Selecting the right welding wire is instrumental for any metal joining process, and ER70S-6 welding wire stands out as an invaluable asset for both novice and expert welders. Crafted with precise engineering, this wire is designed to optimize performance under demanding conditions, ensuring durability and robustness in various applications.
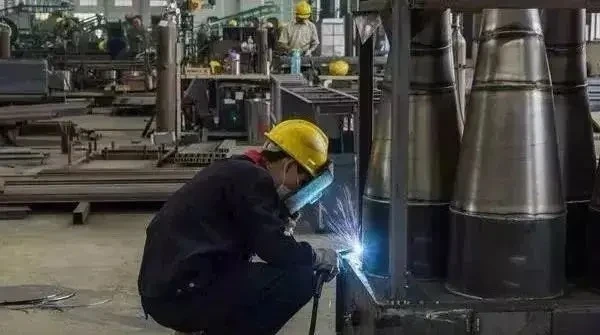
ER70S-6 welding wire is especially known for its impressive deoxidizers, such as silicon and manganese, which not only make the welding process smoother but also enhance the mechanical properties of the weld. This wire is consistently reliable, presenting fewer issues with porosity and uneven surfaces, making it the preferred choice for tasks that demand aesthetic precision as well as structural integrity.
One of the greatest advantages of ER70S-6 is its versatility across different types of welding. It performs exceptionally well in both MIG (Metal Inert Gas) and MAG (Metal Active Gas) applications. This flexibility ensures that welders can work across a variety of metals and thickness levels, from thin sheets to thick plates, without significant adjustments to their setup, thereby saving time and resources.
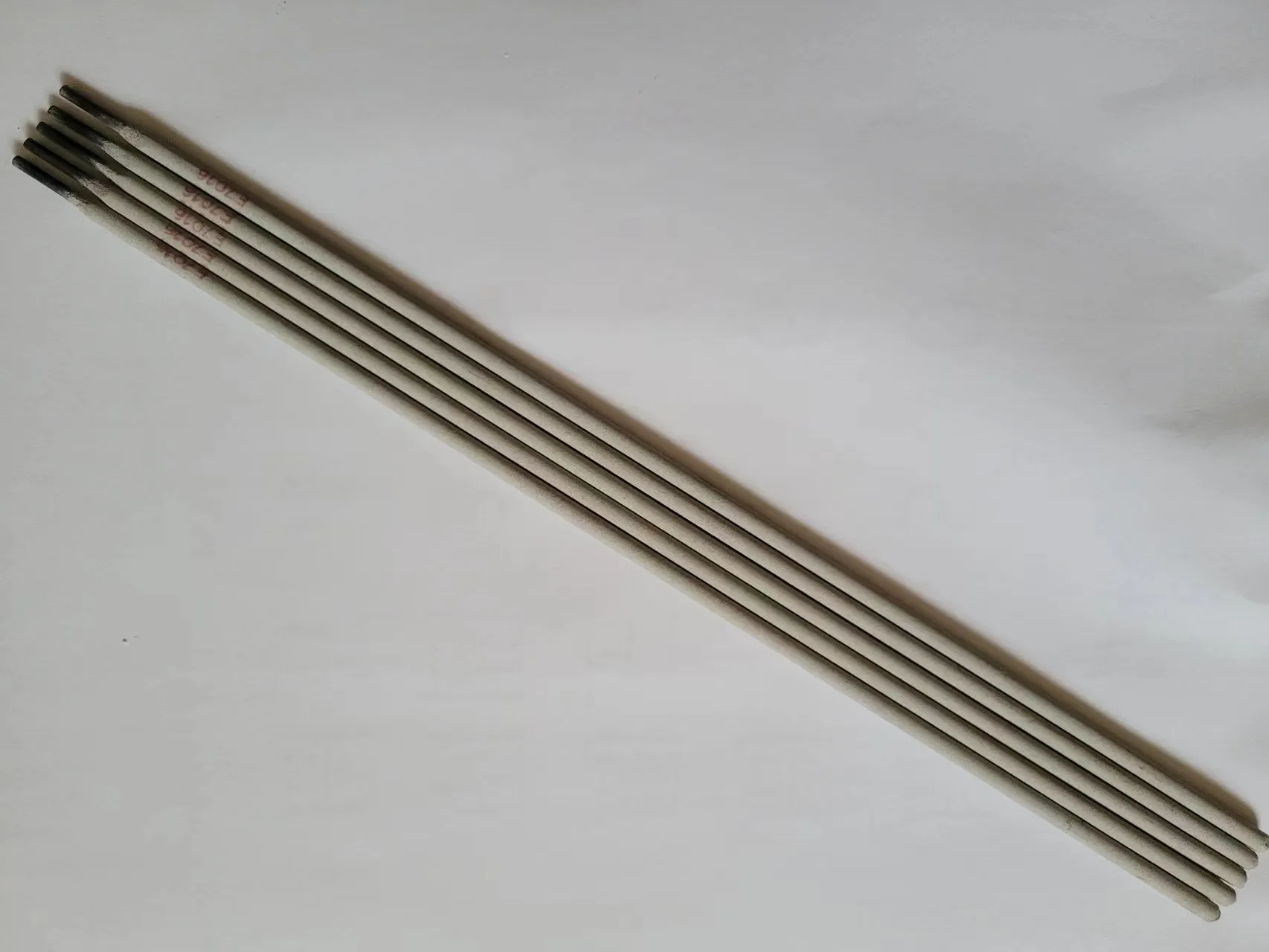
Moreover, ER70S-6 excels in both automatic and semi-automatic welding processes, allowing for customization and adaptability, which is particularly valuable in industrial settings where precision and efficiency are paramount. The wire's consistent feeding property minimizes downtime caused by wire jamming or uneven flow, contributing to smoother operations and decreased operational costs.
Another factor bolstering the popularity of ER70S-6 welding wire is its ability to handle rusted or dirty surfaces better than many other wires. This characteristic proves invaluable in environments where full surface cleaning isn't feasible, providing reliable performance without compromising the quality of the weld. As such, industries ranging from automotive to construction often turn to ER70S-6 for jobs that require high productivity and quality standards even under suboptimal conditions.
er 70 s 6 welding wire
Professionals underscore the importance of proper wire selection, emphasizing how ER70S-6 welding wire’s chemistry contributes to lower hydrogen levels in the weld. This attribute is essential in preventing cracking and ensuring the longevity of the welds. Welders benefit from its strong tensile strength (around 70,000 psi), making it ideal for structural welding and other applications demanding high strength and resiliency.
To ensure the successful application of ER70S-6, experts recommend a controlled environment, including the correct shielding gas and voltage settings, to maximize the wire’s potential. Utilizing argon-rich gas mixtures can further enhance the weld appearance and quality. Guidance from seasoned welders suggests maintaining proper wire-stick-out and travel speeds to optimize bead formation, reducing the risk of defects.
Given its remarkable adaptability and strength characteristics, ER70S-6 welding wire has earned its authoritative status among welding professionals globally. Its engineering precision, combined with a profound understanding of metallurgy, empowers it to meet the challenges of diverse welding scenarios, reinforcing its position as a trustworthy option for high-quality, reliable welds.
The commitment to quality and performance reflected in ER70S-6 welding wire establishes it as a compelling choice for industry leaders and individual practitioners seeking efficient and robust solutions in welding technology. Its excellence in both versatility and function underscores its rightful place in the toolkit of any welding operation aiming for excellence and efficiency.