Understanding the Significance of 7014 Welding Rods A Manufacturer's Perspective
In the world of welding, the choice of materials plays a crucial role in determining the quality and durability of the final product. Among the various welding rods available, the 7014 welding rod stands out for its unique properties and versatility. This article delves into the intricacies of this type of welding electrode, highlighting the importance of its manufacture and the impact it has on the welding industry.
A 7014 welding rod is an alloy steel electrode, known for its high-strength characteristics and excellent impact resistance. The '70' in the name denotes the tensile strength of the weld in thousands of pounds per square inch (ksi), while the '14' refers to the percentage of iron oxide coating on the rod. It is primarily used in the construction of heavy machinery, bridges, and other structures that require robust, long-lasting welds.
Manufacturing 7014 welding rods involves a meticulous process. The raw materials, usually a blend of steel and specific alloys, are first melted and then formed into the desired rod shape. The surface is then coated with a flux material, which helps protect the weld from atmospheric contamination during the welding process. The coating also aids in generating a stable arc and producing a smooth, clean weld bead.
The manufacturing process of 7014 welding rods requires precision and expertise. The composition of the flux coating, the diameter of the rod, and the heat treatment after fabrication all significantly influence the performance of the electrode. Manufacturers need to adhere to strict quality control measures to ensure consistent quality, as even minor variations can affect the weld's mechanical properties Manufacturers need to adhere to strict quality control measures to ensure consistent quality, as even minor variations can affect the weld's mechanical properties
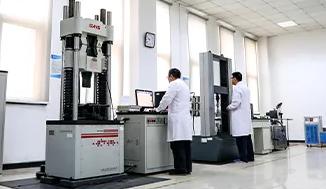
Manufacturers need to adhere to strict quality control measures to ensure consistent quality, as even minor variations can affect the weld's mechanical properties Manufacturers need to adhere to strict quality control measures to ensure consistent quality, as even minor variations can affect the weld's mechanical properties
7014 welding rod manufacturer.
One of the key advantages of 7014 welding rods is their user-friendliness. They operate at relatively low currents, making them suitable for beginners and experienced welders alike. Moreover, they produce less spatter and have a shallow penetration profile, making them ideal for thin sheet metals and applications where distortion needs to be minimized.
However, selecting the right 7014 welding rod manufacturer is crucial. A reputable manufacturer will not only guarantee the quality of the product but also provide technical support and guidance to optimize welding processes. They invest in research and development to continually improve the performance of their welding rods, adapting to the evolving needs of the industry.
In conclusion, the 7014 welding rod is a testament to the power of engineering in the welding sector. Its manufacture is a blend of science, technology, and artistry, resulting in a tool that is both functional and adaptable. As a welding rod manufacturer, understanding the significance of these elements is vital in delivering products that meet the stringent demands of modern welding applications. The 7014 welding rod, therefore, remains a staple in the hands of welders worldwide, a symbol of reliability and craftsmanship in a constantly evolving industry.