In the world of welding, particularly Metal Inert Gas (MIG) welding, the wire used is a crucial component impacting the quality of the weld. MIG welding wire is not just a consumable; it’s a determinant of the strength, efficiency, and precision of the welding process. Understanding its nuances can significantly enhance your welding projects and ensure high productivity and safety standards.
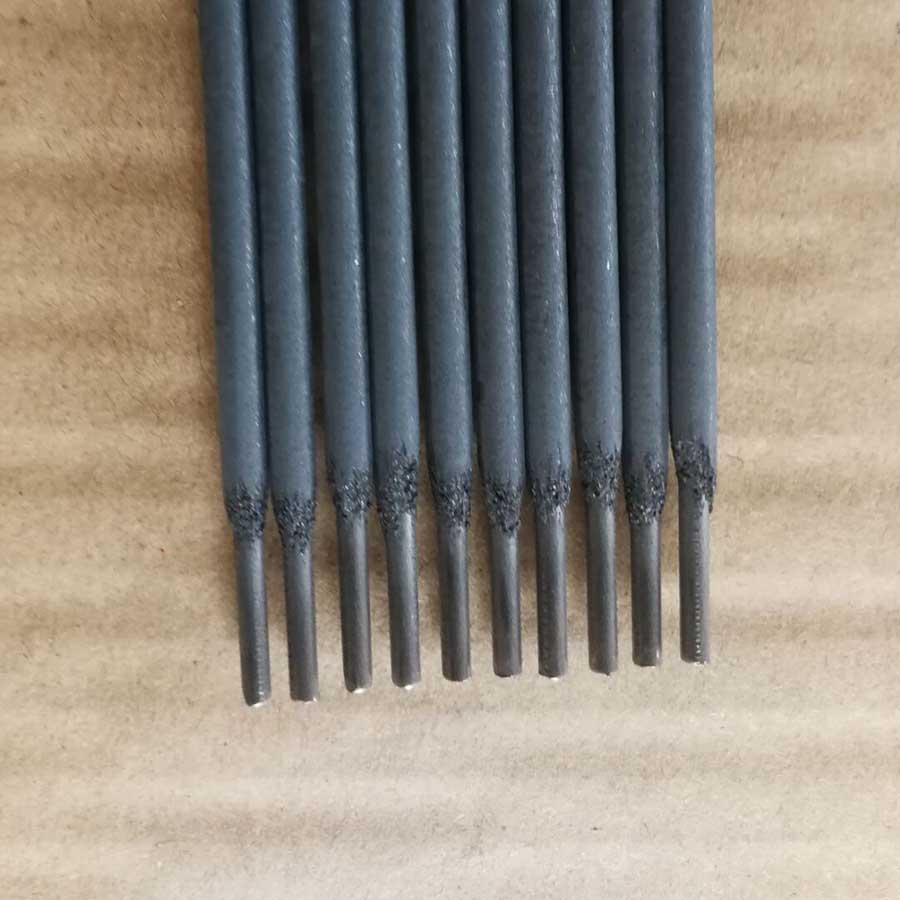
The Importance of Choosing the Right MIG Welding Wire
Choosing the right MIG welding wire is crucial as it directly influences the weld's mechanical properties, such as tensile strength and corrosion resistance. An experienced welder knows that the correct wire size and material can drastically improve the welding process's quality and efficiency. High-quality wire ensures smooth wire feeding, reducing downtime and minimizing spline or porosity, which might occur with substandard products.
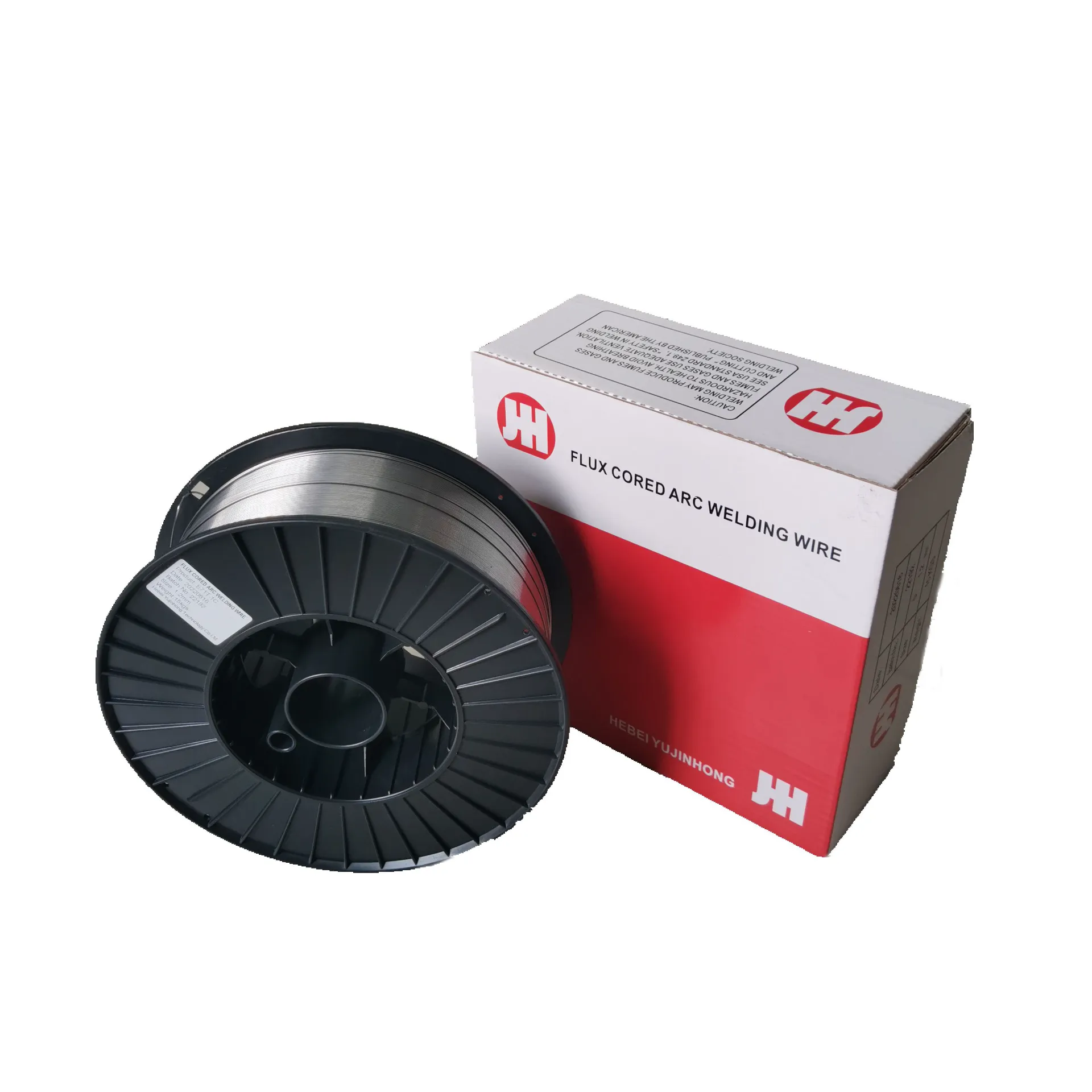
Material Composition and Its Effects
MIG welding wires come in various compositions, primarily aluminum, stainless steel, and mild steel. Your choice depends on the base material you are working with
- Aluminum Wires Known for their thermal conductivity and corrosion resistance, these wires are ideal for high-heat applications. They require a specialized feeding system due to their softness.
- Stainless Steel Wires These provide excellent corrosion resistance and are perfect for welding across a variety of environments.
They help maintain the weld's integrity over time despite chemical exposure.
- Mild Steel Wires Offering a balance of strength and flexibility, mild steel wires are versatile for general-purpose welding. They are usually coated with copper to prevent oxidation and improve electrical conductivity.
Diameter Matters
mig welding wire
The diameter of the MIG wire impacts the penetration and deposition rate. Smaller diameters are excellent for thin materials as they offer precise control and reduce heat input, preventing warp. Larger diameters are beneficial for thick materials, providing deeper penetration and faster welding speeds.
Autonomy and Feedability
Quality welding wires are engineered for seamless feedability. This ensures that the wire moves smoothly through the feeder and torch without disturbances. Poor feedability can lead to inconsistent welds, increased spatter, or even equipment malfunction. Efficient wires guarantee a stable arc and reduce the need for continuous supervision during the weld process, thus improving overall productivity.
Manufacturer Expertise and Certifications
Choosing a manufacturer with a reputation for consistency and quality assurance is crucial. Expert manufacturers offer certifiable wire grades meeting industry standards. Certifications like ISO 9001 ensure that the wire production follows strict quality management protocols, guaranteeing reliable and repeatable results across various projects.
Conclusion
Welding, both as a craft and a science, benefits significantly from the meticulous selection of its components, with MIG welding wire playing a pivotal role. An informed choice leads to enhanced weld quality, sustainability, and fine workmanship. With proper expertise, the right material, diameter selection, and an authoritative manufacturer, you can trust that your welding projects will meet both current and future standards in integrity and performance. Always strive for knowledge and precision, as these are the hallmarks of not only good craftsmanship but also of sustainable engineering practices.