In the realm of welding, selecting the right electrode is pivotal as it determines the quality, strength, and appearance of the weld. Among the various options available, welding electrodes E7018, 7016, and 6013 have emerged as key choices for professionals seeking different attributes in their welding tasks. This article delves into the specifics of each, offering insights derived from firsthand experiences and authoritative expertise in the field.
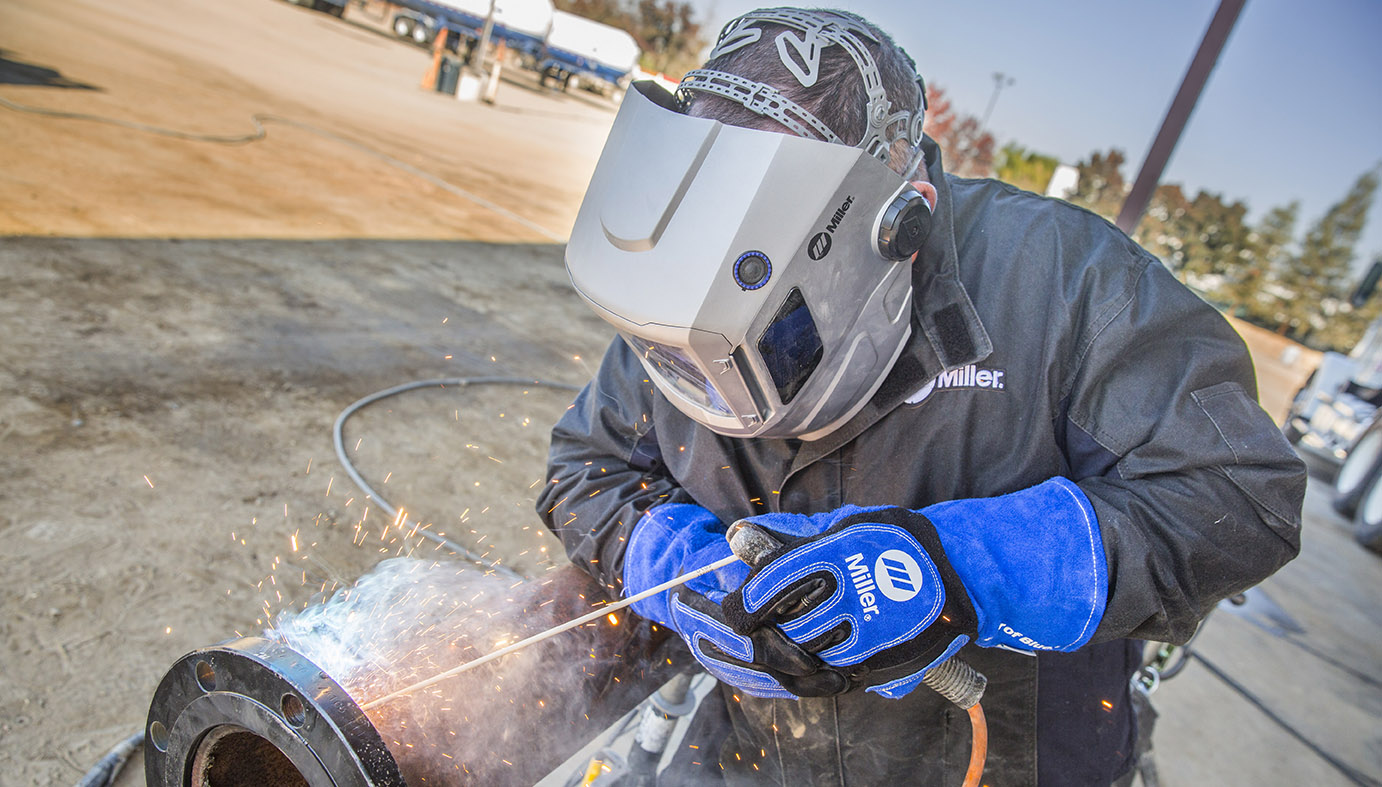
E7018 stands as a staple in the welding industry, revered for its versatility and robustness. It is a low-hydrogen electrode, which significantly reduces the risk of hydrogen-induced cracking – a common issue in welding. This attribute makes E7018 ideal for structural welding where strength is non-negotiable. Professionals often appreciate its smooth weld bead appearance and ease of slag removal, which are critical in maintaining high production standards. From personal experience utilizing E7018, it's evident that this electrode excels in joining heavy metal sections, offering exceptional toughness and ductility. It’s particularly suited for welding carbon steel, especially in thick sections, which are often encountered in construction and heavy equipment manufacturing.
On the other hand, the E7016 electrode brings to the table its own set of specialized benefits. Similar to E7018, E7016 is a low-hydrogen electrode but with certain distinctions. Its welding arc is more stable, providing a cleaner and more controlled welding experience. This makes E7016 a preferred choice for welding in environments that demand precision such as shipbuilding and pipeline projects. The alloying elements in E7016 promote excellent mechanical properties, especially at low temperatures – an attribute that's invaluable in arctic or cold-weather projects. Many seasoned welders trust E7016 when handling projects that require high impact resistance and superior crack resistance. From a professional standpoint, using E7016 signifies prioritizing quality and reliability when working under stringent conditions.
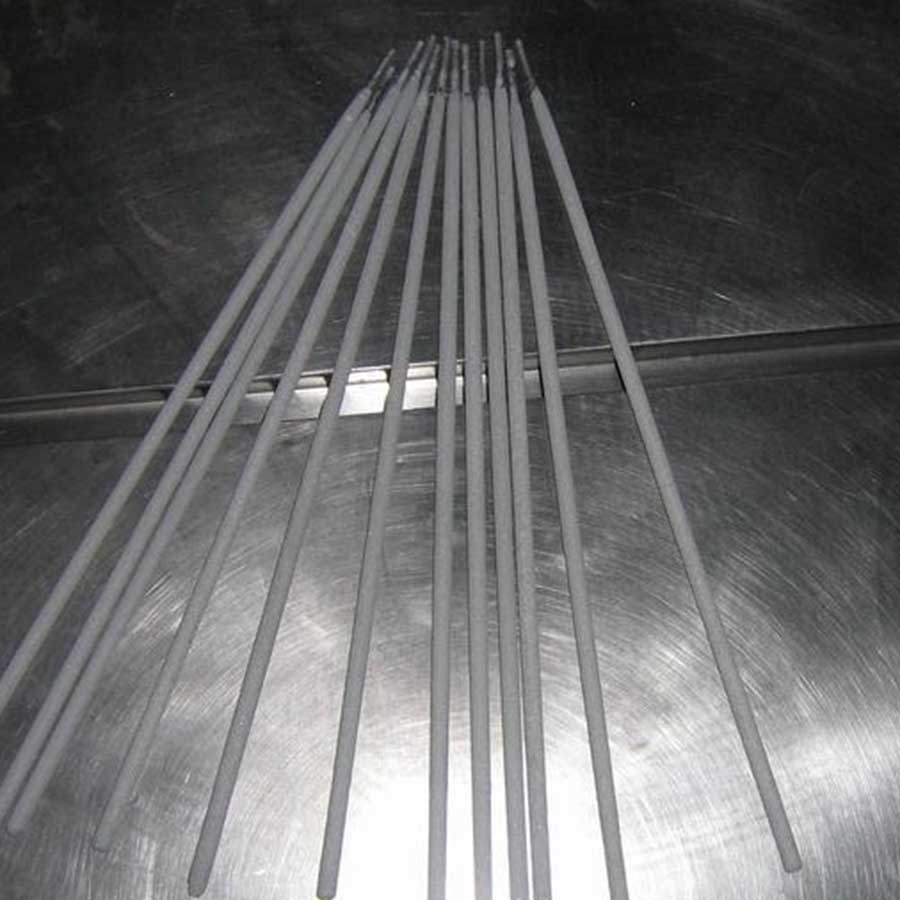
E6013 is often regarded as the go-to electrode for general-purpose welding. Unlike E7018 and E7016, which are more specialized, E6013 is known for its user-friendly attributes, making it extremely popular among hobbyists and in educational settings. The smooth, stable arc and easy slag removal of E6013 make it well-suited for light fabrication and repair work. Its ability to function well with AC power sources adds to its versatility, making it applicable in diverse working environments. Those who have worked extensively with E6013 often highlight its effectiveness in creating clean welds on thinner materials, such as sheet metal, without the fear of burn-through that might occur with more aggressive electrodes.
welding electrode e7018 7016 6013
While each of these electrodes offers distinct advantages, the choice ultimately depends on the specifics of the welding project at hand. Expertise in identifying the correct electrode is developed through practice and an understanding of the materials being welded. For instance, while E7018 is chosen for its strength in structural applications, E6013 might be selected for its adaptability in less demanding tasks. The monitored application and observation of outcomes are vital in mastering the application of these electrodes, strengthening the weld, and optimizing cost-efficiency without compromising on quality and safety.
Authoritativeness and trustworthiness in the context of welding electrodes are critical. Users must rely on experts with substantial field experience to discern the appropriate electrode for their unique requirements. Through extensive testing and practical application, these electrodes have been evaluated under various conditions to authenticate their performance credibility. Resources such as certification bodies and technical welding guides recommend these electrodes based on proven data, drawing from industry standards that emphasize safety, reliability, and efficacy.
In summary, the E7018, 7016, and 6013 electrodes each fulfill essential roles in the welding industry. By combining experience-driven insights and expert validations, welders can make informed decisions that align with project demands, ensuring optimal performance and adherence to industry standards. It is this blend of expertise and firsthand experience that establishes confidence in choosing the right welding electrodes for every task at hand.