Insights into the World of Welding Rod Manufacturers and Factories
The realm of welding rod manufacturers and factories is a fascinating blend of technology, craftsmanship, and industrial expertise. These facilities are the backbone of numerous industries, producing essential materials that ensure the integrity and longevity of structures ranging from bridges and buildings to ships and aircraft. The process of manufacturing welding rods is both an art and a science, requiring precise control over materials and procedures to achieve the desired outcomes.
A typical welding rod manufacturer's factory is a highly organized and specialized environment. It begins with the selection of raw materials—typically steel or aluminum—of specific compositions and qualities. These materials are then cleaned and prepared through processes like drawing, where they are pulled through a series of dies to reach the appropriate diameter. The next critical step is coating the rod with a flux material. This protective layer serves multiple purposes it shields the molten weld pool from impurities, stabilizes the arc, and can add additional alloy elements to the weld.
Manufacturers pay meticulous attention to the formulation of these fluxes, which can be made from a variety of compounds including silicates, alkaline earth metals, and other elements tailored to the specific application needs. After coating, the rods are dried and cured in ovens to ensure the flux adheres properly. Finally, the rods are packaged and prepared for shipment, often with additional quality checks to ensure they meet stringent standards Finally, the rods are packaged and prepared for shipment, often with additional quality checks to ensure they meet stringent standards
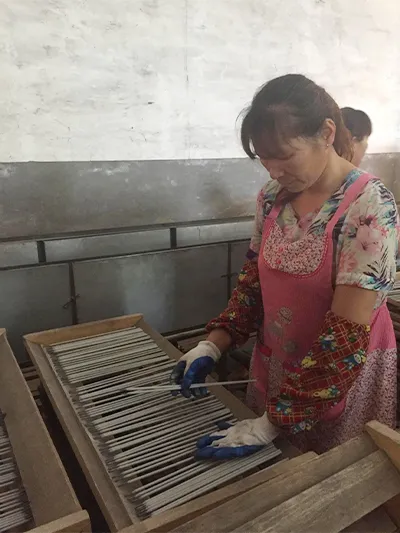
Finally, the rods are packaged and prepared for shipment, often with additional quality checks to ensure they meet stringent standards Finally, the rods are packaged and prepared for shipment, often with additional quality checks to ensure they meet stringent standards
welding rod manufacturers factory.
Innovation plays a crucial role in the welding rod industry. Advanced factories employ cutting-edge technologies such as automated production lines, robotics, and computer-aided design (CAD) systems to enhance efficiency and precision. Moreover, research and development departments continuously explore new materials and coatings to improve welding performance and reduce costs. For instance, the development of low-temperature, high-performance fluxes has revolutionized the welding of sensitive metals like stainless steel and aluminum.
Environmental sustainability is also becoming a focal point within these factories. Many manufacturers are implementing eco-friendly practices such as recycling scrap metal, reducing energy consumption, and using water-based fluxes to minimize hazardous waste. As global standards for environmental stewardship continue to rise, these efforts are not only beneficial for the planet but also serve as a competitive advantage in a market that increasingly values green practices.
In conclusion, the world of welding rod manufacturers and factories is one where tradition meets modernity, where the quest for excellence in materials science intersects with industrial scale production. As these facilities evolve, they continue to play a vital role in ensuring that welding remains a reliable and efficient method of joining metals, securing the infrastructure and safety of our built environment.