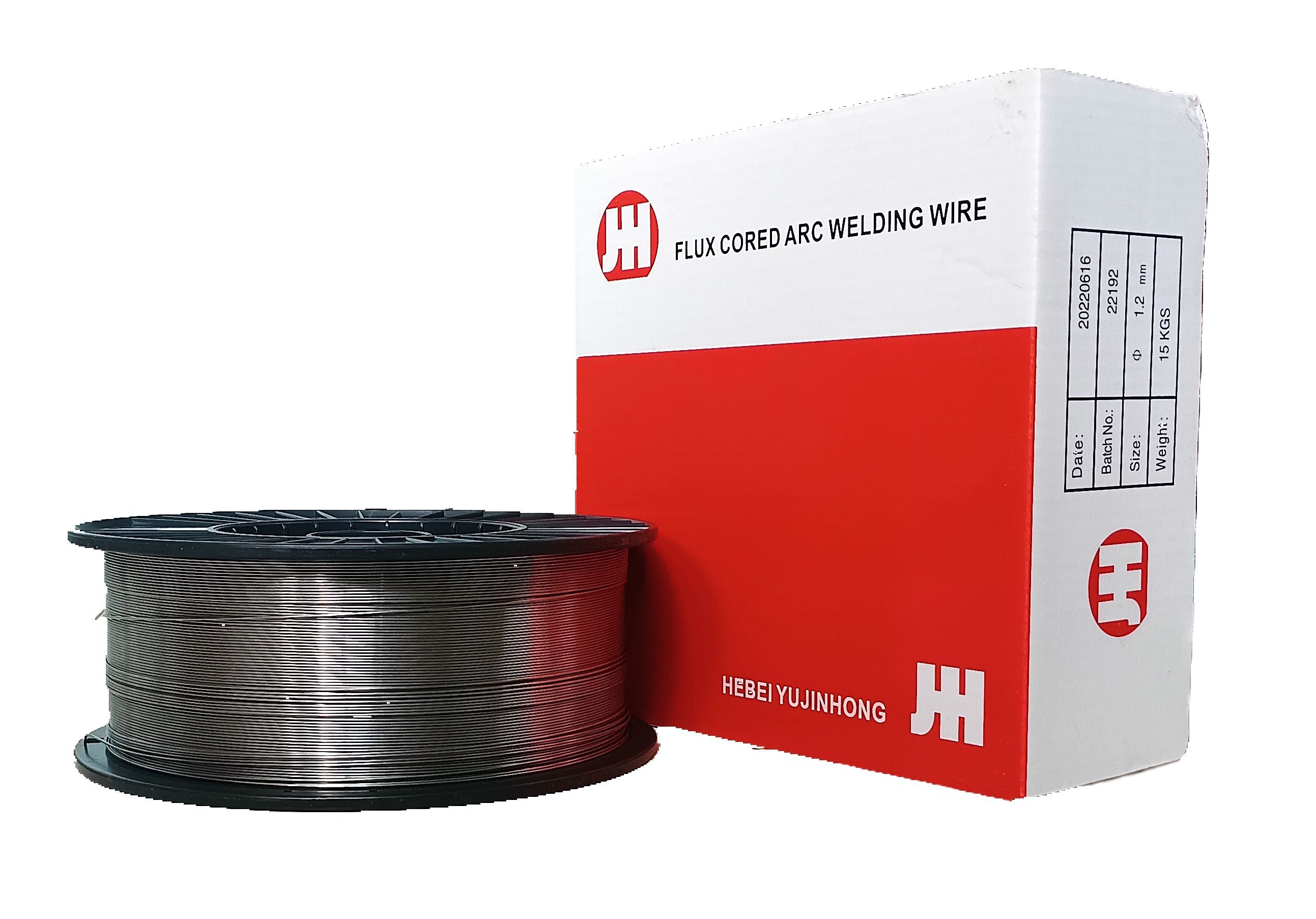
One of the standout features of 7024 electrodes is their formulation, which includes a substantial amount of iron powder in the flux coating. This attribute makes them a preferred choice for high-speed welding operations, as the iron powder enhances the deposition rate. Welders often choose 7024 electrodes for jobs that require a fast fill rate, making them ideal for situations where large amounts of metal need to be deposited in a short amount of time.
Typically used in flat and horizontal positions, 7024 electrodes allow for smooth bead appearance and minimal spatter, contributing to high-quality welds. Their usability is further enhanced by their ability to operate effectively with AC or DC+ (direct current positive) currents, offering flexibility that many professional welders find invaluable in complex projects. This adaptability allows welders to select the power source most suitable for their specific needs without compromising the weld quality.
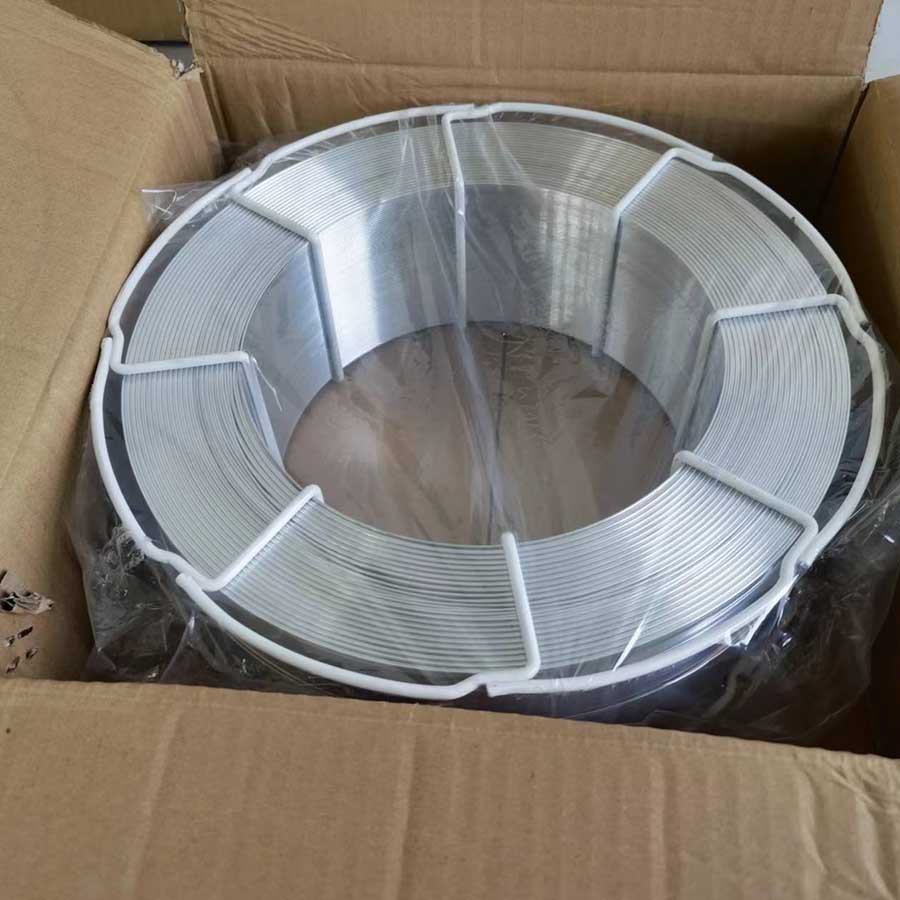
The proficiency of 7024 welding electrodes in delivering robust and aesthetically pleasing welds, however, does not come without expertise.
Successful application demands an understanding of specific parameters and techniques. For instance, controlling the travel speed and maintaining a proper arc length are crucial for maximizing the electrodes' benefits. A short arc length minimizes the risk of porosity and ensures a stable arc, which is essential for achieving sound welds.
Another critical aspect that underscores the expert use of 7024 electrodes is the importance of electrode storage and handling. To maintain their performance integrity, electrodes should be stored in a dry environment, away from moisture, which can compromise the flux coating and lead to inferior welds. Professional welders understand the necessity of conditions free from humidity and handle electrodes with care to avoid damaging the coating.
7024 welding electrode
Those who master the use of 7024 electrodes appreciate their efficiency in producing welds with excellent mechanical properties, which is why they are often employed in heavy-duty construction projects, such as structural welding. Their capability to provide high penetration and strong, crack-resistant welds make them trusted tools in the construction of bridges, ships, and industrial structures. This endorsement by industry professionals speaks to the electrodes' authority and reliability in critical applications.
Moreover, the expertise required for using 7024 welding electrodes extends to recognizing the types of tasks they are most suited for. Although they are exceptional for specific applications, they are not the universal solution for all welding needs. Recognizing situations that demand more versatile electrodes, like vertical or overhead positions, is crucial for welders aiming to maintain high standards of craftsmanship.
Trustworthiness in using 7024 electrodes is further emphasized by adhering to safety protocols. Ensuring a clean work environment, protective gear, and understanding of material properties minimizes the risks associated with welding operations. Trust in the welding process is built through consistent practice and attention to detail, fundamentally impacting the quality of the final product.
In conclusion, 7024 welding electrodes are an invaluable asset for those involved in the welding industry due to their ability to deliver efficient and high-quality results in appropriate applications. Their successful use reflects a balance of expertise, experience, and meticulous attention to the details of the welding process. By leveraging these electrodes' unique properties, skilled professionals can achieve superior outcomes, reinforcing the electrodes' esteemed position within the welding community. As advancements in materials and techniques continue, maintaining a deep understanding of electrodes like 7024 will ensure ongoing success and safety in metal fabrication and repair endeavors.