Choosing the right welding wire is pivotal for ensuring high-quality welds, particularly when dealing with CO2 MIG welding. Insiders in the welding industry are well-aware of the nuances and challenges that this type of welding presents, especially when propelled by the distinctive environment created by carbon dioxide as a shielding gas. When selecting a CO2 MIG wire, like those utilized in professional welding settings, several key factors should be meticulously considered to optimize performance, quality, and efficiency.
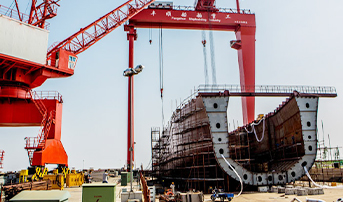
To begin with, one must understand the nature of CO2 gas in MIG welding. Carbon dioxide is a reactive gas that delivers deep penetration and swift welding processes, pivotal for thick material applications. However, CO2 can make the arc less stable than inert gases like argon, necessitating specific wire attributes to mitigate potential issues such as spatter and arc instability.
Mig wires specifically designed for CO2 environments are typically composed with a higher silicon—a deoxidizer—and manganese content to enhance weld pool fluidity and minimize the adverse impacts of reactive gases. For expert welders, the importance of using an ER70S-6 wire, for instance, cannot be overstated in these scenarios. This wire grade is engineered to deliver excellent results with carbon dioxide shielding by providing a stable arc and reducing spatter, ultimately resulting in lower cleanup time and a smoother welding finish.
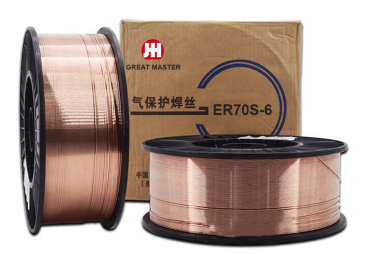
Furthermore, the diameter of the wire is another critical consideration. Welders must gauge the thickness and nature of the base metal to determine the optimal wire size. Larger wire diameters are suitable for thicker metals and allow for higher current settings, while smaller diameters work well for thin materials to avoid burn-through. Expert welders often advise a diameter range of 0.030 to 0.
045 inches for most CO2 MIG welding tasks.
co2 mig wire
An additional aspect to consider is the welding position. CO2 MIG wire must be chosen based on the specific stance—be it flat, vertical, overhead, or horizontal—as this can drastically influence both the technique and wire feed speed. Manufacturers often provide detailed specifications for each wire class, guiding expert users to select the most appropriate wire for their application.
Moreover, trustworthiness in selecting CO2 MIG wires is paramount. You must source from reputable brands known for consistent quality and rigorous testing. Industry standards and certifications, such as AWS (American Welding Society) classifications, should be non-negotiable elements when making your decision. High-quality MIG wires from respected suppliers facilitate not only improved welding outcomes but also maintain safety and efficiency.
Real-world experience reveals that welders who carefully select their CO2 MIG wire based on these professional criteria routinely achieve superior weld quality while mitigating common welding problems. Through the combination of technical expertise, stringent selection criteria, and reliance on authoritative industry standards, one can ensure a reliable welding process. These factors lend authoritative credibility and trust to any welding operation, ensuring that professional standards are met every time.