The E-7018 welding rod stands out as a staple in industrial and commercial welding projects due to its remarkable characteristics and versatile applications. Craftsmen and professionals in the welding domain consistently favor this electrode for its unique properties that ensure robust and long-lasting welds. This article delves into the specifics of why the E-7018 is a top choice among welding experts, focusing on its real-world applications, technical nuances, and safety aspects.
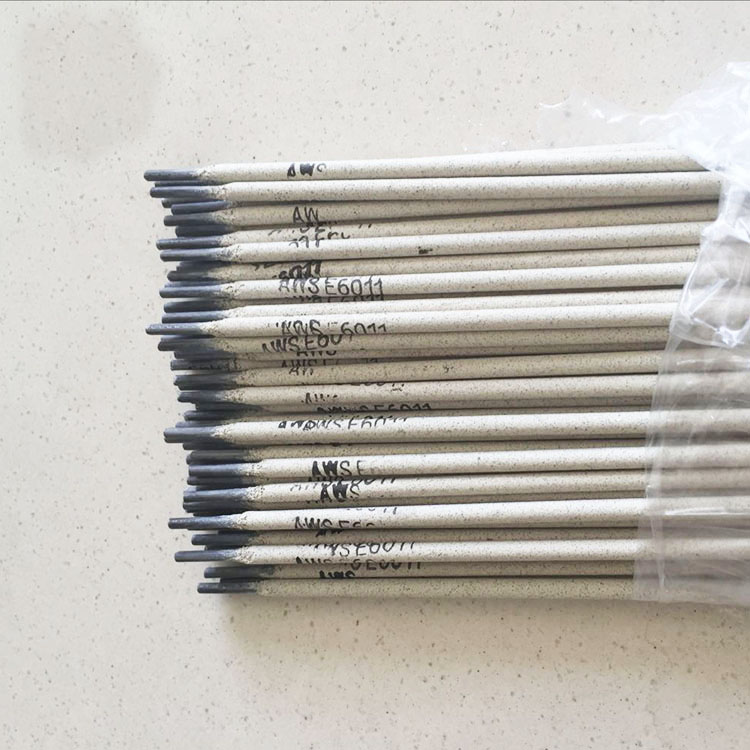
E-7018 electrodes are revered for their low-hydrogen iron powder coating, which significantly reduces the risk of hydrogen-induced cracking—a common issue in the welding of steel. This low hydrogen feature makes E-7018 indispensable for critical welding projects, such as structural steelwork and pressure vessels, where integrity and strength are paramount. Seasoned welders appreciate this rod not just for its technical properties but also for the smooth and clean arc it produces, minimizing post-weld clean-up and reducing project time.
These rods are lauded for their ability to weld in numerous positions flat, horizontal, vertical, and overhead. This adaptability is crucial on-site where work conditions may not always allow for the perfect setup. Experienced welders often highlight the reliability of the E-7018 in less-than-ideal environments, such as outdoor locations subject to unpredictable weather. Here, the rod’s moisture-resistant characteristics play a key role in maintaining weld quality.
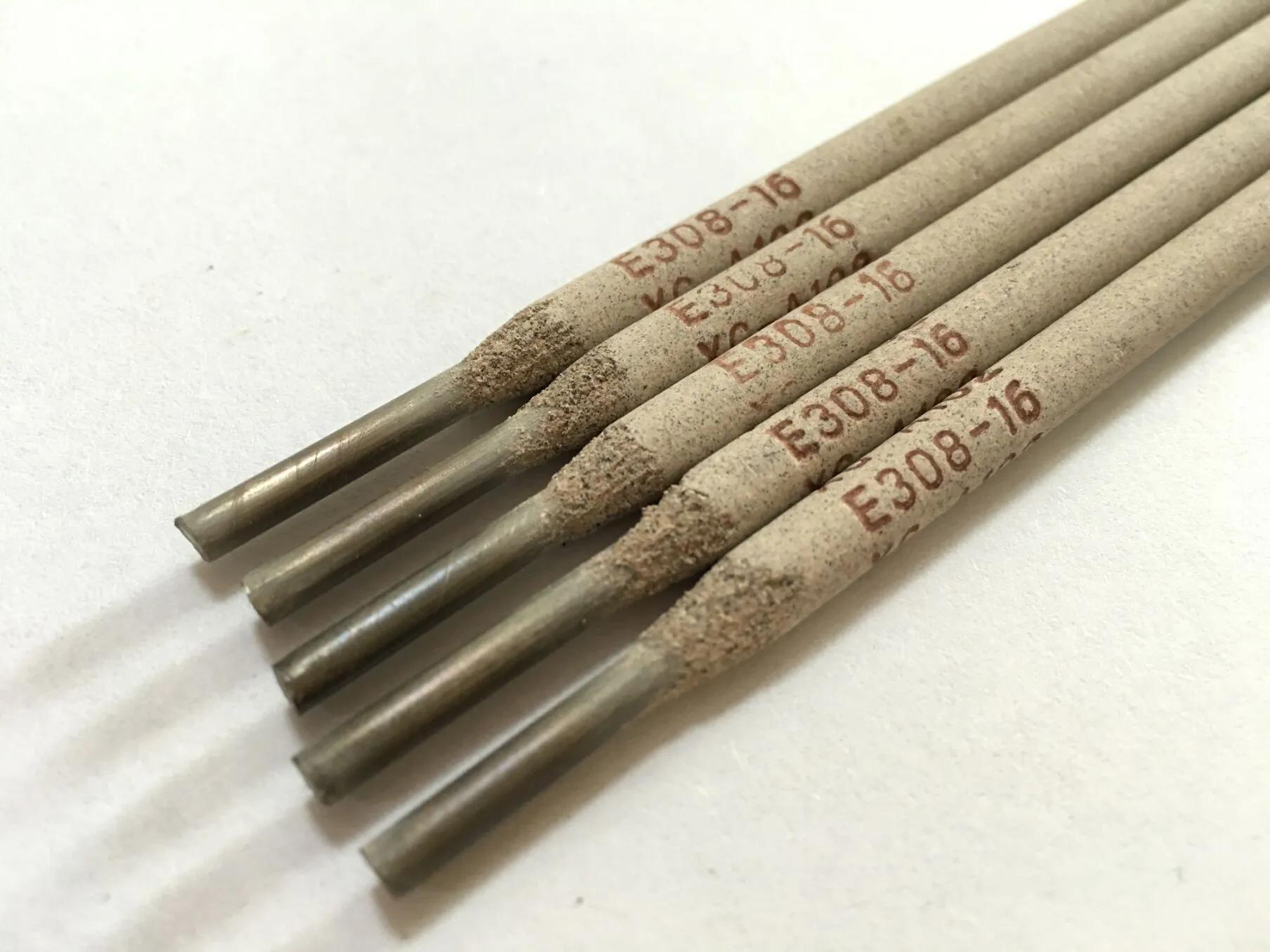
The E-7018 rod’s impressive tensile strength, rated at 70,000 psi, ensures that welds can withstand significant stress without compromise. This characteristic, combined with excellent ductility, makes it a preferred choice in construction applications where safety and durability are non-negotiable. Professionals also note the rod’s deposition rate, which allows for efficient metal transfer and encourages uniform bead formation, critical for achieving aesthetically and structurally clean welds.
welding rod e-7018
In the industry, there is a consensus on the importance of proper storage to maintain the E-7018’s efficiency.
These rods are hydroscopic, meaning they absorb moisture from the environment. Therefore, keeping them in a dry storage oven is recommended to prevent moisture uptake that could lead to weld defects. Expert advice consistently suggests maintaining storage temperatures around 250°F to ensure the rods retain their optimal condition.
Safety considerations are paramount when using any welding materials. Users of E-7018 must be aware of the appropriate safety gear required to protect against the intense light and heat generated during welding. Protective clothing, gloves, and a welding helmet with the correct shade level are essential to prevent exposure to harmful UV rays and molten metal splatter. Professionals underline the importance of maintaining a well-ventilated workspace to avoid inhalation of potentially hazardous fumes, a standard practice that underscores trustworthiness in welding operations.
The application of E-7018 goes beyond just functionality; it extends into improving the efficiency and safety of projects. Skilled welders often mention their experiences where swap-outs from different electrodes to E-7018 led to significant improvements in project timelines and outcomes. These real-life applications bolster the electrode’s reputation, making it a benchmark in the welding industry.
In summary, the E-7018 welding rod is not just a tool but a pivotal component in achieving exemplary results in demanding welding tasks. Its low-hydrogen coating, high tensile strength, versatility in application positions, and structural reliability underscore its authority and consistent trust among welding professionals. Proper handling and adherence to safety protocols further enhance its standing, ensuring that operations proceed smoothly and result in high-quality welds. This rod significantly bridges expertise with experience, making it an indispensable resource for any welding project that demands excellence.