Welding rods for aluminum, also known as filler rods, are a crucial component in aluminum welding, particularly when aiming to achieve durable and precise joints. Understanding the nuances of aluminum welding rods not only facilitates better decision-making for projects but also ensures that the welds deliver the expected performance and longevity.
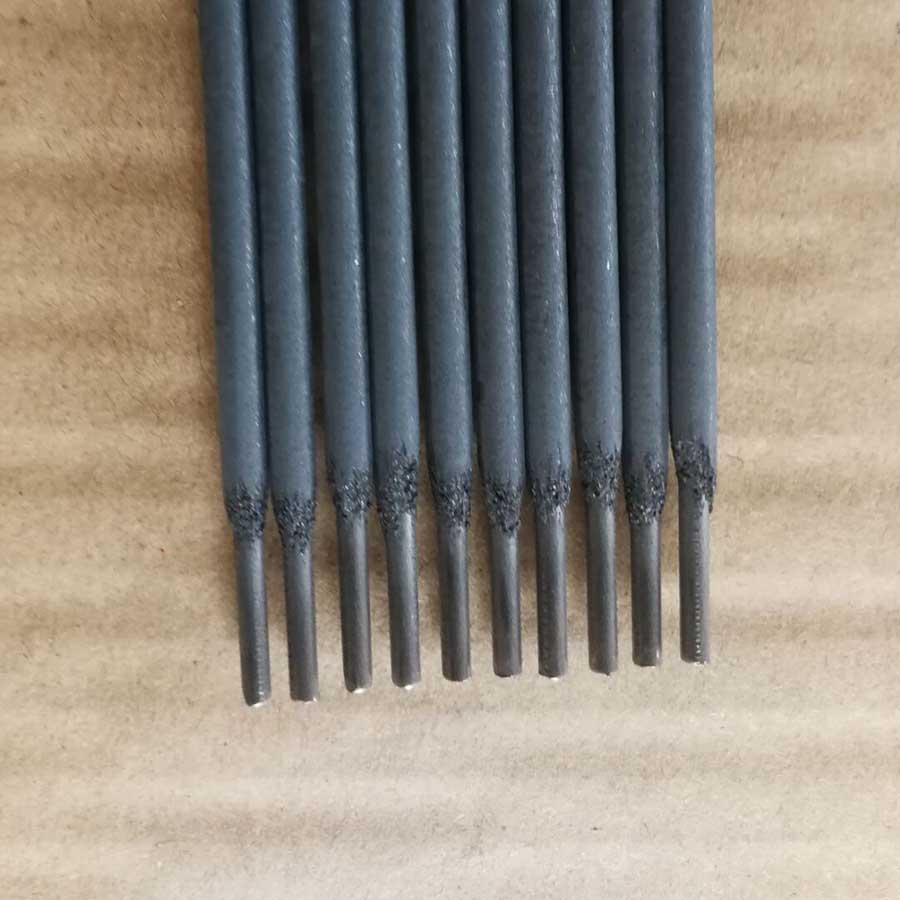
Aluminum's unique properties—its lightweight nature, high corrosion resistance, and excellent thermal conductivity—make it a favored material across various industries from automotive to aerospace. However, these same properties also pose challenges during welding, necessitating the use of specialized welding rods.
When selecting a welding rod for aluminum, it's essential to consider the specific aluminum alloy being welded. Aluminum alloys are categorized into series based on their main alloying element. The 5000 and 6000 series are most commonly welded, and each requires a specific type of filler rod to achieve the optimal weld. For instance, 4043 and 5356 are two of the most popular choices, each bringing unique characteristics to the welding process.
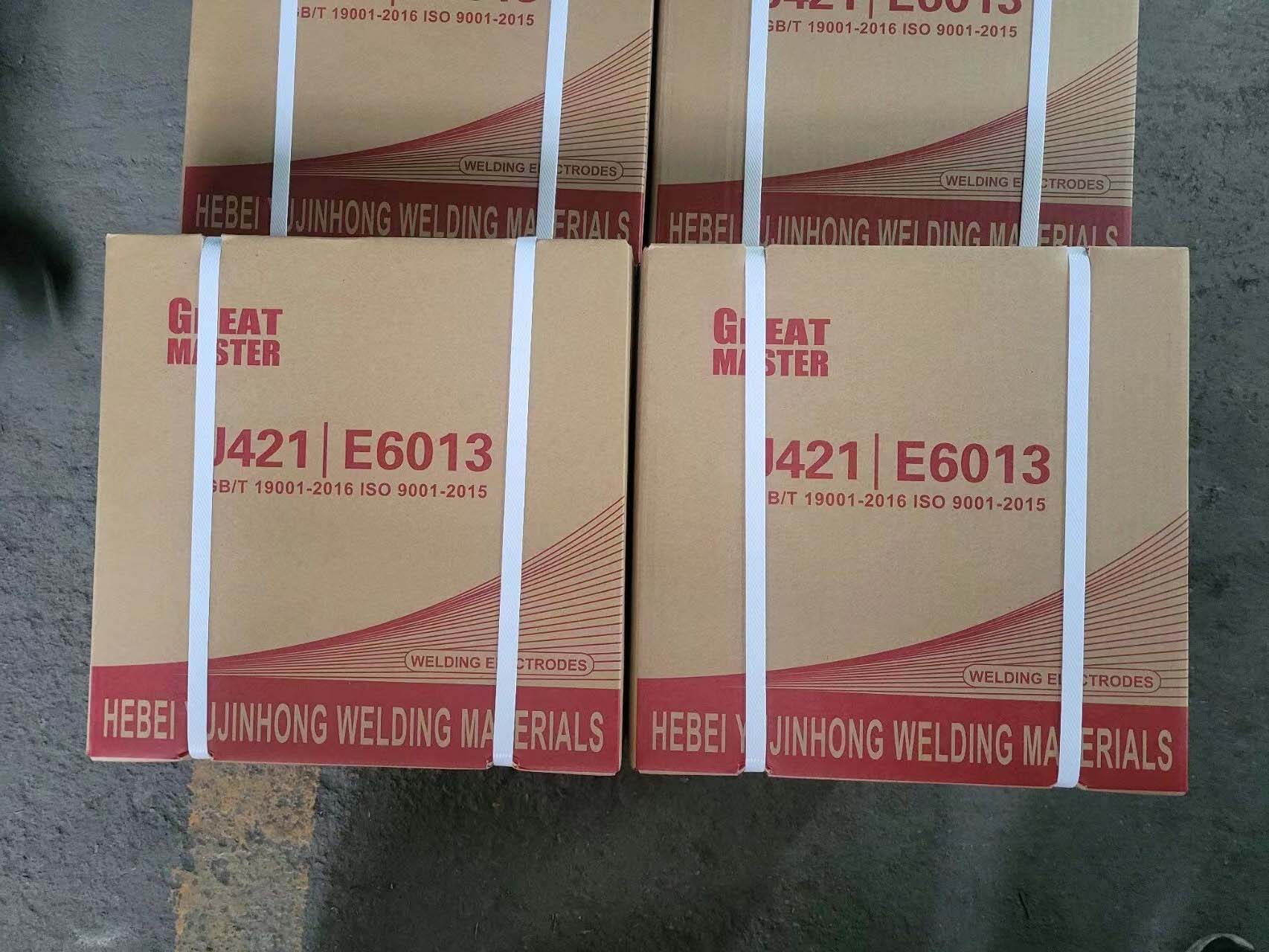
The 4043 aluminum welding rod is renowned for its versatility and is often used for general-purpose applications. It contains approximately 5% silicon, which helps reduce the melting point of the aluminum, making it easier to weld under a variety of conditions. The silicon also contributes to a more fluid weld pool, which aids in achieving a smooth and aesthetically pleasing finish. Importantly, 4043 rods produce welds that are less prone to hot cracking, a common issue in aluminum welding, thus enhancing the structural integrity of the joint.
On the other hand, the 5356 aluminum welding rod is the go-to option for applications where higher tensile strength is required. Containing magnesium as a primary alloying element, it is suitable for materials subjected to elevated service temperatures and offers exceptional corrosion resistance, particularly in marine environments. However, one must be mindful of its tendency to crack if the base metal has high silicon content, making it less suitable for some cast aluminum alloys.
welding rod for aluminum
Beyond the type of rod, welding technique plays a pivotal role in the success of the weld. Tungsten Inert Gas (TIG) welding and Metal Inert Gas (MIG) welding are the two most prevalent methods for aluminum. Each method has its optimal scenarios TIG welding is ideal for thinner gauges and provides greater control over the welding process, while MIG welding excels in speed and efficiency, making it preferable for thicker materials and larger projects.
Expertise in handling aluminum rods is essential. Pre-weld preparation, such as cleaning the aluminum to remove oxide layers and contaminants, significantly affects the quality of the weld. Furthermore, controlling heat input is critical. Aluminum's high thermal conductivity means that it dissipates heat quickly, necessitating precise heat management to avoid warping or melting through the material.
Authoritative sources in the welding industry emphasize the importance of matching the welding rod's characteristics to the base material and intended application. Publications from leading welding institutes and manufacturers provide detailed guidelines to navigate these choices, ensuring that the welder's expertise translates into exceptional results.
Over time, practical application and experience reveal that trust in a welding rod brand can significantly influence project outcomes. Renowned brands have invested heavily in research and development to produce rods that not only meet industry standards but also provide consistent performance. Their certification and adherence to rigorous manufacturing processes add a layer of trustworthiness to these products, ensuring they perform as expected in demanding environments.
In conclusion, the choice of welding rod for aluminum is not a decision to be taken lightly. It requires an understanding of the material properties, the context of the application, and the experience derived from practical application. A well-informed choice backed by authoritative insights and trustworthy products can significantly enhance the outcome of any aluminum welding project, ensuring structural integrity, longevity, and, in many cases, aesthetic appeal.