Understanding TIG and MIG Welding Wires Key Differences and Applications
TIG (Tungsten Inert Gas) and MIG (Metal Inert Gas) welding are two widely used welding techniques in various industries, each with its own distinct characteristics and applications. A significant aspect of both processes is the welding wire used, which plays a crucial role in the quality and efficiency of the weld.
TIG welding employs a non-consumable tungsten electrode to produce an arc, which melts the base metal. The welding wire in TIG welding, usually made from the same material as the workpiece, is fed through the torch separately. It's commonly available in diameters ranging from 0.8mm to 3.2mm, depending on the thickness of the material being welded. TIG welding wires are typically pure or alloyed, with alloys like aluminum, stainless steel, and titanium being common choices. The purity and composition of the wire significantly affect the weld's mechanical properties and appearance.
On the other hand, MIG welding uses a continuous wire feed as both the electrode and filler material. MIG welding wires are available in a broader range of materials, including carbon steel, stainless steel, and aluminum. They come in different sizes and diameters, with the most common being 0 They come in different sizes and diameters, with the most common being 0
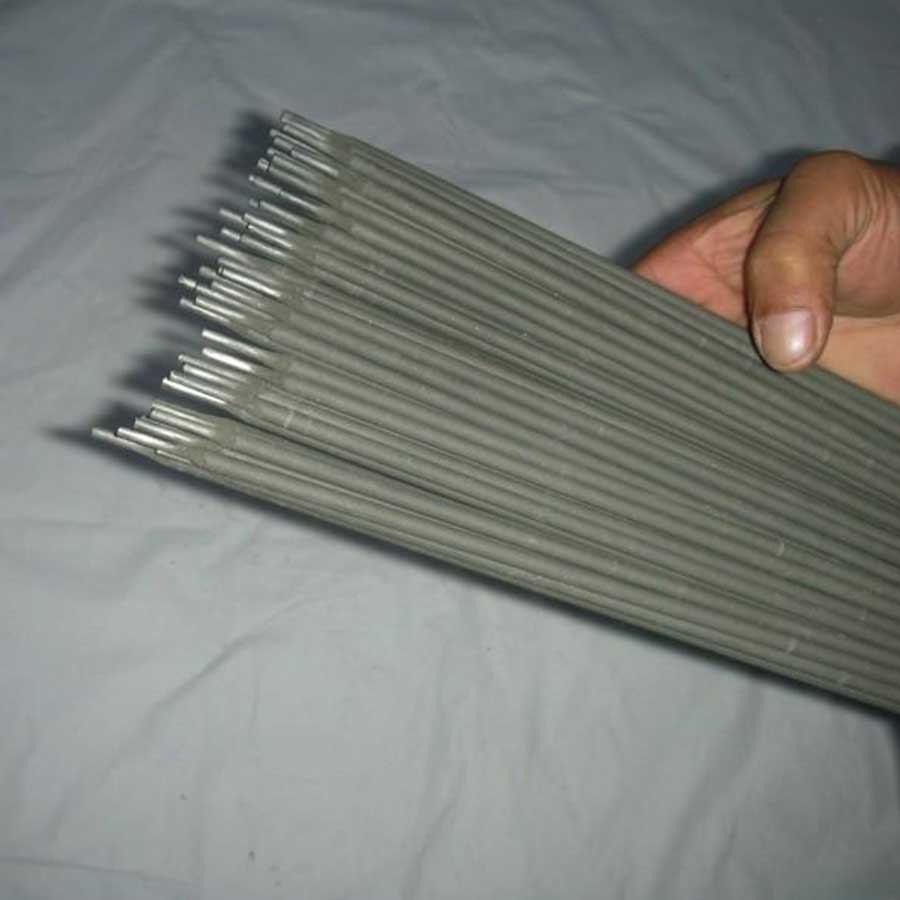
They come in different sizes and diameters, with the most common being 0 They come in different sizes and diameters, with the most common being 0
tig mig welding wire.8mm, 1.0mm, and 1.2mm. The choice of wire depends on factors such as the type of metal, thickness, and desired weld quality. MIG welding wire is often coated with a flux to protect the molten weld pool from contamination.
Both TIG and MIG welding wires have their advantages. TIG welding is renowned for its precision and control, making it ideal for intricate and thin gauge work, while MIG welding is faster and more efficient, suitable for larger, thicker materials or high-production welding tasks.
In conclusion, TIG and MIG welding wires, though serving a similar purpose, differ significantly in their composition, usage, and application. The selection of the right welding wire is critical, as it not only impacts the welding process but also the final product's durability, strength, and aesthetics. Whether it's the fine control of TIG welding or the speed and versatility of MIG welding, understanding the nuances of these welding wires is vital for any professional or hobbyist welder.