Understanding and Utilizing 0.6mm Gasless MIG Wire in Welding Processes
Gasless MIG welding, also known as flux-cored arc welding (FCAW), has become an increasingly popular welding method due to its efficiency and versatility. Among the various types of gasless MIG wires available, the 0.6mm diameter wire stands out for its balanced performance and wide application range.
The 0.6mm gasless MIG wire is a consumable electrode that contains a flux core, which serves as both a conductor and a source of shielding gas. The absence of an external gas supply makes this welding technique more convenient and cost-effective, especially for outdoor or windy conditions where a continuous gas shield might be challenging to maintain.
One key advantage of using 0.6mm gasless MIG wire is its adaptability. It can be used on a variety of materials, including mild steel, low-alloy steel, and even some stainless steels, making it a versatile choice for different welding projects. Its smaller diameter allows for better control and precision, particularly in intricate or thin-sheet welding tasks.
The welding process with 0.6mm gasless MIG wire is relatively simple. The wire feeds through the welding gun, creating an electric arc when it comes into contact with the workpiece The wire feeds through the welding gun, creating an electric arc when it comes into contact with the workpiece
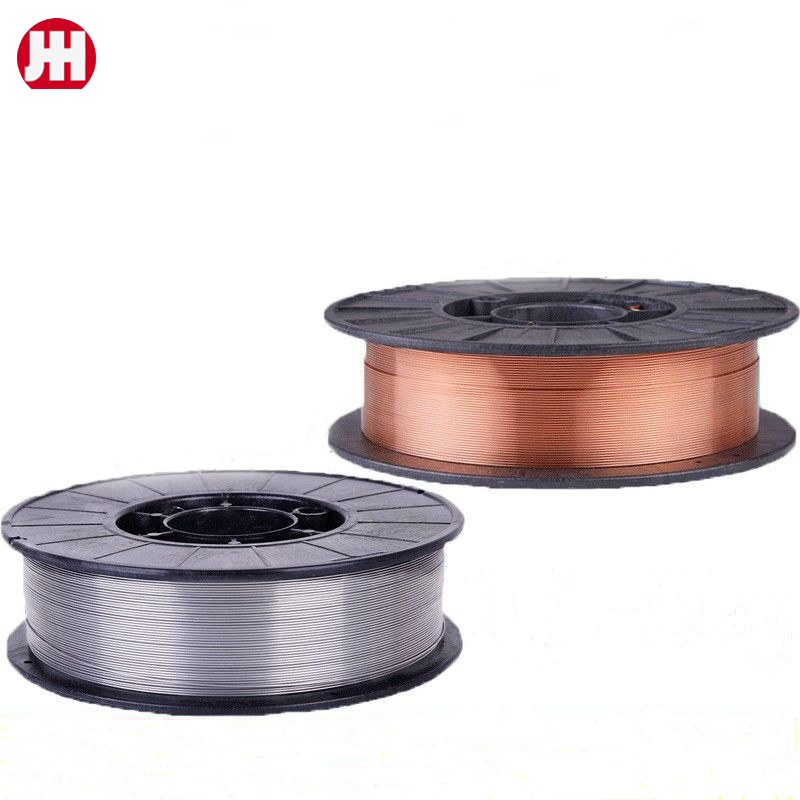
The wire feeds through the welding gun, creating an electric arc when it comes into contact with the workpiece The wire feeds through the welding gun, creating an electric arc when it comes into contact with the workpiece
0.6mm gasless mig wire. The heat generated from the arc melts the wire and the base material, forming a weld pool. The flux core decomposes upon heating, releasing gases that protect the weld area from atmospheric contamination, ensuring a clean and strong joint.
In terms of performance, the 0.6mm gasless MIG wire offers a good balance between penetration depth and fusion, resulting in strong welds without excessive spatter. It also provides a higher deposition rate compared to thicker wires, enabling faster welding speeds and increased productivity.
However, it's essential to consider the specific welding conditions and material thickness when selecting the appropriate wire. Thicker materials may require a larger diameter wire for adequate penetration, while thinner sections can benefit from the finer control offered by the 0.6mm wire.
In conclusion, the 0.6mm gasless MIG wire is a practical and efficient welding solution for professionals and hobbyists alike. Its compact size, combined with its ability to work on a range of materials, makes it a go-to choice for many welding applications. By understanding its properties and proper usage, users can harness the full potential of this welding technology to deliver high-quality, reliable welds.