Aluminum TIG welding rods are a crucial element in the field of welding, playing an indispensable role for both hobbyists and professional fabricators alike. These rods are specifically designed for Tungsten Inert Gas (TIG) welding, known for its precision, cleanliness, and ability to produce strong, high-quality welds. When discussing aluminum TIG welding rods, it’s vital to consider the various aspects that contribute to their effectiveness and suitability for different projects.
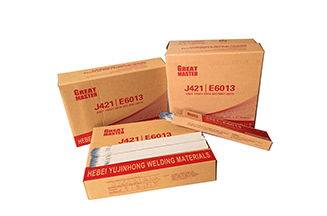
First and foremost, understanding the composition of aluminum TIG welding rods is essential. Typically, these rods are made from pure aluminum or aluminum alloys like 4043 and 5356. The selection between these two depends heavily on the requirements of the project. 4043 rods, for instance, are favored for their enhanced fluidity and ease of use, making them ideal for welding softer alloys. Conversely, 5356 rods are popular for their higher strength and greater corrosion resistance, which makes them suitable for welding tougher aluminum alloys used in marine or heavy-duty applications.
The next consideration is the diameter of the rod. Common diameters range from 1/16 inch to 1/8 inch. The choice of diameter is crucial as it affects the weld’s penetration and the ease of feeding the rod during the welding process. A smaller diameter rod is preferred for thin materials and more intricate work, as it allows for better control. On the other hand, larger diameter rods are used for thicker materials to ensure adequate weld penetration and strength.
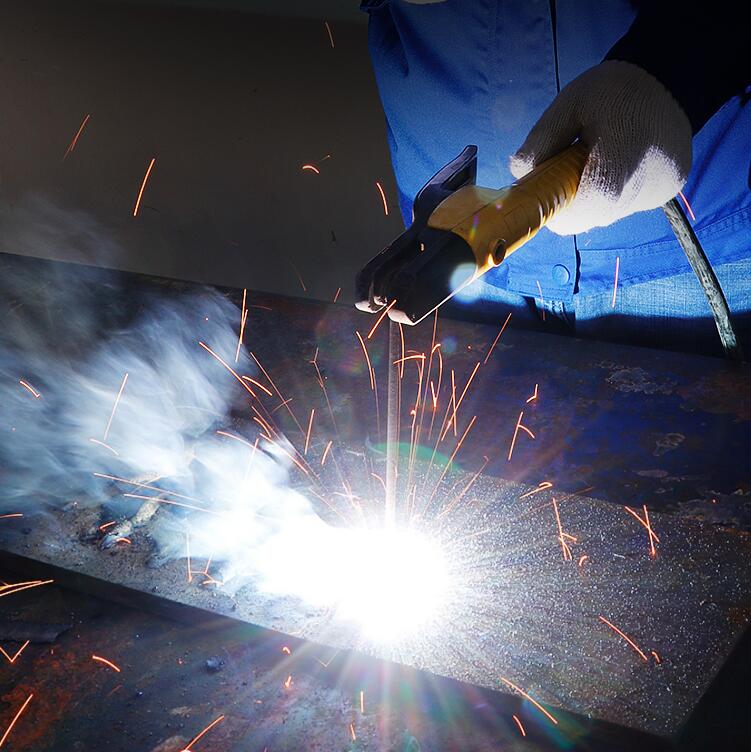
Pre-cleaning the aluminum surface prior to welding cannot be overstated. Aluminum’s intrinsic quality to develop a thin oxide layer on its surface poses a significant challenge during the welding process. This oxide layer has a higher melting point than the aluminum itself, which can lead to incomplete fusion and weak welds. Therefore, cleaning the material with a dedicated aluminum cleaner or mechanically with a stainless steel brush is highly recommended. This step not only enhances the quality of the weld but also prolongs the life of the tungsten electrode by preventing contamination.
aluminum tig welding rod
When it comes to the equipment setup, the right choice of tungsten electrode is key. Pure tungsten or zirconiated tungsten electrodes are commonly employed due to their capability to handle the high heat demands of welding aluminum. These materials provide a stable arc and withstand the thermal conductivity of aluminum, maintaining the integrity of the welding process. Additionally, using an alternating current (AC) power source promotes a cleaning action that helps break up the oxide layer, ensuring a clean and solid weld.
Attention to welding parameters is another cornerstone of effective aluminum TIG welding. The balance of current, travel speed, and filler rod addition needs to be meticulously adjusted. Too much current can cause burn-through, whereas too little may result in poor penetration and weak joints. A consistent travel speed ensures uniform weld bead and reduces the risk of overheating. Meanwhile, the filler rod must be dipped precisely and rhythmically to fill the weld pool without creating voids or inclusions.
The aluminum TIG welding rod’s reliability hinges on the welder’s skill and knowledge. Working with aluminum requires a sharper learning curve due to its heat sensitivity and rapid oxide formation. Thus, gaining hands-on experience, practicing extensively, and continuously updating oneself with the latest techniques are crucial for mastering this welding art. Collaborating with seasoned experts or engaging in welding communities can provide valuable insights and practical tips that textbooks or manuals might not offer.
In conclusion, the aluminum TIG welding rod is more than just a consumable material; it is a pivotal tool that demands understanding and respect for its properties and applications. Mastery of its use can elevate the quality and durability of aluminum structures, reflecting a level of craftsmanship and professionalism that’s acknowledged and trusted within the welding community.