A MIG welder wire is an essential tool for any welding project. Whether you are a professional welder or a DIY enthusiast, having the right wire can make a significant difference in the quality and strength of your welds.
MIG welding, also known as gas metal arc welding, is a popular welding process that uses a continuous solid wire electrode for feeding into the weld pool. This wire electrode is melted and acts as a filler material to join the two pieces of metal together.
One of the key factors to consider when selecting a MIG welder wire is the thickness of the wire. The wire diameter will determine the size of the weld bead and the welding speed. Thicker wire is suitable for welding thicker metals, while thinner wire is better for welding thinner materials.
Another important consideration is the type of metal you will be welding. Different metals require different types of MIG welder wire. For example, mild steel typically uses a standard ER70S-6 wire, while stainless steel requires a different type of wire with higher chromium content.
The shielding gas used in MIG welding also plays a crucial role in the selection of the wire. The most commonly used shielding gas is a mixture of argon and carbon dioxide, which is suitable for welding a wide range of metals The most commonly used shielding gas is a mixture of argon and carbon dioxide, which is suitable for welding a wide range of metals
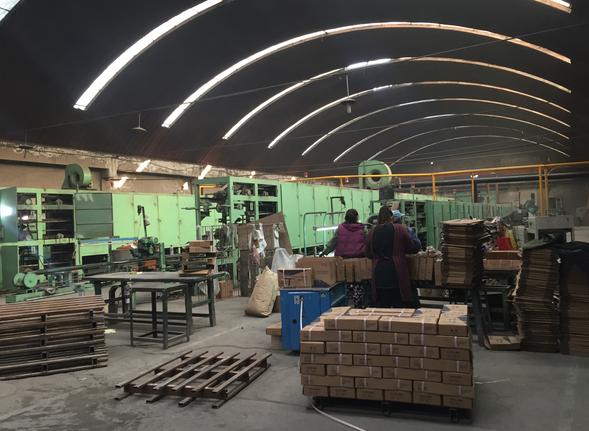
The most commonly used shielding gas is a mixture of argon and carbon dioxide, which is suitable for welding a wide range of metals The most commonly used shielding gas is a mixture of argon and carbon dioxide, which is suitable for welding a wide range of metals
mig welder wire. However, specific types of wire may require different shielding gases for optimal performance.
When choosing a MIG welder wire, it is essential to consider the welding parameters, such as voltage, wire feed speed, and travel speed. These parameters will affect the quality and appearance of the weld, as well as the overall efficiency of the welding process.
In addition to selecting the right wire for your project, it is also crucial to ensure proper storage and handling of the wire. Storing the wire in a dry and clean environment can prevent contamination and ensure consistent welding performance.
Overall, the selection of the right MIG welder wire is crucial for achieving strong and high-quality welds. By considering factors such as wire thickness, metal type, shielding gas, and welding parameters, you can ensure a successful welding project with durable and reliable results.
In conclusion, a MIG welder wire is a fundamental component of the welding process, and choosing the right wire is essential for achieving optimal results. By understanding the different factors that impact wire selection and following best practices for storage and handling, you can ensure a successful welding project with strong and durable welds.