TIG welding, or Tungsten Inert Gas welding, is an arc welding process that uses a non-consumable tungsten electrode to produce the weld. This precise welding technique is popular among professionals working with thin-gauge metal and non-ferrous metals. Central to the success of TIG welding is the type of welding wire used. Selecting the right TIG welding wire can be vital for achieving high-quality welds, and understanding its nuances is essential for both seasoned welders and those looking to refine their craft.
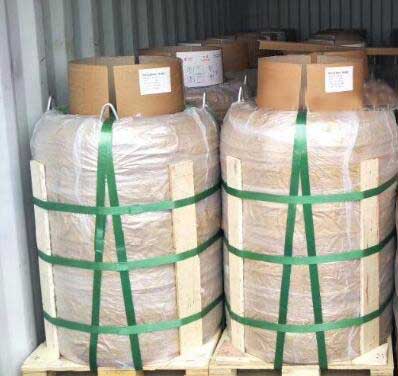
Choosing the right TIG welding wire begins with understanding the material composition of the metals being welded. For aluminum welding, for instance, ER4043 and ER5356 are common wire choices. ER4043 offers a lower melting point and better fluidity, which is ideal for aesthetic welds or welds requiring a fine appearance. ER5356, on the other hand, is preferred for its strength and offers better corrosion resistance, making it ideal for projects that endure significant wear or those to be anodized after welding.
Stainless steel TIG welding also demands careful consideration of wire type, based on the specific needs of the project. A widely utilized wire in this domain is the ER308, which joins 304 stainless to 304 stainless–precisely matching the composition for enhanced strength. ER316 is another variant, used where the welded joint faces higher saline or brackish conditions, due to its increased molybdenum content that fortifies against corrosion.
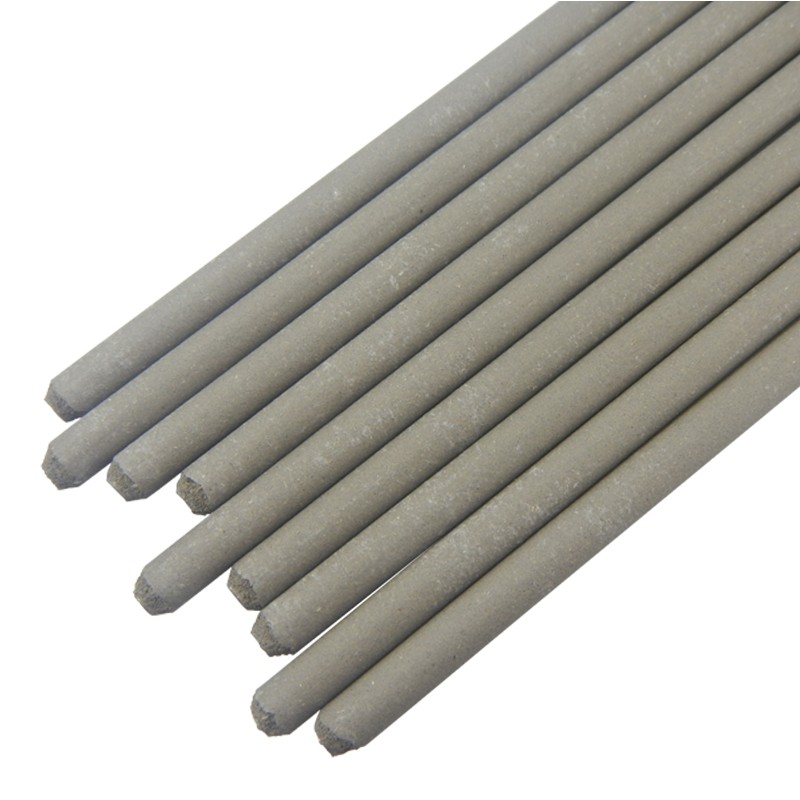
Expert TIG welders understand that the diameter of the wire affects the performance of the weld. Thinner wires, such as those in the range of 0.8mm to 1.0mm, are suited for lighter gauge projects, where controlling the heat input is critical to avoid warping or burn-through.
Thicker wires, like 1.6mm, are more appropriate for heavy-duty applications, where higher current and deeper penetration are required. In applications requiring high precision, ensuring the correct wire diameter is crucial for controlling the weld bead and ensuring the integrity of the entire structure.
tig welding wire
The surface finish of TIG welding wire plays a significant role in ensuring weld quality. Clean, oxide-free surfaces lead to more consistent electrical conductance and arc stability, thus adding to the weld’s aesthetic and structural quality. Therefore, it is recommended to choose wires that are well-cleaned and polished, minimizing impurities that could hinder weld quality.
Storage and handling of TIG welding wires are equally vital to maintaining their quality. Wire should always be stored in a dry, cool environment to prevent corrosion or any damage that could result from moisture infiltration. Professional welders often recommend storing wires in resealable containers or moisture-resistant packaging to prolong their usability. This ensures that when you reach for the wire, it's as good as new, ready to achieve that perfect weld without any defects caused by improper storage.
The quality of TIG welding wire can significantly impact the efficiency and outcome of a welding project. Engaging with reputable suppliers ensures access to wires manufactured with precise alloy compositions and excellent quality control. Expert welders value certifications and standards compliance, such as those provided by AWS (American Welding Society), guaranteeing that the wire meets stringent quality checks and industry requirements.
When it comes to TIG welding, the importance of selecting the correct wire cannot be overstated. The right choice enhances the welder’s ability to deliver high-caliber work, standing up to both aesthetic scrutiny and functional demands. Continuous learning and adaptation in technique, alongside a commitment to choosing quality materials, underpin the expertise and authority of proficient TIG welders worldwide. Understanding these components helps build trust and credibility, both in the craft itself and in the professionals who wield it.