The 3/32 welding rod is an essential tool in the world of metal fabrication, offering precise applications in a variety of welding processes. Its versatility makes it a popular choice among both amateur and professional welders. Understanding its applications, benefits, and proper handling techniques can enhance the quality of welds and ensure safety and efficiency in any project.
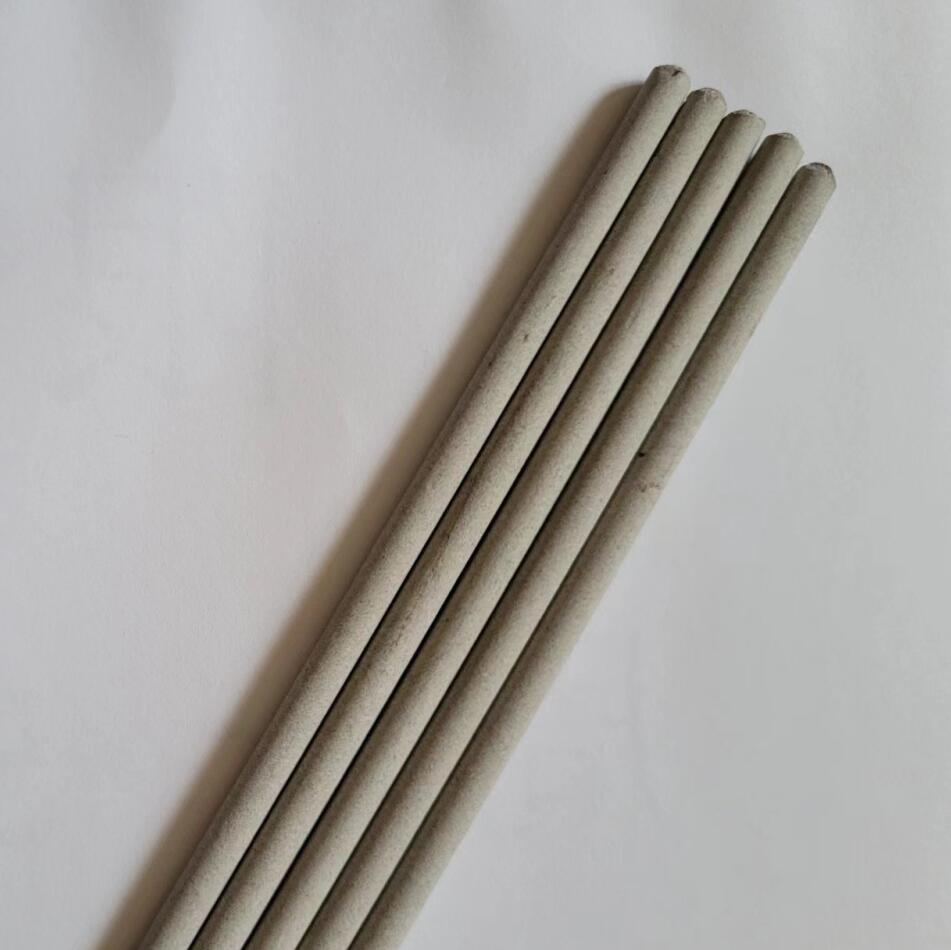
3/32 welding rods are commonly used in Shielded Metal Arc Welding (SMAW), also known as Manual Metal Arc Welding (MMAW) or stick welding. They provide excellent control and allow for smooth, steady arcs, making them suitable for welding carbon steel and other ferrous metals. One of the standout features of these rods is their ability to offer a consistent burn-off rate, which is crucial for maintaining weld quality during extensive welding tasks.
From an expertise perspective, selecting the appropriate welding rod involves assessing the material's composition and thickness. The 3/32 diameter is particularly well-suited for medium-thickness materials, offering a balanced penetration and bead profile. Welders using a 3/32 rod will appreciate its adaptability to various electrical settings, typically operating between 70 to 100 amps, which allows adjustments based on specific project needs.
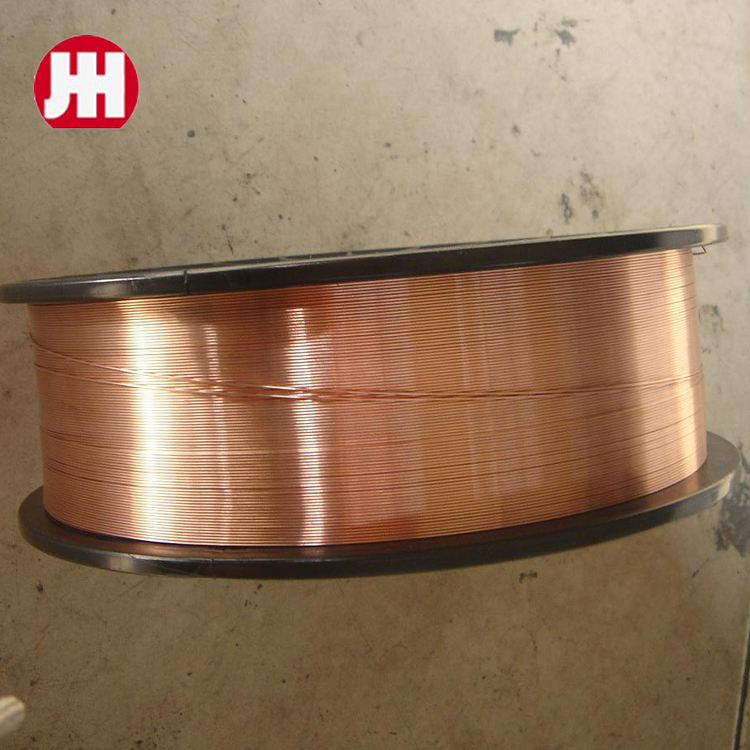
Experience shows that using this rod efficiently requires attention to welding positions, electrode angles, and travel speeds. Welders frequently employ it for all-position welding, though proficiency with vertical and overhead positions might require practice. The rod's coating plays a pivotal role in stabilizing the arc and influencing the characteristics of the weld deposit, highlighting the importance of understanding the coat type for the task at hand.
Professional welders recognize the importance of pre-weld preparation when using 3/32 rods. Cleaning the metal surface to remove rust, oil, and other contaminants ensures a strong and defect-free weld. Additionally, controlling the temperature of the base material prevents warping and maintains structural integrity. Tack welding, a technique where preliminary weld spots temporarily hold components, can help maintain alignment during the welding process.
In terms of authoritativeness, consulting welding standards and guidelines from organizations such as the American Welding Society (AWS) ensures adherence to industry best practices. These bodies provide comprehensive specifications for using specific types of rods, ensuring optimal performance and safety standards.
Trusting such credible sources reinforces the reliability of welding procedures and outcomes.
3/32 welding rod
Safety is paramount in welding, given the hazards involving heat, ultraviolet radiation, and toxic fumes. Using 3/32 welding rods necessitates appropriate personal protective equipment such as gloves, helmets with suitable filter shades, and flame-resistant clothing to mitigate these risks. Ensuring a well-ventilated environment and employing suitable fume extractors also enhances safety and complies with occupational health standards.
The trustworthiness of using 3/32 welding rods can be further bolstered by sourcing materials from reputable manufacturers and suppliers. Quality control processes in production and adherence to international standards like ISO certifications offer guarantees of rod consistency and performance. Engaging with suppliers who provide material certification and customer support reflects a commitment to providing reliable products.
Despite their advantages, the successful application of 3/32 welding rods depends significantly on the operator's skill and experience. As such, training and practice are crucial. Many technical schools and vocational programs offer detailed courses on welding techniques, including the effective use of various rod diameters. Continuous education helps welders stay updated with technological advancements and refine their skills for better outcomes.
Implementing these rods in projects also involves strategic planning, where understanding job requirements, environmental conditions, and expected weld performance inform rod selection and technique adjustments. Welders can benefit from simulation software that predicts weld behavior under different conditions, aiding in pre-planning and reducing rework on site.
In conclusion, the 3/32 welding rod is more than just a tool; it embodies a combination of science, skill, and safety. Its broad use in the industry underscores its utility and effectiveness in producing high-quality welds. By embracing authoritative guidelines, continuous learning, and strategic planning, welders can maximize the potential of this indispensable rod, ensuring both their project's success and personal safety.