Understanding Mig Wire Sizes in Factory Production
MIG (Metal Inert Gas) welding, a popular welding process in industrial settings, significantly relies on the correct selection of wire size for optimal performance and efficiency. The mig wire sizes in factory production play a crucial role in determining the quality, speed, and overall effectiveness of the welding process.
Factory operations often involve a wide range of materials and thicknesses, necessitating a variety of mig wire sizes to accommodate these differences. Mig wire, typically made from steel or aluminum, is a continuous consumable electrode that melts during the welding process, creating a fusion between the base metals.
Wire diameter is measured in millimeters and directly impacts the welding parameters such as amperage, travel speed, and deposition rate. Thicker wires, generally 1.0mm to 1.6mm, are used for heavier applications and thicker materials, while thinner wires, around 0.6mm to 0.8mm, are suited for lighter work and thinner metals. Factories often stock a comprehensive range to cater to diverse production needs.
In a factory setting, the mig wire size selection is not arbitrary but is based on a series of factors
In a factory setting, the mig wire size selection is not arbitrary but is based on a series of factors
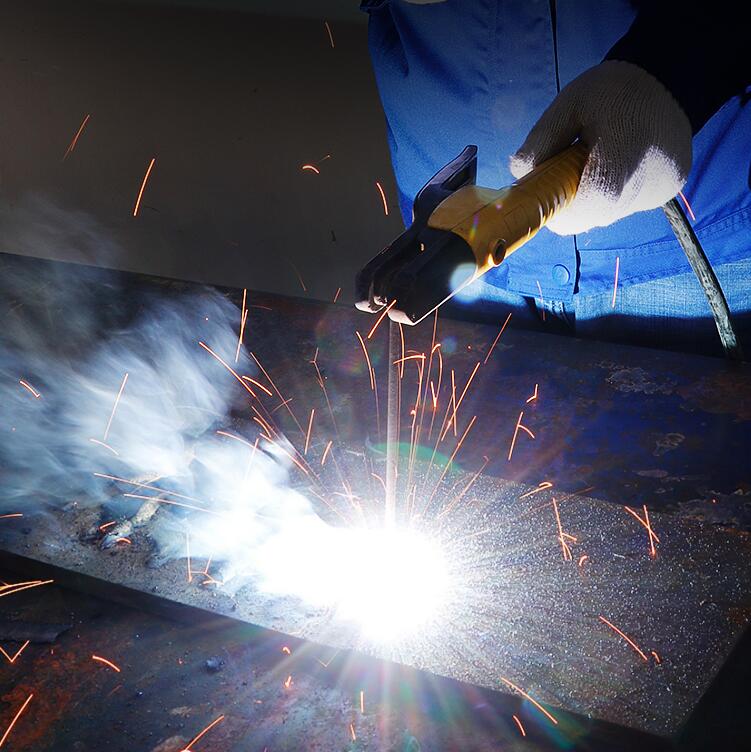
In a factory setting, the mig wire size selection is not arbitrary but is based on a series of factors
In a factory setting, the mig wire size selection is not arbitrary but is based on a series of factors
mig wire sizes factory. These include the material being welded, the desired welding speed, the type of shielding gas used, and the power source's capabilities. A larger wire diameter can increase welding speed and deposition rate, making it suitable for high-production factory lines where efficiency is paramount. Conversely, smaller wires offer greater precision and control, ideal for intricate or thin-sheet welding tasks.
Moreover, the mig wire size also affects the heat input, which can influence distortion, weld penetration, and the overall quality of the joint. Factory engineers must strike a balance to prevent overheating and ensure a strong, clean weld.
Factories often have stringent quality control measures in place to ensure the correct mig wire size is used for each job. This includes proper storage to maintain wire integrity, regular equipment maintenance, and operator training to understand the impact of wire size on welding outcomes.
In conclusion, mig wire sizes in factory production are a critical element that drives productivity, quality, and safety. It is a testament to the interplay between engineering design, materials science, and manufacturing processes. By understanding and optimizing this aspect, factories can enhance their welding operations, minimize waste, and ultimately drive profitability.