In the world of metalworking, welding sticks, also known as electrodes, play a critical role in shaping and constructing durable structures. These seemingly simple components are, in fact, cornerstones of welding technology, and their selection can make or break a welding project. Understanding their nuances is key to unlocking their potential. This discussion uses real-world experience, professional knowledge, authoritative insights, and a focus on trustworthiness to provide a comprehensive overview.
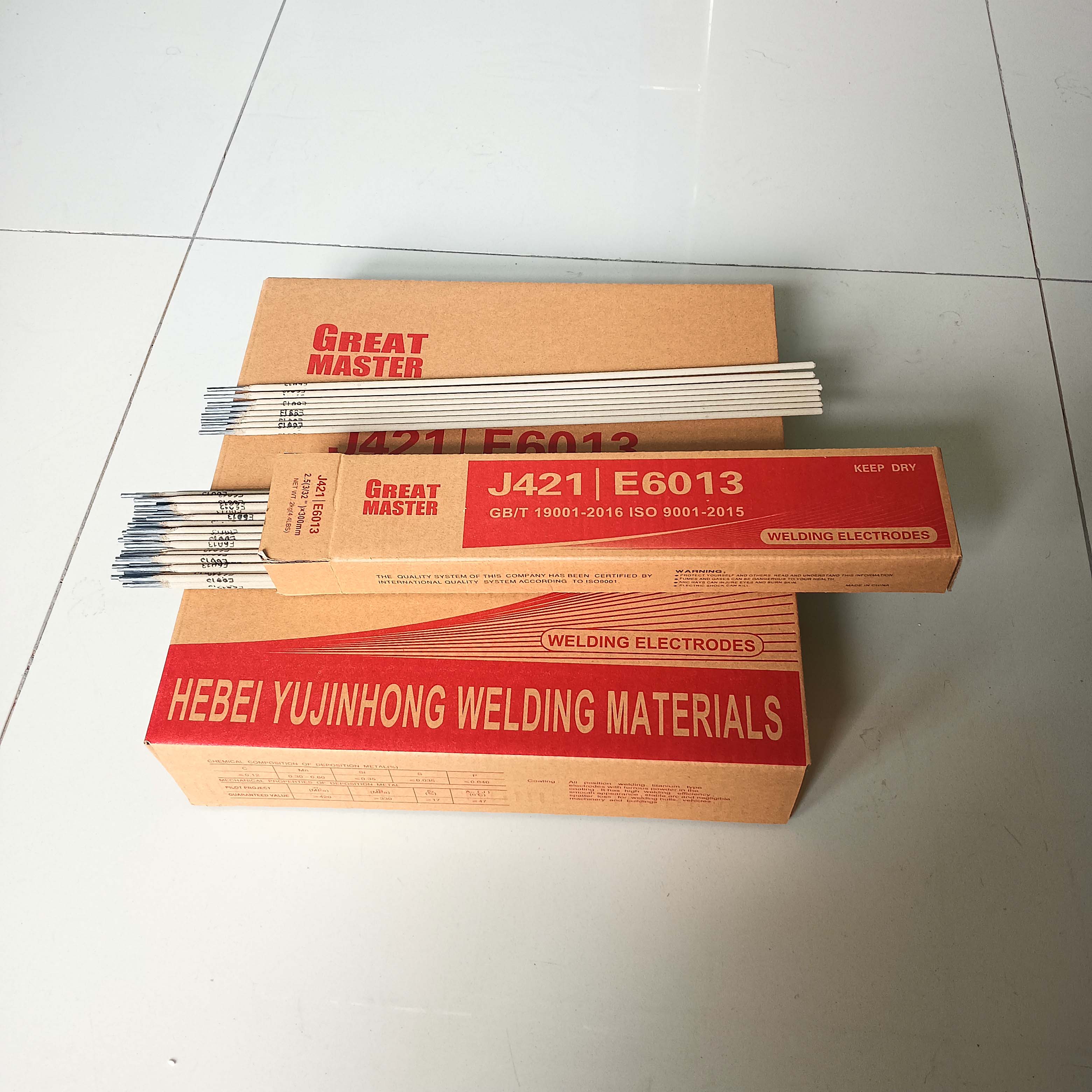
Welding sticks are coated metal rods essential for manual metal arc welding (MMAW). Their primary function is to conduct current and fuse metals, while the flux coating protects the weld from contamination. The selection of an appropriate welding stick is crucial and expertise in this area ensures the creation of robust and precise welds.
From personal experience, different projects demand different types of welding sticks. For instance, E6010 and E6011 are preferred in scenarios that require deep penetration and working with rusted or unclean surfaces. These types, with their cellulose-based coatings, deliver high-speed, high-deposition welding, making them favorites among seasoned welders working on pipelines and structurally significant projects. Conversely, E7018 is revered for its low-hydrogen coating properties. It offers a smoother finish and excellent crack resistance, suitable for high-strength welds and critical jobs like bridge construction where reliability and perfection are non-negotiable.
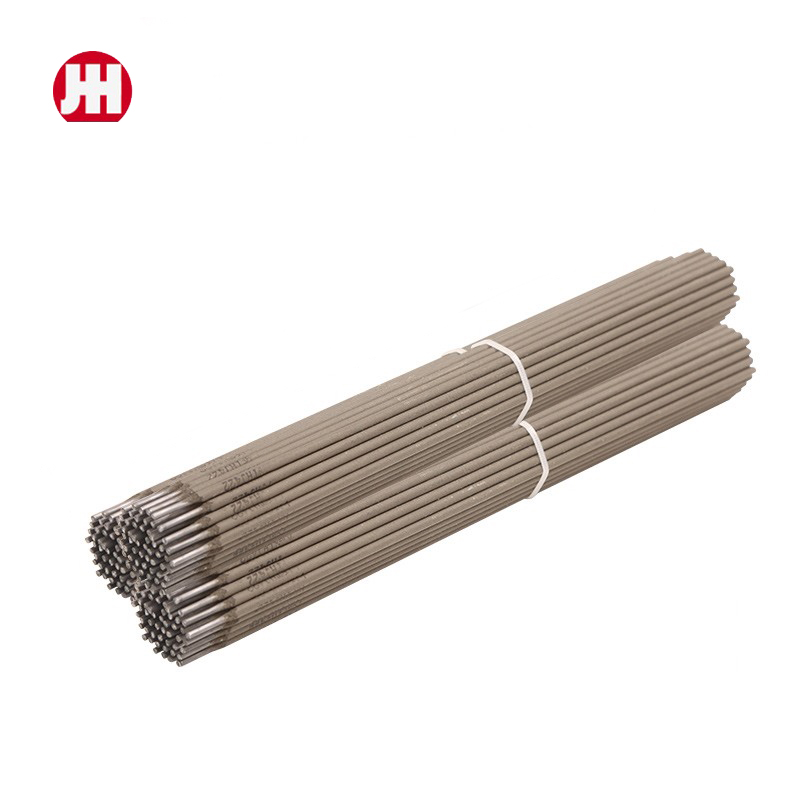
The professional authority of seasoned welders often lies in their ability to select the right electrode and adjust their techniques according to the welding stick being used. Mastery in temperature control, angling, and travel speed is essential. Years of hands-on practice reveal that the difference between a novice and an expert often hinges on their ability to adapt and modify based on the welding rod. Building this expertise involves understanding not just what each type of stick offers, but also what specific environments demand.
welding stick
From an authoritative perspective, it's crucial to rely on manufacturers' specifications and guidelines when choosing a welding stick. Professional insights suggest closely examining the American Welding Society's classification for welding sticks. Their authoritative standards help welders ensure that the electrodes chosen meet the industry requirements for tensile strength, elongation, and positional capabilities.
Credibility in welding practices is bolstered by proper storage and handling of the welding sticks. Moisture absorption can compromise coating integrity, which is why manufacturers emphasize storing electrodes in dry and controlled environments. This maintains their performance and ensures safety, aligning with both professional standards and maintaining trustworthiness on the job.
In conclusion, the journey to mastering welding sticks is both an art and a science. It requires a blend of hands-on experience, technical expertise, authoritative knowledge, and a steadfast adherence to best practices. Those who understand the intricate dynamics of welding sticks can harness their full potential, transforming simple metal rods into components of strength and resilience in construction projects worldwide. Becoming proficient in their use is not just a technical feat; it is a critical step forward for any serious welder determined to leave their mark on the industry.