The landscape of welding technology has seen substantial innovations, with CO2 solid welding wire emerging as a pivotal player revolutionizing industrial applications. Renowned for its efficiency and superior metallurgical qualities, CO2 solid welding wire is increasingly becoming the go-to choice for professional welders worldwide.
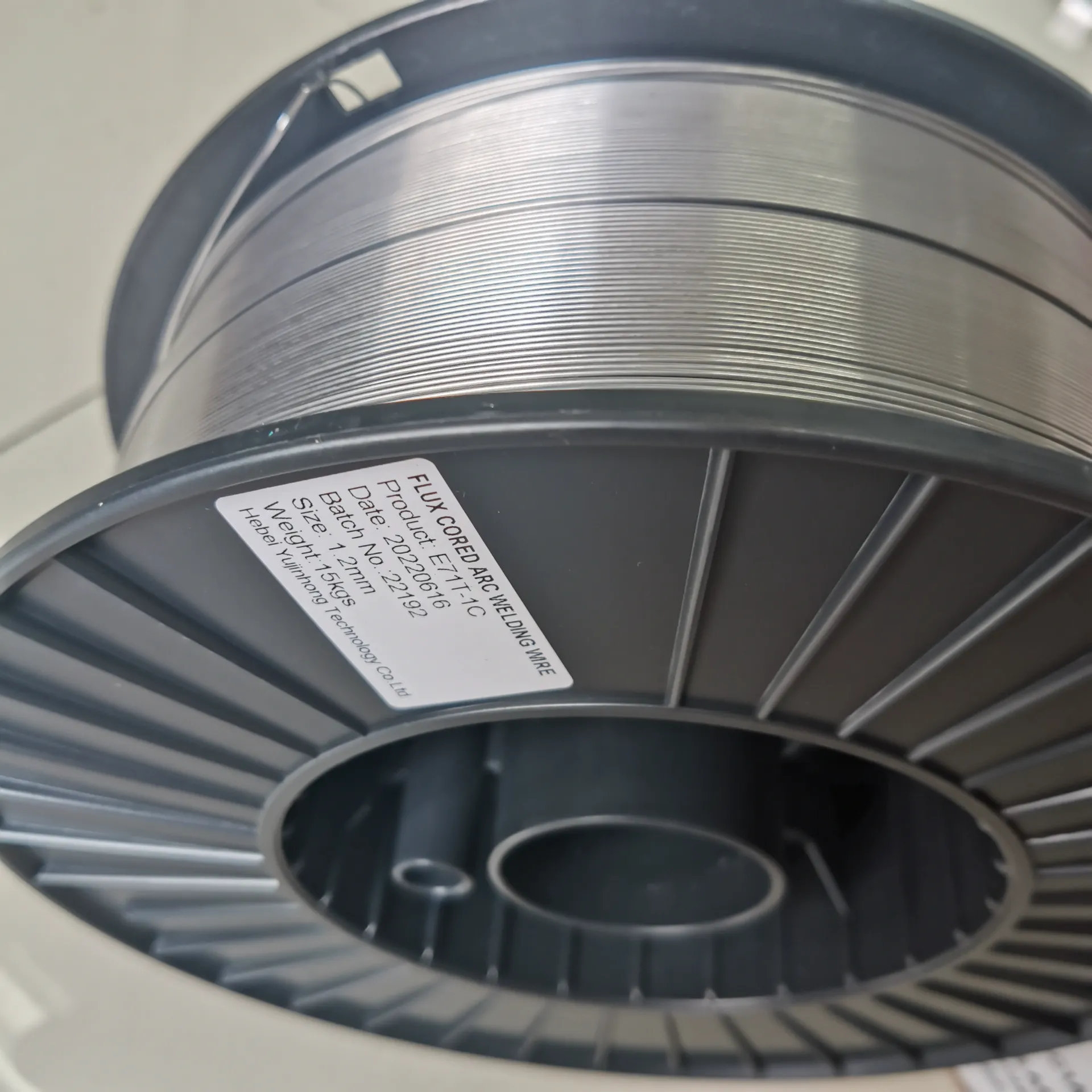
In the bustling adventure of metal fabrication, CO2 solid welding wire stands out for its consistency and precision in delivering high-quality welds. Distinguished from traditional welding methods, the use of CO2 gas as a shielding agent offers robust protection against atmospheric contamination during the welding process. This results in stronger, more durable welds with minimal porosity, thereby enhancing the structural integrity of the finished product.
Professional welders often emphasize the enhanced arc stability and reduced spatter achieved with CO2 solid welding wires. These characteristics streamline the welding process, reducing the need for post-weld cleanup and thereby improving productivity. Its uniform composition further contributes to consistent weld bead formations, which is crucial for projects demanding precision and strength.
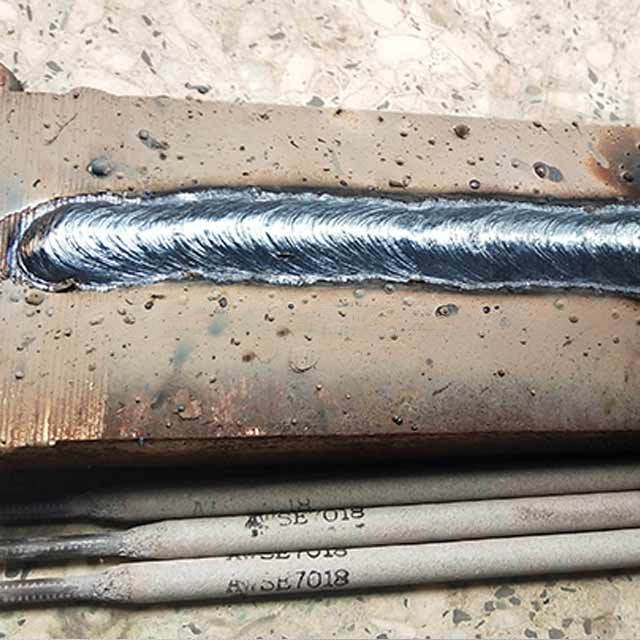
From an expertise standpoint, CO2 solid welding wire is formulated to provide excellent weldability across a variety of metals, including carbon steel and certain grades of stainless steel. This versatility is particularly influential in industries such as automotive, shipbuilding, and industrial fabrication, where the demands for precision and durability are extraordinarily high. Engineers and welders appreciate the wire's adaptability, which accommodates different welding positions and methods, ranging from flat welds to overhead techniques.
co2 solid welding wire
Technical assessments and experiential feedback highlight the wire's effectiveness in reducing common welding defects. Its chemistry is optimized to minimize incidents of incomplete fusion, undercutting, and slag inclusions, translating into higher-quality, reliable welds. Consequently, this fosters greater confidence among engineers and project managers in the materials' performance in structural applications.
Industry experts advocate for CO2 solid welding wire not just for the mechanical properties it imparts to welds but also for its economic advantages. The efficiency gained from reduced welding time and lower wastage through minimized spatter translates into cost savings over large-scale projects. Furthermore, its compatibility with automated welding systems enhances its appeal in modern manufacturing environments, where speed and precision are paramount.
Trust in CO2 solid welding wire is underpinned by its consistent performance and widespread adoption in critical infrastructure projects. Regulatory bodies and quality assurance engineers often cite its role in enhancing safety standards due to the reliable, high-strength welds it produces. These attributes are vital in sectors where even minor welding failures can pose significant safety risks.
In conclusion,
CO2 solid welding wire represents a paradigm shift in welding technology. Its deployment in various applications underscores a synthesis of technical prowess and practical utility, essential for modern welding demands. As industries continue to evolve, the adoption of CO2 solid welding wire signals a commitment to advancing welding techniques that prioritize efficiency, quality, and safety without compromise.