The realm of welding has continually evolved, with the welding electrode standing as a pivotal component in the welding industry. For those stepping into the world of metallurgy or even experienced fabricators seeking to enhance their craft, understanding the nuances of welding electrodes is essential.
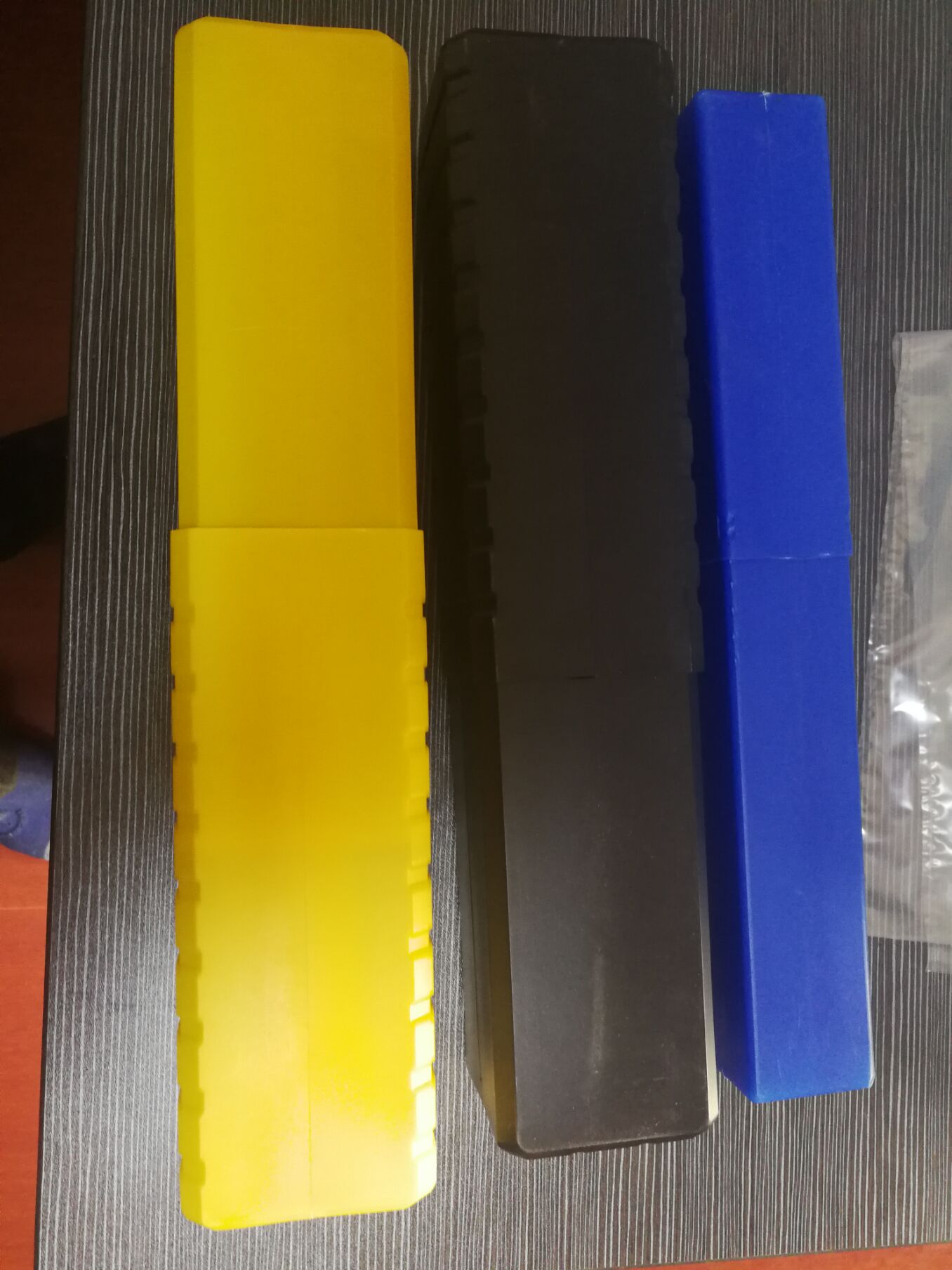
Welding electrodes, commonly perceived as simple consumables, serve a role that transcends merely bridging gaps. They are engineered with precision to enable efficient heat transfer, ensuring that the materials being welded unify seamlessly. Catering to various industrial demands, welding electrodes come in diverse types, each designed to optimize specific welding processes and materials.
An experienced welder’s toolkit nearly always includes a variety of welding electrodes. Different electrodes cater to diverse metals and welding conditions. For instance, mild steel electrodes are popular for their versatility across multiple applications, offering solid performance and reliability. They are typically coated with materials like rutile or cellulose, which aid in stabilizing the arc and improving weld appearance.
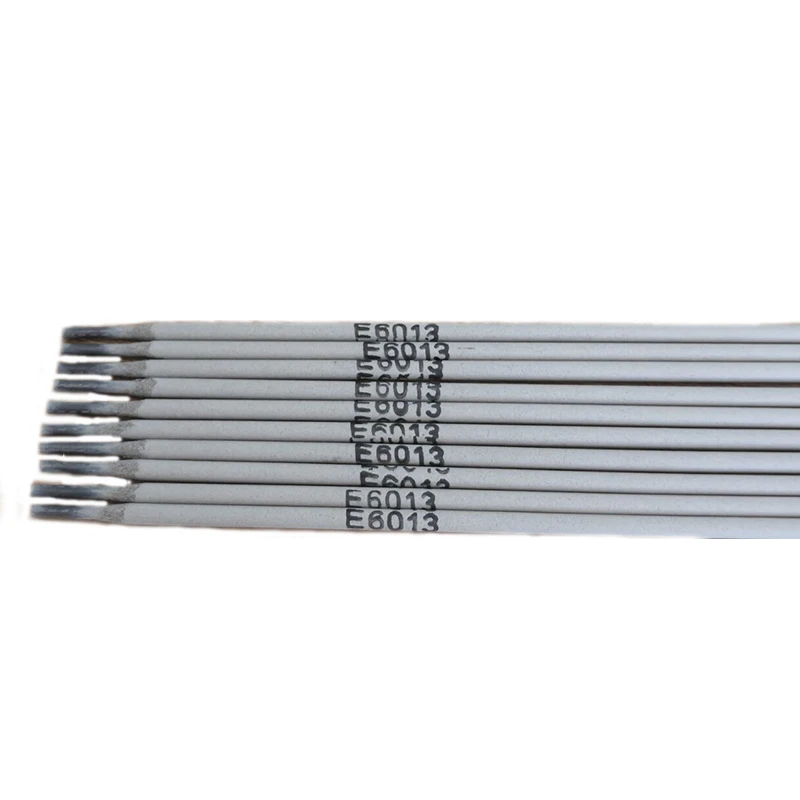
For projects demanding superior strength or corrosion resistance, stainless steel electrodes are invaluable. These electrodes are formulated specifically for stainless steel welds, ensuring that the corrosion-resistant properties of the metal are not compromised. Expertise in handling these electrodes is crucial—welding stainless steel demands precision and attention to detail to prevent issues like distortion or rust.
Low hydrogen electrodes, another significant category, are essential when welding high-strength steels. These specialized electrodes limit hydrogen intake during the welding process, which can otherwise lead to cracking. The industry regards them highly for critical welding tasks where structural integrity is non-negotiable.
welding electrode
The authority in welding disciplines often underscores the importance of selecting the correct electrode size and type as the nuances greatly affect the weld quality. Electrode size impacts the stability of the arc and penetration of the weld, with smaller diameters being preferred for thin materials to prevent burn-through, and larger diameters suited for thicker metals.
Trustworthiness in electrode performance is paramount. Reputable manufacturers ensure rigorous testing and quality control to deliver electrodes that meet specified standards and perform consistently under various operating conditions. Welders trust well-established brands for both personal projects and high-stakes industrial work, knowing that reliability can directly affect safety and structural soundness.
Beyond product selection, welders’ technique and application expertise amplify the actual use of welding electrodes. Regular training on the newest techniques and technology advancements further enhances a welder’s skill set, emphasizing the continuous learning necessary in this dynamic field.
Whether a novice entering the welding industry or a professional refining their craft, the intersection of quality electrodes and informed application cannot be overstated. The conversation continues to evolve, as innovations in electrode formulation and coating technologies emerge, pushing the boundaries of what welders can achieve. Welding electrodes are far from static—they are dynamic tools crucial to the modern evolution of material science and assembly.
In summary, a profound understanding of welding electrodes, coupled with practical experience and industry insights, amplifies a craftsman’s ability to execute precise welds. Mastering the intricate art of electrode selection and usage marks a significant leap in any welder's journey towards excellence.