The Art and Science of Electrode Welding A Comprehensive Overview
Electrode welding, also known as arc welding or stick welding, is a fundamental process in the world of metal fabrication and construction. This method, dating back to the early 20th century, has stood the test of time due to its versatility, simplicity, and effectiveness.
At its core, electrode welding relies on an electric current to create an intense heat source, which melts the base metal and a consumable electrode to form a weld. The electrode, coated with a flux material, not only conducts the current but also provides shielding against atmospheric contamination, ensuring a clean and strong joint.
The process begins with the application of an electric current between the workpiece and the electrode. When the current flows, it creates an electric arc, which can reach temperatures of over 5,000 degrees Celsius. The heat generated from this arc melts both the electrode and the base metal, creating a pool of molten metal. The flux coating on the electrode disintegrates upon heating, releasing gases that protect the weld area from oxidation and nitrogen absorption.
One of the key advantages of electrode welding is its ability to work in various environments. Unlike other welding methods, it can be performed outdoors or in areas with less than ideal conditions, thanks to the protective shield provided by the flux. Additionally, the process allows for the welding of thicker materials, making it a preferred choice for heavy-duty applications such as shipbuilding, bridge construction, and pipeline repairs Additionally, the process allows for the welding of thicker materials, making it a preferred choice for heavy-duty applications such as shipbuilding, bridge construction, and pipeline repairs
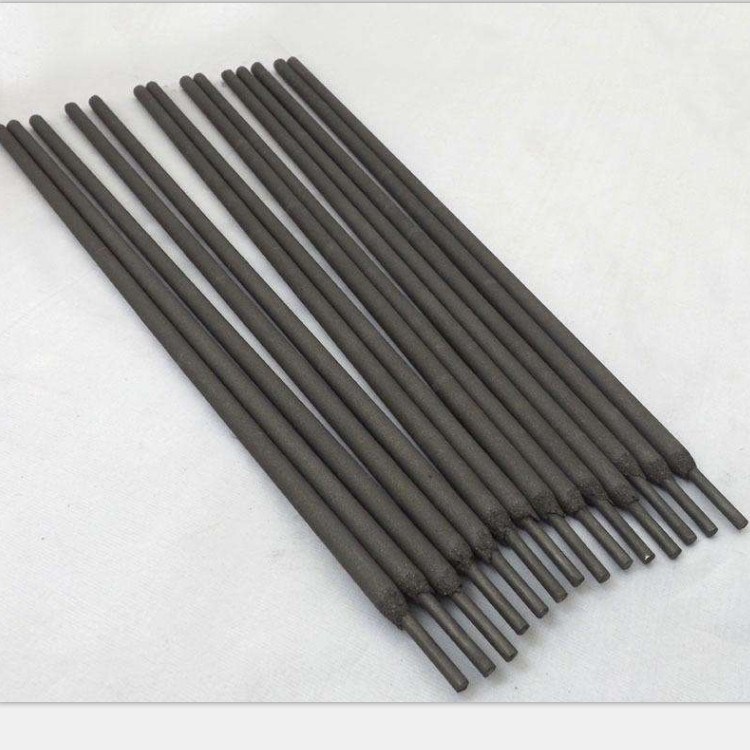
Additionally, the process allows for the welding of thicker materials, making it a preferred choice for heavy-duty applications such as shipbuilding, bridge construction, and pipeline repairs Additionally, the process allows for the welding of thicker materials, making it a preferred choice for heavy-duty applications such as shipbuilding, bridge construction, and pipeline repairs
electrode welding.
Despite its robustness, electrode welding does have its challenges. It requires a steady hand and a good understanding of the process to control the arc and prevent spatter. The type of electrode used is crucial, as different coatings produce welds with distinct properties. For instance, a rutile electrode provides a cleaner weld with less slag, while a basic electrode is suitable for all-position welding.
In conclusion, electrode welding is a blend of art and science, requiring skillful execution and a deep understanding of metallurgy. Its durability, adaptability, and simplicity have secured its position in the welding industry for decades. As technology advances, electrode welding continues to evolve, with new electrodes and techniques enhancing efficiency and quality. However, its fundamental principle remains unchanged - harnessing the power of electricity to forge metals together, creating structures that stand the test of time.