Understanding Aluminum Mig Wire A Comprehensive Guide
Aluminum MIG welding wire, also known as Metal Inert Gas welding wire, is a crucial component in the process of welding aluminum and its alloys. This advanced welding technique has revolutionized the manufacturing and engineering industries due to its efficiency, speed, and precision.
MIG welding, in general, involves using a continuous wire feed as an electrode, which is melted by an electric arc and then fused with the base metal. In the case of aluminum, it presents unique challenges due to its high thermal conductivity and tendency to oxidize rapidly. The use of aluminum MIG wire addresses these challenges effectively.
Aluminum MIG wire is typically made from a blend of aluminum, magnesium, silicon, or other elements, depending on the application and the type of aluminum being welded. It comes in various diameters and chemical compositions to suit different welding requirements. For instance, ER4043 is a common alloy used for general-purpose welding, while ER5356 is more suitable for higher strength applications.
One key aspect of aluminum MIG welding is the use of an inert gas, usually argon or a mix of argon and helium, to shield the welding arc and molten puddle from atmospheric contamination. This gas shield ensures a clean and consistent weld, preventing oxidation that could weaken the joint This gas shield ensures a clean and consistent weld, preventing oxidation that could weaken the joint
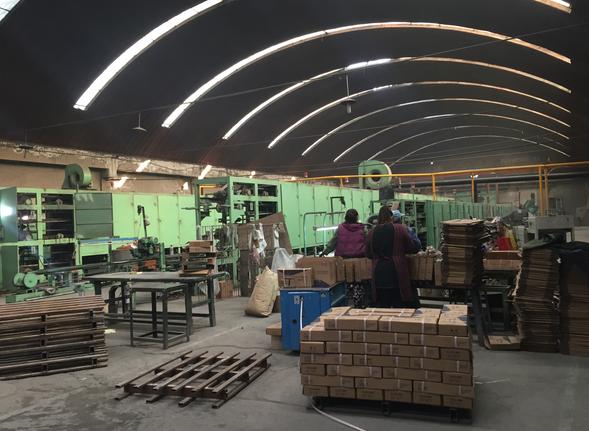
This gas shield ensures a clean and consistent weld, preventing oxidation that could weaken the joint This gas shield ensures a clean and consistent weld, preventing oxidation that could weaken the joint
aluminum mig wire.
The selection of the right aluminum MIG wire depends on factors such as the thickness of the material, the desired mechanical properties, and the welding position. Thicker wires are generally used for thicker materials, while thinner wires provide better control and penetration for thinner metals.
To optimize welding performance, it's essential to consider the welding machine settings, including voltage, wire feed speed, and travel speed. These parameters need to be finely tuned to achieve the best results, minimizing spatter, ensuring deep penetration, and producing a smooth, clean weld.
In conclusion, aluminum MIG wire is a versatile tool in modern welding practices, offering advantages in speed, precision, and versatility. Its proper selection and usage can significantly enhance the quality and efficiency of aluminum welding projects. Whether in automotive, aerospace, or construction industries, understanding and leveraging the potential of aluminum MIG wire can lead to superior welding outcomes and stronger, more reliable structures.