The utilization of 316L electrodes has seen a significant rise across various industries, reinforcing its status as a critical component in modern welding practices. The 316L electrode, characterized by its low carbon content, is primarily used for welding stainless steels, particularly varieties containing molybdenum. Its rise in popularity is attributed to its exceptional properties and wide-ranging applications, which make it a perfect fit for industries where material integrity and performance are paramount.
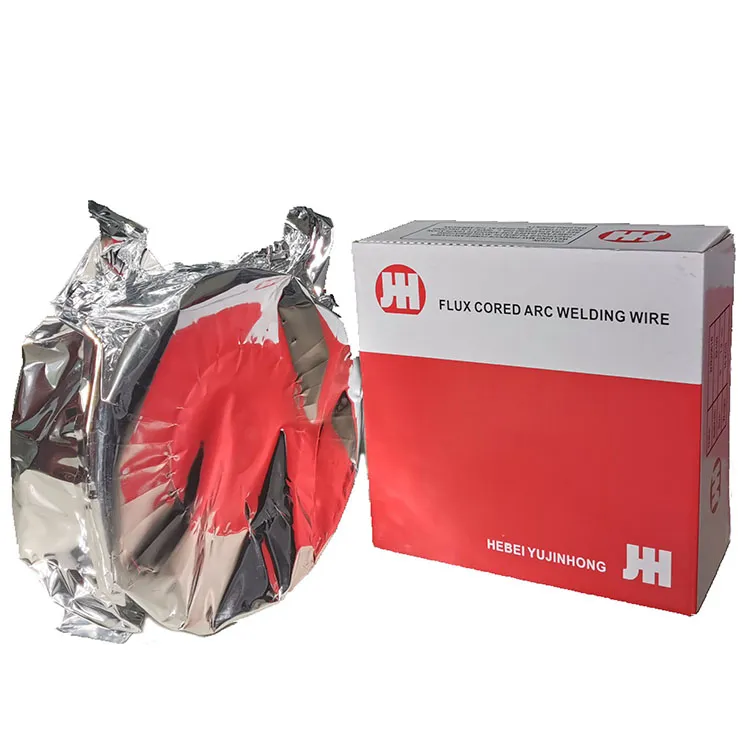
From an experiential perspective, welders who have worked with 316L electrodes often highlight its ability to offer superior corrosion resistance, especially in chloride environments. This performance is not merely anecdotal; it's backed by industry tests and real-world applications. In environments such as marine settings or chemical processing plants where the exposure to harsh conditions is routine, the employment of 316L electrodes ensures durability and longevity of the welds. This effectively reduces maintenance costs and downtime, thus delivering operational advantages over other electrode types.
In terms of expertise, 316L electrodes are engineered to handle the challenges associated with welding dissimilar materials. Their engineering ensures that they perform seamlessly across various stainless steel grades, providing a robust and reliable weld. A deep understanding of metallurgy is applied in the manufacturing process of these electrodes to ensure the welds possess high tensile strength and resistance to pitting. Professionals in the field of metallurgical engineering or materials science often recommend using 316L electrodes when welding austenitic stainless steel, given its compatibility and consistent performance.
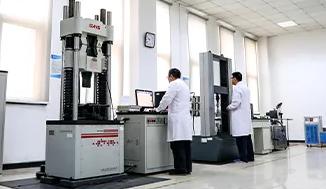
Authoritativeness in the context of 316L electrodes comes from the adherence to international standards which these products comply with. Standards set by bodies such as the American Welding Society (AWS) and other relevant authorities guide the production and application of these electrodes. Following these stringent guidelines, manufacturers produce 316L electrodes that not only meet but often exceed the industry benchmarks for quality and safety. Organizations that utilize 316L electrodes frequently conduct certifications and training to ensure that their welding teams are capable of leveraging these high-caliber products effectively.
316l electrode
Trustworthiness in welding is crucial, as it directly affects the safety and integrity of structures. The reliability of 316L electrodes is well-documented through numerous case studies and user feedback that highlight successful implementations across stress-intensive applications. Customers rely on these electrodes for both their innovative design, which enhances welding quality, and their predictability in performance, making them a staple recommendation among industry veterans.
In product-oriented discussions, the 316L electrode is often positioned as a solution for overcoming common welding challenges such as sensitization or intergranular corrosion. Given its low carbon content, the likeliness of carbide precipitation at the grain boundaries during welding is reduced, helping maintain the corrosion-resistant properties of the stainless steel. Thus, 316L electrodes are frequently recommended for applications in environments that demand cleanliness and resistance to pollutants and corrosive elements.
The effectiveness of these electrodes extends to their performance in various welding techniques, such as gas tungsten arc welding (GTAW), shielded metal arc welding (SMAW), and gas metal arc welding (GMAW). Across these methods, the 316L electrode provides excellent control over the welding arc, leading to smooth and defect-free weld beads. This versatility makes it an indispensable tool for professional welders looking to achieve premium quality welds with efficiency and precision.
In conclusion, the 316L electrode stands out as an exemplary product in welding, offering unparalleled reliability and performance. It meets the demands for non-reactive, durable, and structurally sound joint formation across industries that prioritize safety, efficiency, and long-term service. Welders and engineers alike vouch for its dependability, making it a preferred choice for critical projects and an essential component in the welding toolkit. Whether for repair, maintenance, or new constructions, its adaptability and quality assurance mark it as an industry leader, perpetually setting the standard for modern welding requirements.