When it comes to selecting the best flux core welding wire, experience stands as one of the most critical factors to consider. Over the years, seasoned welders and industry professionals have determined that finding the right flux core welding wire is essential for achieving high-quality welds with efficiency and precision. This article aims to delve into the intricacies of what makes a flux core welding wire superior and how its characteristics can profoundly impact your welding outcomes.
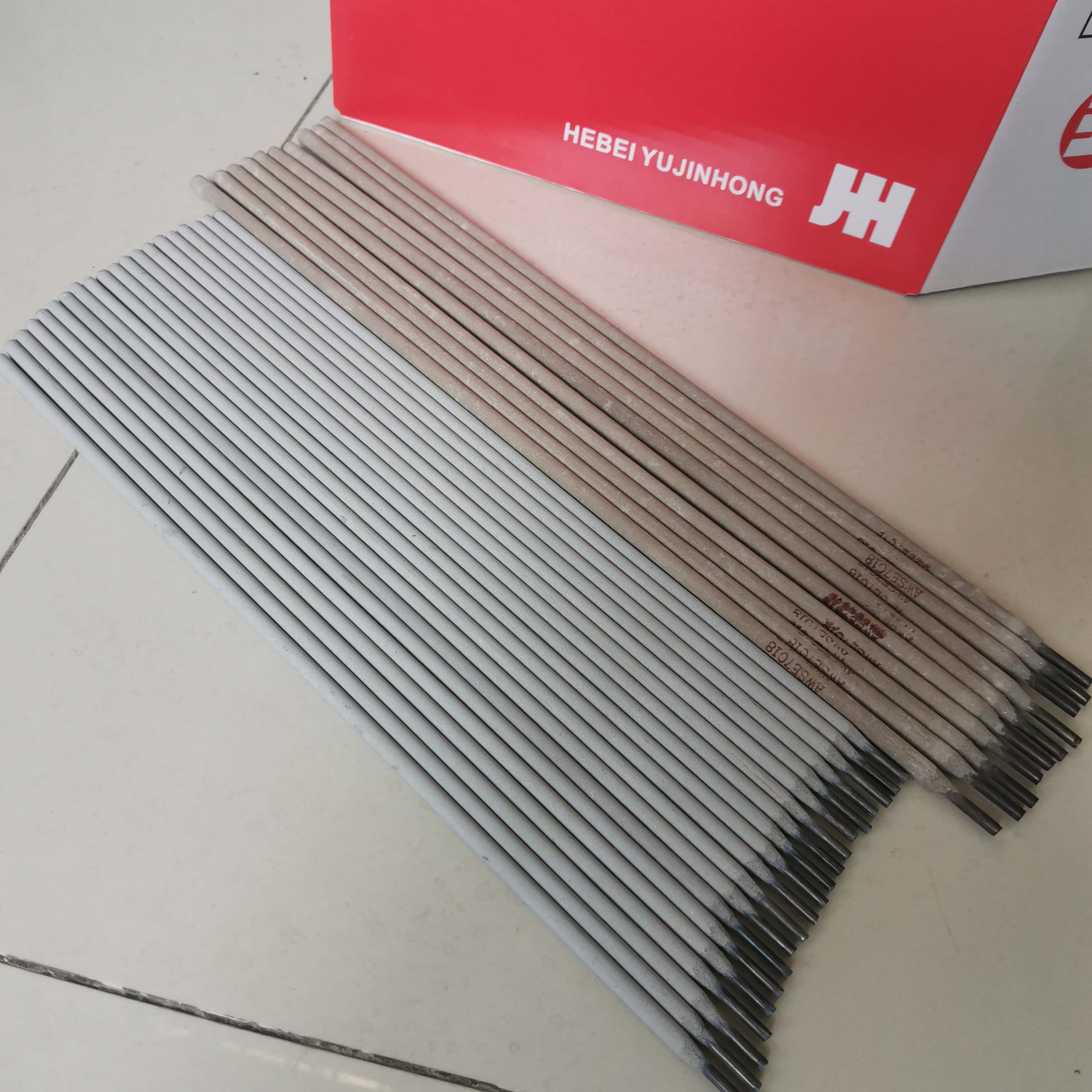
First and foremost, it is imperative to recognize the influence of material compatibility in selecting your flux core welding wire. Mild steel, stainless steel, and other metal types each require specific wire compositions to enhance weld strength and quality. Professional welders often swear by self-shielding flux core wires for mild steel, especially in outdoor settings where wind and atmospheric conditions can affect shielding gases' effectiveness if used with MIG welding setups.
To avoid compromising the structural integrity of your work, consider premium brands recognized for their consistent quality outputs. Companies like Hobart and Lincoln Electric are frequently lauded for their dedication to quality assurance and material science innovation. These manufacturers invest heavily in research and development, typically reflected in user trust and authoritative reviews.
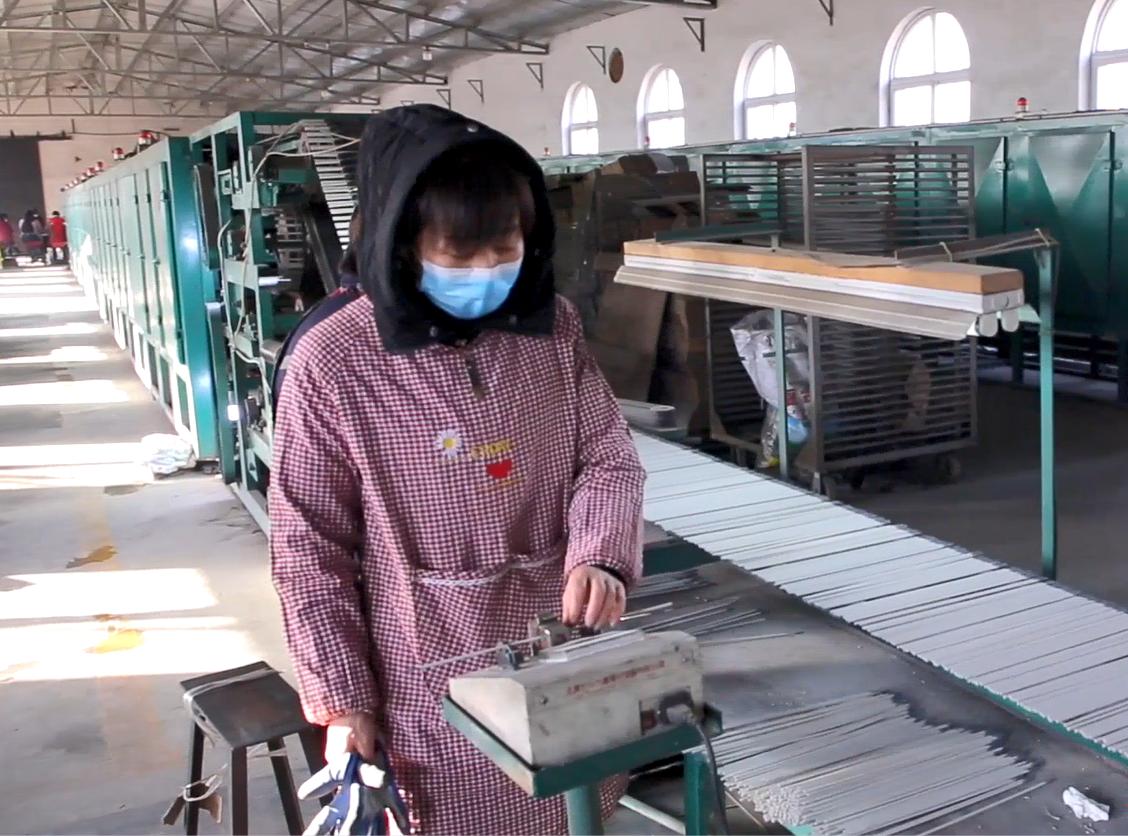
The diameter of the flux core welding wire is another fundamental aspect influencing welding performance. For thicker, more robust projects, welders should opt for a larger wire diameter, such as .035 inches, to ensure deeper penetration and stronger welds. On the other hand, thinner materials benefit from smaller diameter wires, around .030 inches,
offering more control and precision. Consulting the manufacturer's recommendations is paramount for determining the optimal diameter for particular welding projects.
Expertise in flux core welding also involves an understanding of the importance of wire feeding capabilities and compatibility with your welding machine. It's crucial to ensure your welder supports flux core wire feeding to prevent issues such as wire jamming or inconsistent feeding that could lead to substandard welds. Advanced machines often feature variable feed settings, allowing seasoned welders to finetune their setups for improved control and efficiency.
best flux core welding wire
Weld position often dictates the type of flux core wire suitable for the job. Out-of-position welding, which includes vertical and overhead positions, generally requires wires with fast-freezing slag systems. Wires that form a tight arc and produce minimal spatter are preferred, offering cleaner welds and reducing the need for extensive post-weld cleanup.
Authoritative reviews often emphasize the importance of flux core wire's ease of use, particularly for beginners or those transitioning to flux core welding from other methods. User-friendly wires associated with smooth arc starts, consistent feeding, and minimal spattering can drastically reduce the learning curve for novices while maintaining professional-grade results.
Trust in the welding wire's efficacy is further reinforced by examining certifications and adherence to industry standards. Wires boasting AWS (American Welding Society) or ISO (International Standards Organization) certifications indicate compliance with rigorous quality and performance benchmarks, offering assurance of reliability regardless of application scale.
Moreover, field testing and real-world feedback add layers of trustworthiness to flux core welding wire selections. Observing how wires perform in diverse settings—from the predictability of workshop environments to the unpredictability of field conditions—provides invaluable insights into potential strengths and limitations.
In conclusion, the pursuit of the best flux core welding wire encompasses a blend of experience, expertise, authoritative insights, and trust-based evaluations. Integrating these elements ensures that your choice not only meets but exceeds operational expectations, laying the groundwork for welds that are both aesthetically pleasing and structurally sound. Whether you’re a seasoned professional or a budding welder, understanding and leveraging these comprehensive guidelines are pivotal steps toward achieving welding excellence.