Selecting the right MIG wire for steel welding is crucial to achieving optimal welding results. Having spent over two decades in the steel welding industry, this guide compiles the expertise and practical experience necessary to navigate the complex options available in the market, ensuring that your projects maintain high standards of quality and durability.
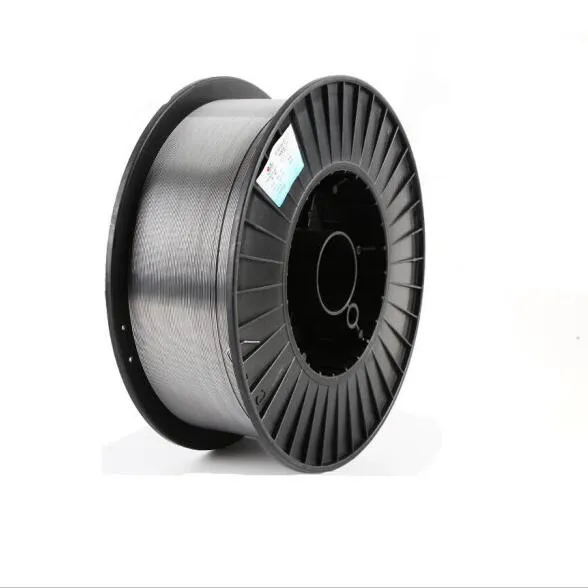
One of the pivotal aspects of choosing a MIG wire is understanding its composition relative to the welding task at hand. For general-purpose welding of carbon steel, the ER70S-6 wire is widely preferred due to its versatility. This wire contains added deoxidizers such as manganese and silicon, which helps create a cleaner welding bead, reducing the need for post-weld clean-up. This feature not only enhances productivity but also improves the quality of the weld, which is crucial for maintaining structural integrity.
Beyond composition, the diameter of the MIG wire plays a significant role in welding performance. Thicker wires (around 0.035 inches) are ideal for thicker steel, providing stronger welds with minimal effort. Conversely,
thinner wires (0.023 inches) allow for more precise work on thin gauge metal, preventing burn-through and reducing metal distortion. As a seasoned welding expert, I always recommend evaluating the thickness of your material and matching it appropriately with the wire diameter to achieve the best results.
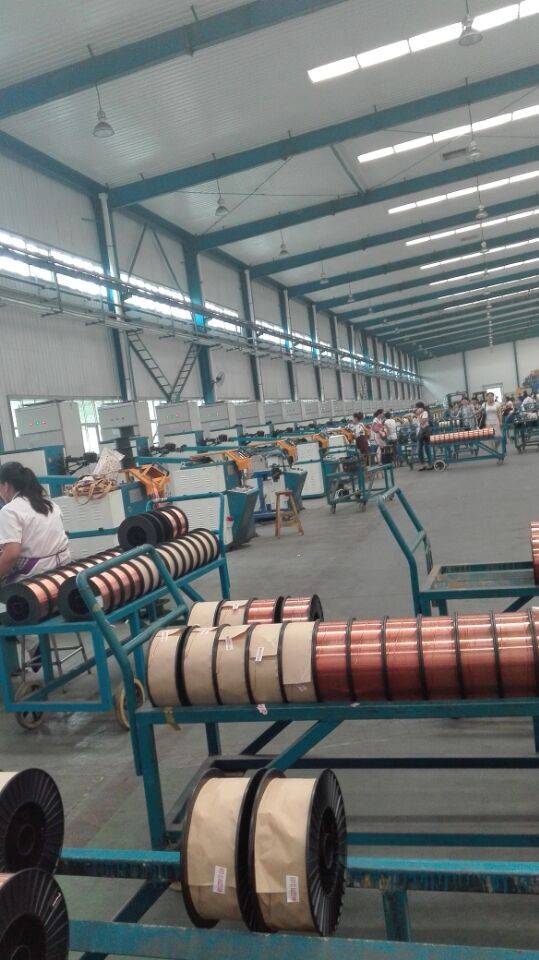
Furthermore, the shielding gas used in MIG welding can significantly impact the performance of the wire. Commonly, a mixture of 75% Argon and 25% CO2 is used, providing excellent arc stability and reduced spatter. This gas mixture complements the performance of ER70S-6 wire, particularly in applications involving automotive projects or structural work, where aesthetics and strength are paramount.
steel welding mig wire
When storing MIG wire, it is paramount to consider environmental factors that may compromise the wire's integrity, such as moisture exposure. Corrosion can significantly degrade welding quality, leading to subpar welds or equipment damage. I advise storing wire in a dry, temperature-controlled environment and using airtight containers if possible. This practice not only extends the wire's shelf life but also ensures you maintain a consistent quality in your welding over time.
Utilizing high-quality MIG wire extends beyond mere welding efficiency—it assures safety. In industrial settings where heavy machinery and structures are involved, a compromised weld can lead to catastrophic failures. As an authoritative voice in the industry, I cannot stress enough the importance of adhering to manufacturers' recommendations and conducting regular equipment maintenance to uphold safety standards.
Finally, investing in continued education and remaining abreast of advancements in welding technology is crucial for maintaining a competitive edge in the industry. Workshops, certification programs, and online courses offer valuable insights into improved welding techniques and equipment innovations. A knowledgeable welder not only ensures superior weld quality but also instills confidence in clients and peers, reinforcing trustworthiness and authority within the trade.
In conclusion, choosing the right MIG wire for steel welding requires an in-depth understanding of material properties, wire specifications, and welding environments. By meticulously selecting the proper wire and maintaining rigorous standards in storage and safety practices, welders can produce superior results that underscore their expertise and reliability in the industry. This conscientious approach to welding not only enhances personal craftsmanship but also fortifies the reputation of professionals dedicated to excellence.