Innovation in Mig Welding Wire 1.0 Factory Production
In the realm of manufacturing and industrial processes, MIG (Metal Inert Gas) welding has become a cornerstone for its efficiency and adaptability. A critical component of this process is the MIG welding wire, particularly the 1.0 diameter variant, which is extensively used across factories for its precise weld deposits and high speed. The production of MIG welding wire 1.0 in factories involves a blend of technology, expertise, and quality assurance to cater to the demanding needs of various industries.
The journey of MIG welding wire 1.0 begins with the selection of high-quality raw materials. These are typically stainless steel or others, depending on the end-use requirements. The raw materials undergo a rigorous cleaning process to ensure that the final product is free from impurities, which could compromise weld integrity. Following cleaning, the material is drawn through a series of dies to achieve the desired diameter. This step requires precision engineering to maintain consistency in wire dimensions, ensuring each weld delivers the same quality every time.
Once the drawing process is complete, the wire is spooled onto reels of specified sizes, ready for the final stage of production – the application of a protective coating. This coating serves two purposes first, it protects the wire from oxidation and contamination during storage and use, and second, it helps stabilize the arc during welding. The type of coating varies according to the intended use of the wire, ranging from rust preventative to those designed for specific types of metal transfer The type of coating varies according to the intended use of the wire, ranging from rust preventative to those designed for specific types of metal transfer
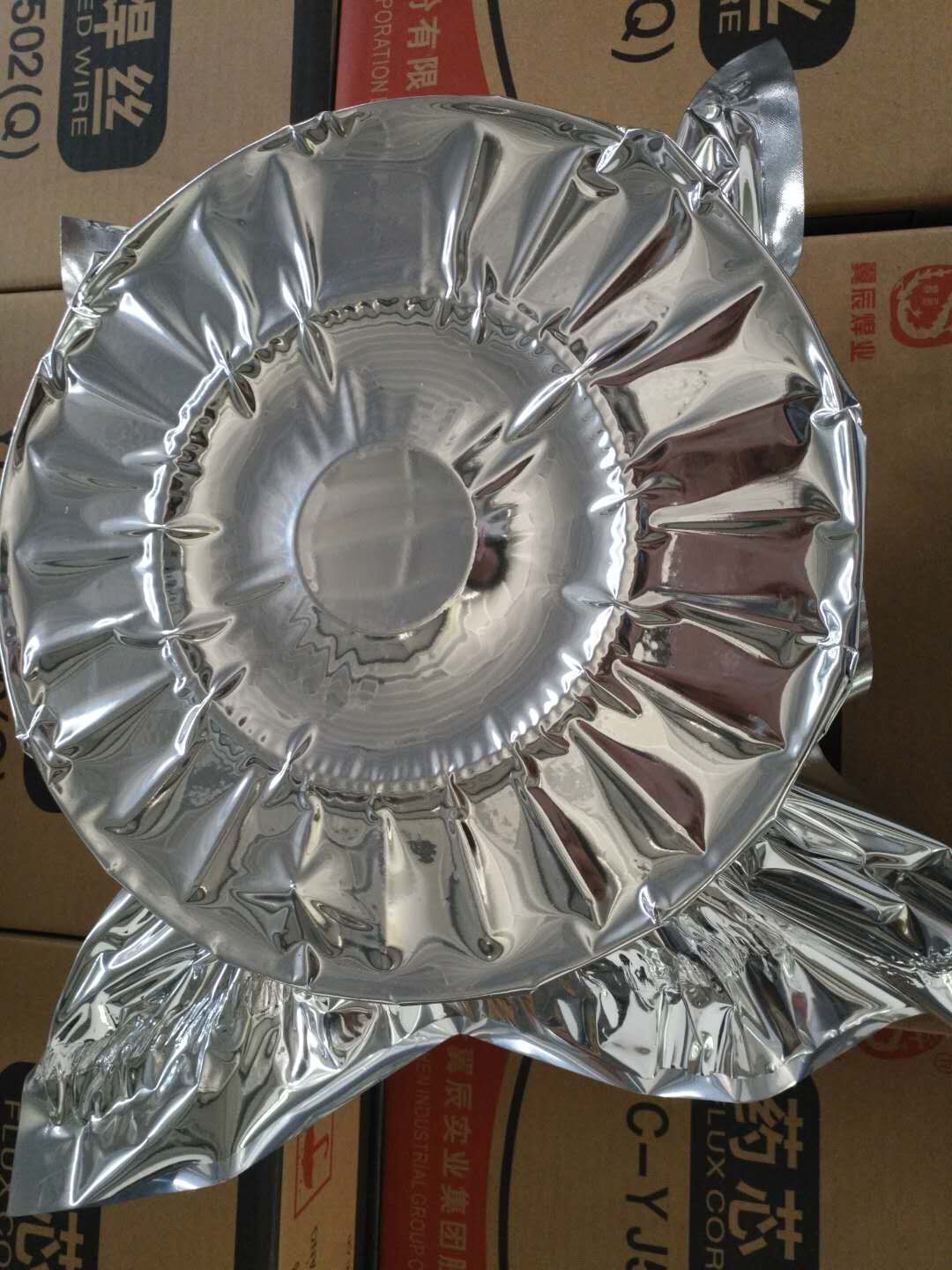
The type of coating varies according to the intended use of the wire, ranging from rust preventative to those designed for specific types of metal transfer The type of coating varies according to the intended use of the wire, ranging from rust preventative to those designed for specific types of metal transfer
mig welding wire 1.0 factory.
The factory environment where MIG welding wire 1.0 is produced is a testament to modern manufacturing efficiency. Automated lines minimize human error, while real-time monitoring systems track the quality of the wire at various stages. Quality control inspectors perform rigorous tests, from measuring the wire's tensile strength to examining its chemical composition, to guarantee that each batch meets international standards.
In addition to the technical aspects of production, factories also focus on sustainability practices. Waste management and energy-efficient operations are integral to reducing the environmental footprint of wire production. By recycling scrap metal and optimizing energy use, factories can significantly lessen their impact on the environment without sacrificing the quality of the MIG welding wire 1.0 they produce.
The production of MIG welding wire 1.0 in factories is a sophisticated process that combines cutting-edge technology with stringent quality controls. It reflects the continuous innovation and commitment to excellence that drives the manufacturing sector forward. As industry demands continue to evolve, so too will the methods by which MIG welding wire 1.0 is produced, ensuring that it remains a vital and reliable component in the world of metal joinery and fabrication.