Electrodes welding, though a fundamental aspect of various industrial and DIY projects, often remains a topic shrouded in mystery for many. Understanding its nuances can transform a casual user into a seasoned professional capable of creating robust and reliable welds. With decades of industry experience under my belt, I am here to unravel the complexities of electrodes welding. This article will guide you through the intricacies and elevate your proficiency, whether for commercial applications or personal endeavors.
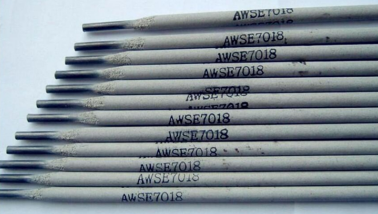
Electrode selection is the cornerstone of effective welding. The choice depends on the metal type and thickness, welding position, and power source available. Mild steel projects typically benefit from using E6010 and E6011 electrodes, known for deep penetration and versatility in various positions. In contrast, E7018 electrodes are preferred when working on structural welding projects requiring high tensile strength and ductility. Their low hydrogen properties minimize the risk of cracking, especially in stressed steels. Understanding these subtleties allows you to match the electrode to your specific needs, ensuring strong and durable welds.
The role of the electrode coating in flux composition cannot be overstated. It influences arc stability, controls weld pool, introduces protective gases, and stabilizes the welding arc. For instance, cellulose-based coatings on electrodes create a gas shield, protecting the weld pool from atmospheric gases, which is crucial for outdoor welding applications. Mastering these elemental interactions is essential for achieving optimal results in varying environmental conditions.
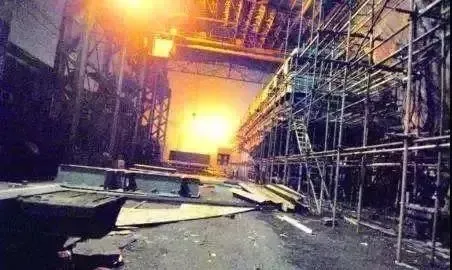
Welding position profoundly affects technique and outcome. Whether working in flat, horizontal, vertical, or overhead positions, each presents unique challenges requiring particular skills and electrode choices. Flat positions generally provide more control over the molten pool leading to cleaner welds, while vertical up or down and overhead positions necessitate a steady hand and often different electrode types to maintain stability and prevent slag inclusions. Building experience in these positions broadens your expertise, making you more versatile in tackling diverse projects.
electrodes welding
The welding machine's settings and maintenance are pivotal in achieving consistent welding quality. Machines should be calibrated correctly with amperage settings tailored to the electrode and material thickness. A higher amperage setting can improve penetration but might lead to excessive spatter or burn-through if not meticulously controlled. Regular maintenance checks, including cleaning and replacing worn-out components, guarantee reliability and prevent unexpected failures during critical projects.
Safety precautions should always be prioritized. Welding electrodes emit intense heat and potentially harmful fumes. Ensuring the use of appropriate personal protective equipment such as welding helmets, gloves, and aprons is non-negotiable. Additionally, working in well-ventilated areas or utilizing fume extraction systems can significantly reduce health risks, enhancing long-term well-being and productivity.
Finally, sustainability in welding practices is becoming increasingly crucial. Opting for environmentally friendly electrodes, recycling metal scraps, and using energy-efficient welding machines contribute to a minimal ecological footprint. As industries shift towards sustainable practices, your commitment to reducing environmental impact not only aligns with industry trends but also positions you as a responsible and forward-thinking welder.
Electrodes welding embodies both art and science, requiring theoretical knowledge and practical experience. By continuously updating your skills and embracing new technologies and methodologies, you ensure that you remain at the forefront of this ever-evolving field. Mastery over these multi-faceted processes not only boosts your confidence but also solidifies your reputation as an authoritative and trustworthy figure within the welding community.