Understanding Stainless Steel Flux Core MIG Wire for Enhanced Welding Performance
Stainless steel flux core MIG wire, a specialized welding consumable, has revolutionized the metal fabrication industry with its efficiency and versatility. It is a popular choice among welders due to its ability to deliver strong, corrosion-resistant welds in various applications.
MIG, or Metal Inert Gas welding, is a process that involves using a continuous wire feed as an electrode, which melts and fuses the materials together. The 'flux core' aspect of this wire refers to the hollow center filled with flux, a substance that shields the molten weld pool from atmospheric contamination, ensuring a clean, high-quality joint.
Stainless steel flux core MIG wire, typically composed of alloys like 308, 309, or 316, offers several advantages. Firstly, it allows for welding without the need for a shielding gas, making it ideal for outdoor or windy environments where gas protection might be challenging. This feature significantly simplifies the setup process and reduces costs. Secondly, the flux in the wire generates its own protective gas shield, which enhances the penetration and fusion of the metals, even at higher travel speeds.
The flux also helps in removing impurities from the weld, improving the overall quality and integrity of the joint. The self-shielded nature of the wire makes it suitable for thick material, as it can produce deep penetration and strong weld beads The self-shielded nature of the wire makes it suitable for thick material, as it can produce deep penetration and strong weld beads
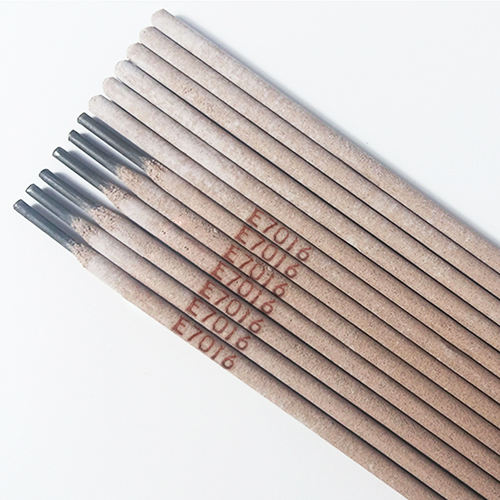
The self-shielded nature of the wire makes it suitable for thick material, as it can produce deep penetration and strong weld beads The self-shielded nature of the wire makes it suitable for thick material, as it can produce deep penetration and strong weld beads
stainless steel flux core mig wire. Moreover, stainless steel flux core MIG wire provides excellent resistance to corrosion, heat, and wear, making it perfect for applications in industries such as food processing, chemical plants, and marine structures.
However, despite its benefits, using stainless steel flux core MIG wire requires skill and understanding. The wire's composition and diameter must be matched to the job at hand, as well as the welding machine's capabilities. Adjustments in voltage and wire feed speed are critical to achieve the desired bead appearance, penetration, and fusion.
In conclusion, stainless steel flux core MIG wire is a game-changer in the welding world, offering convenience, efficiency, and high-quality welds. Its self-shielding properties, coupled with the strength and corrosion resistance of stainless steel, make it a go-to option for professionals seeking robust, reliable welds in diverse conditions. As technology continues to evolve, so does the potential of stainless steel flux core MIG wire, promising even more advanced welding solutions in the future.