MIG welding wire, also known as Metal Inert Gas welding wire, is an essential component in the MIG welding process, a widely used metal fabrication technique. This type of welding wire serves as the filler material that joins two metal pieces together, making it a critical element in various industries, from automotive and construction to manufacturing and engineering.
MIG welding wire is typically made from a continuous spool of metal, available in different diameters and materials, such as steel, aluminum, stainless steel, and others. The choice of wire depends on the type of metal being welded and the desired quality of the weld. For instance, mild steel wires are commonly used for general-purpose welding, while aluminum wires are suitable for lightweight materials.
The welding wire's composition plays a crucial role in the welding process. It not only fills the joint but also influences the mechanical properties, corrosion resistance, and appearance of the weld. The wire is fed through a welding gun, which also supplies an inert gas, usually argon or carbon dioxide, to shield the arc and protect the molten puddle from atmospheric contamination.
One of the key benefits of MIG welding wire is its efficiency. Its continuous feed allows for a faster welding speed compared to other methods, making it ideal for large-scale projects Its continuous feed allows for a faster welding speed compared to other methods, making it ideal for large-scale projects
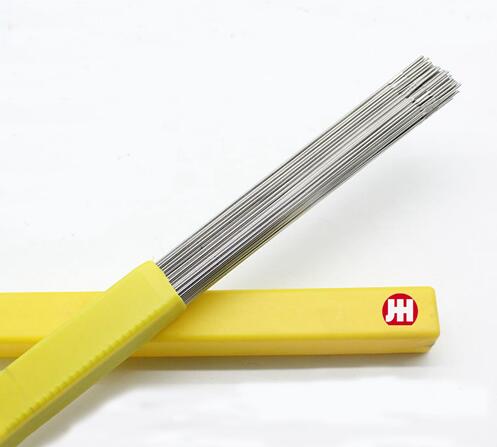
Its continuous feed allows for a faster welding speed compared to other methods, making it ideal for large-scale projects Its continuous feed allows for a faster welding speed compared to other methods, making it ideal for large-scale projects
mig welding wire. Additionally, the process is relatively easy to learn, making MIG welding popular among professionals and hobbyists alike.
However, selecting the right MIG welding wire and understanding its properties is paramount. The wrong wire can lead to poor weld quality, increased porosity, or even complete failure of the weld. Factors such as the wire's chemical composition, diameter, and the welding machine settings must be carefully considered to achieve optimal results.
In conclusion, MIG welding wire is more than just a simple consumable; it's a fundamental element in the precision and effectiveness of the MIG welding process. Its versatility, combined with its ability to provide strong, clean welds at high speeds, has solidified its position as a staple in modern welding practices. As technology advances, so does the development of MIG welding wires, promising even greater efficiency and weld quality in the future.