Mastering the art and science of MIG (Metal Inert Gas) wire welding can transform mundane construction and manufacturing tasks into works of precision and durability. This technology, crucial for an array of industries, demands expertise and a commitment to quality. As someone who has spent years in welding workshops and laboratories, I have witnessed firsthand both the potential and pitfalls of MIG wire welding. This article unpacks the nuances of this process, enriched by experience and guided by technical authority, to provide you with a trustworthy guide on leveraging MIG wire welding like a seasoned professional.
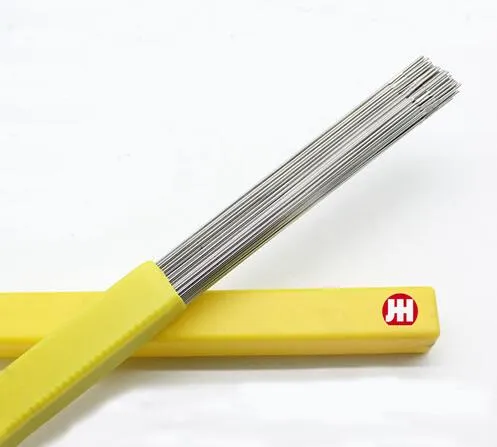
The essence of effective MIG wire welding lies in understanding its components and how they synergize to produce a seamless weld. At the heart of this technology is the welding wire itself, which serves as the filler material. It's fed through a welding gun, where it melts and mixes with a specific inert gas, often Argon or CO2, to protect the weld pool from contaminants. This combination ensures a clean, efficient weld.
Choosing the right wire is paramount. Mild steel wires, such as ER70S-6, are popular due to their versatility and efficiency. They're tailored to work well with a variety of metals and coatings, and under different environmental conditions. Stainless steel or aluminum wires, on the other hand, require more specificity in terms of equipment settings and shielding gases, due to their distinctive thermal and physical properties. This selection process demands a nuanced understanding of both the material and expected welding conditions.
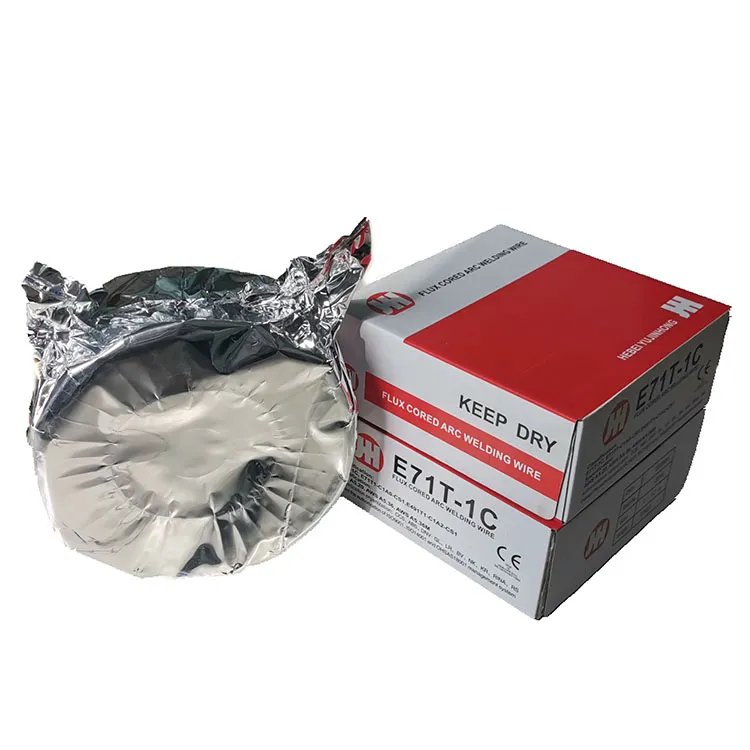
The practical experience of setting the correct voltage and wire feed speed distinguishes novices from seasoned professionals. Every material and wire requires specific machine settings to achieve optimal penetration and bead size. For instance, aluminum welding typically demands a higher amperage as opposed to mild steel, due to its excellent thermal conductivity. Calibration of these settings is a matter of practice and precision, and greatly influences the weld’s quality and durability.
Another critical aspect of MIG wire welding is maintaining a consistent welding technique. Positioning, torch angle, speed, and distance can dramatically affect the quality of the weld. Holding the torch at a 10 to 15-degree angle is generally recommended, moving at a steady pace without abrupt stops to ensure a smooth, even finish. Variations in technique can cause undercutting, inadequate penetration, or even structural weaknesses.
mig wire welding
A robust weld relies equally on meticulous preparation. Cleaning the workpiece to remove rust, paint, or other contaminants is essential. Any debris can interfere with the integrity of the weld, leading to potential failures. Utilizing a wire brush or grinder is a common practice that promotes a strong, clean weld.
Troubleshooting issues before they escalate is part of the expertise in MIG wire welding. Common problems such as porosity, spatter, or incomplete fusion can often be traced back to improper settings, inadequate cleaning, or poor technique. Developing the skill to identify and correct these issues on the fly is what defines a competent welder.
Investing in quality equipment is non-negotiable. Reliable MIG welders, often from trusted brands, ensure stable performance and durability. Regular maintenance of these machines, such as replacing worn contact tips and ensuring proper spool tension, pays dividends in extending their lifespan and reliability.
Leveraging personal protective equipment (PPE) is mandatory. Despite the advanced technology, MIG welding exposes operators to substantial risks, including UV radiation, fumes, and molten spatter. High-quality helmets, gloves, and jackets are essential to ensure safety and protection, reducing the likelihood of accidents and health hazards.
In conclusion, the mastery of MIG wire welding emerges from a blend of technical knowledge, practical experience, and a commitment to maintaining industry standards. By honing your technique, investing in quality gear, and prioritizing safety, you can leverage MIG wire welding to produce results that stand the test of time, positioning yourself as a true expert in this indispensable field.