For anyone exploring the world of welding, understanding the intricacies of different filler materials can greatly enhance the quality of your work. One such material, the MIG flux core wire, stands out due to its versatility and capability of producing strong welds without requiring a shielding gas. This characteristic makes it an ideal choice for both professional welders and hobbyists who want flexibility in their projects.
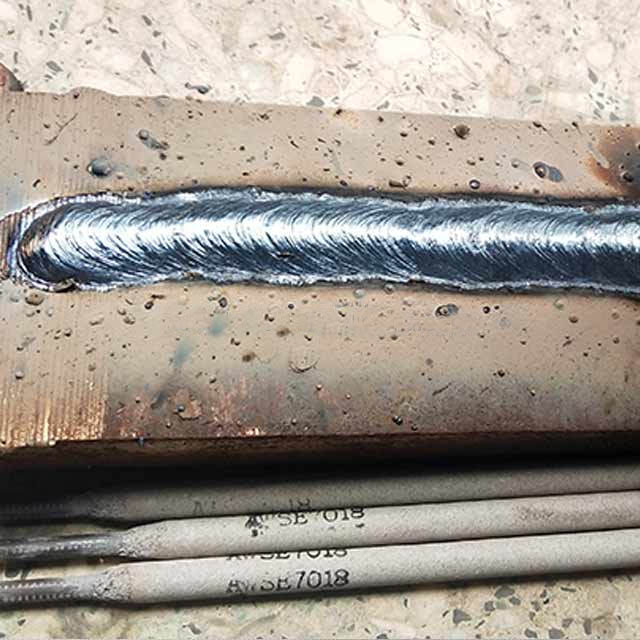
MIG flux core wire essentially combines the benefits of MIG and flux-cored welding techniques. Unlike traditional MIG welding that requires a separate shielding gas to protect the weld pool, a flux core wire contains its own shielding medium within the wire. This allows for welding in outdoor or drafty conditions where wind might blow away the gas from a conventional MIG setup, an advantage particularly useful for site welding or even small home projects conducted in less controlled environments.
Experts in the field often emphasize the efficiency of MIG flux core wire, especially when dealing with heavy or thick materials. Its capability to handle more significant metals compared to solid wire makes it preferred for industries demanding robust performance, such as shipbuilding or structural work. From a professional standpoint, the flux core wire’s deeper penetration on thicker sections is invaluable, saving both time and resources while ensuring strong, durable welds.
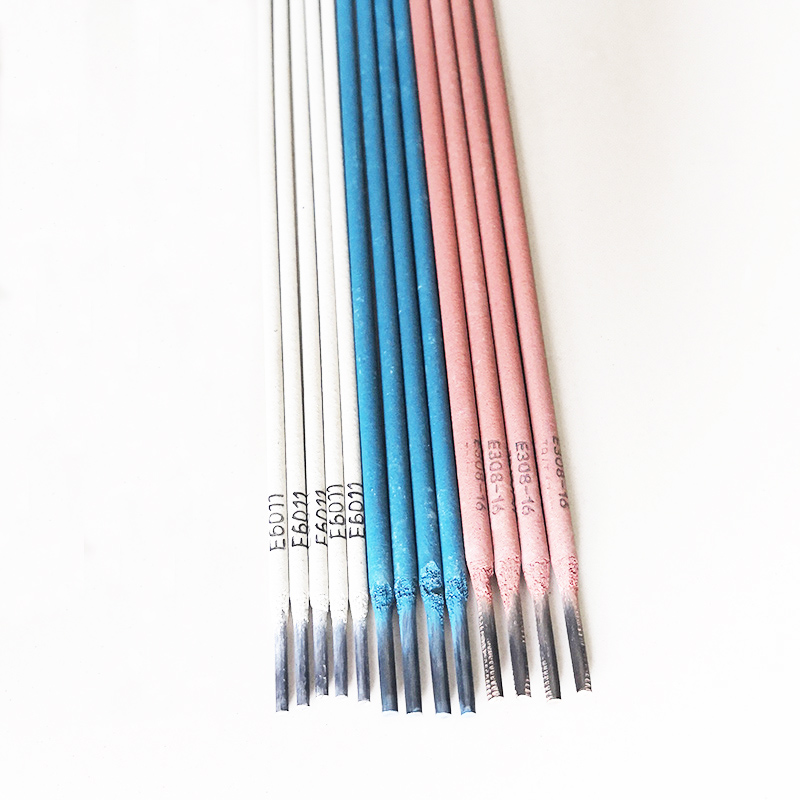
Regarding personal experience, many welders will attest to the ease of transitioning from solid wire to flux core within a single machine—a feature particularly beneficial for versatile workshops. It suits various positions, including overhead and vertical, offering flexibility that many experts find lacking in other methods. The absence of a separate shielding gas also reduces the complexity and cost of equipment setup, aligning with the practical experiences of welders who prioritize efficiency and ease of access.
mig flux core wire
To achieve authoritativeness, it’s crucial to highlight that reputable manufacturers provide flux core wires in different compositions and diameters to suit a wide range of applications. Industrial experts advise selecting wire based on the material to be welded, the welding position, and the structural requirements. Quality products from leading brands serve as a testament to reliability, meeting industry standards and guaranteeing product safety and performance. Certifications that accompany these wires further boost their trustworthiness, ensuring users receive verified quality.
Trustworthiness in the realm of welding materials hinges significantly upon adherence to safety and operational guidelines. User manuals and expert advice insist on using appropriate personal protective equipment (PPE), such as gloves, masks, and welding jackets, to safeguard against fumes and UV radiation. This emphasis on safety cultivates an environment of mutual trust between manufacturers and consumers.
In terms of SEO benefits, tapping into users' search intent relating to practical guides, tips, or benefits of using MIG flux core wires can boost site performance. Content optimized around keywords like “flux core welding tips,” “best flux core wire for beginners,” or “advantages of flux core welding” resonates well with readers seeking specific, actionable information. Providing comprehensive, expert-driven advice in such articles solidifies site authority and reliability in the vast landscape of welding resources online.
In conclusion, the MIG flux core wire is a revolutionary tool that offers unparalleled convenience, adaptability, and efficiency. Its self-shielding nature, high penetration capabilities, and ease of use make it a beloved choice among both seasoned professionals and aspiring welders. Ensuring its optimal use through expert-recommended practices and choosing high-quality, certified products will pave the way for superior weld quality and project success.