Aluminum welding wire is a critical component in various industrial and domestic applications. When selecting welding wire, it's essential to understand its unique properties and how they impact welding performance. Professional welders often seek aluminum welding wires for their capacity to deliver strong, reliable joints in aluminum fabrication projects. The superior corrosion resistance of aluminum makes it a preferred choice for marine applications, automotive manufacturing, and structural projects, where durability is paramount.
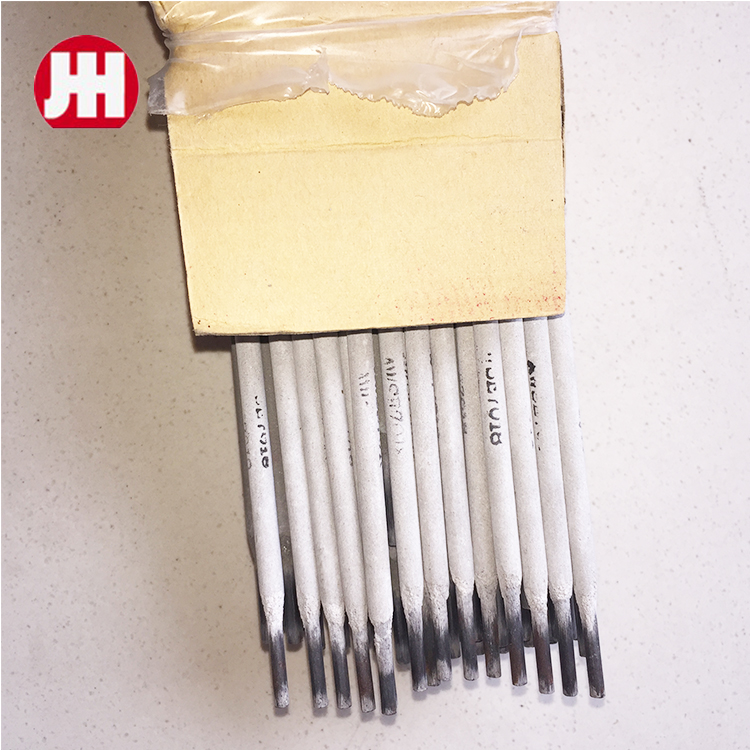
Expertise in welding requires a deep understanding of the different aluminum alloys available. These include popular variants like 4043, 5356, and others, each with distinct characteristics determining their suitability for different tasks. For instance, 4043 aluminum welding wire is favored for its smooth, attractive finish and is particularly adept at welding 6000 series aluminum. This alloy is renowned for its ease of use, minimal thermal expansion, and suitability in applications requiring a low-heat process. Its silicon content enhances the flow while providing a sheen that finishes beautifully.
On the other hand, 5356 aluminum welding wire is utilized for its exceptional strength and is optimal for welding 5000 series aluminum, popular in both transport and construction sectors. The magnesium content in 5356 gives it a higher tensile strength, making it a preferred choice when joint integrity cannot be compromised. Furthermore, it is less prone to cracking, a critical factor in load-bearing structures. This alloy also provides superior corrosion resistance, an essential feature for applications exposed to harsh environments.
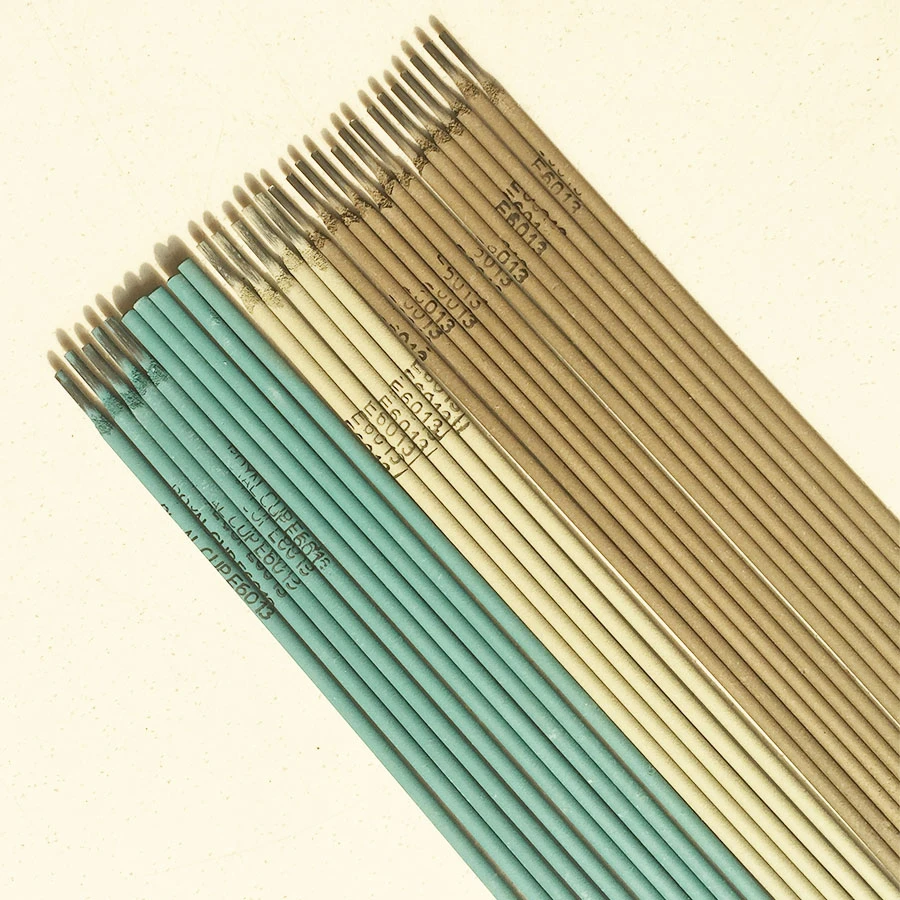
When it comes to the welding process, using aluminum wire presents unique challenges that require a degree of expertise to navigate successfully. Aluminum's high thermal conductivity demands that the welder effectively manage the heat input to prevent warping or burn-through. In addition, because aluminum is more susceptible to contamination, cleanliness is crucial. Experienced professionals often recommend prepping the metal surfaces with a chemical cleaner or wire brush to ensure optimal results.
aluminum welding wire
In terms of equipment, choosing a welder with appropriate settings for aluminum is critical. MIG welders are commonly used for aluminum welding, thanks to their speed and the strength of the welds produced. It is advisable to fit these welders with suitable accessories like a spool gun, which facilitates smooth feeding of the softer aluminum wire, preventing tangling and ensuring consistent delivery without disrupting the arc.
Authoritativeness in the field can be gauged by the continuous advancements in aluminum welding technology and the expertise of manufacturers in producing high-quality wire. Companies that invest in rigorous testing and quality assurance processes can confidently offer products that consistently perform under demanding conditions. Trustworthiness in product claims is further established through certifications and compliance with industry standards that ensure welders receive a reliable and safe product.
Aluminum welding wire's growing popularity across various sectors aligns with the increasing demand for lightweight, strong, and corrosion-resistant materials. As industries continue to innovate, leveraging the benefits of aluminum can enhance performance, reduce weight, and improve overall efficiency in their products. By understanding and applying the right techniques and choosing high-quality wire, professionals in the field can achieve exceptional results, ensuring longevity and integrity in their projects.