Copper welding wire, an essential component in the welding industry, stands out due to its excellent conductivity, versatility, and reliable performance in various welding applications. Welding, an age-old technique that involves the joining of two or more parts, relies heavily on the quality and properties of the welding material used. Copper welding wire, in this regard, offers unparalleled benefits, ensuring not just seamless welds but also long-lasting durability.
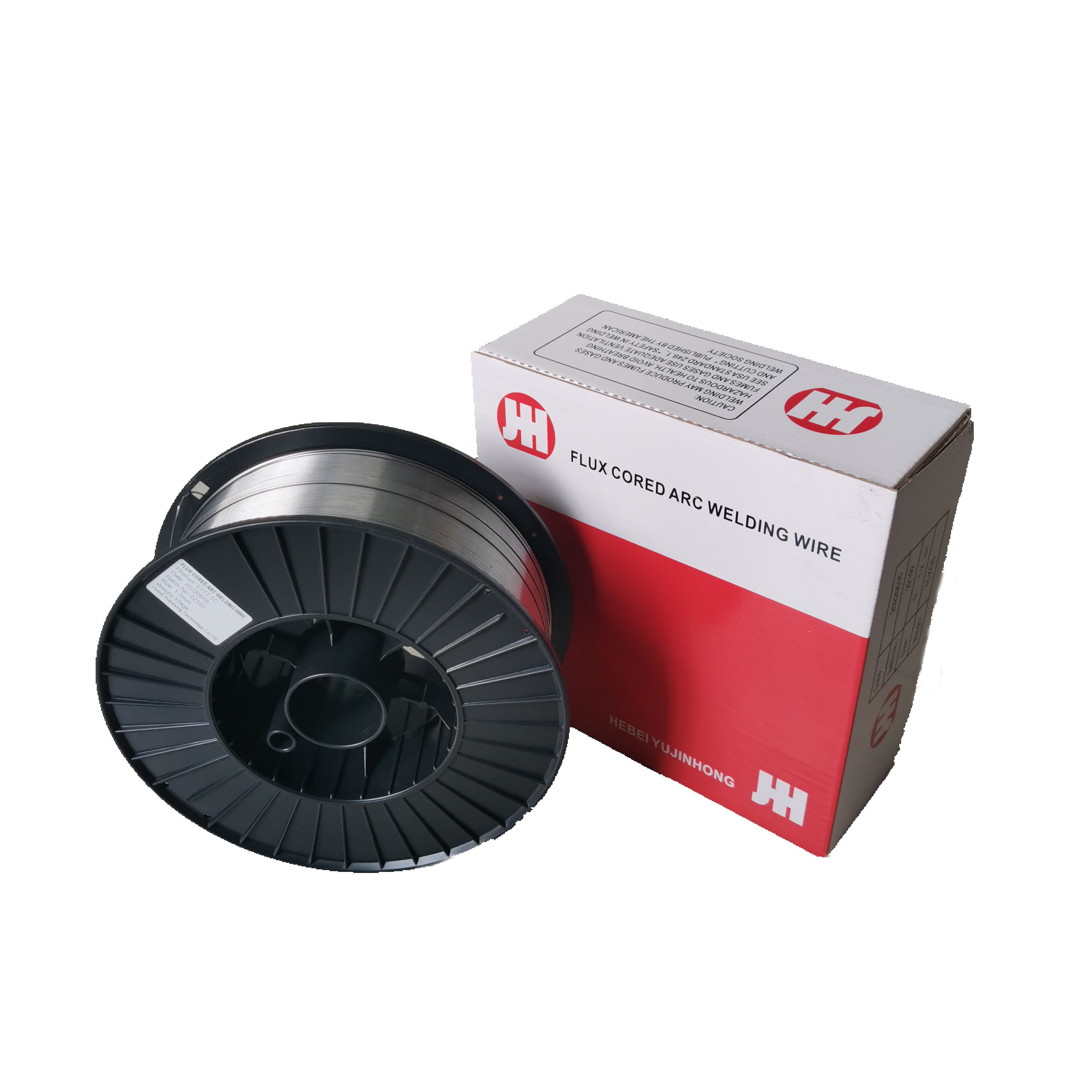
With years of hands-on experience in the field, I have observed the transformative effect that using high-grade copper welding wire can have on a project. These wires boast high thermal and electrical conductivity, characteristics that are pivotal in ensuring strong and precise welds. The malleability and ductility of copper, combined with its resistance to corrosion, make copper welding wire an indispensable resource for engineering projects demanding precision and robustness.
A common challenge in welding is maintaining the integrity of the weld joint under varying conditions. Here, copper welding wire shines due to its exceptional thermal conductivity, which enables it to disperse heat rapidly. This fast heat dissipation minimizes distortion, a common issue welded structures face. Furthermore, for projects requiring multiple metals to be joined, copper welding wire provides an excellent solution due to its compatibility with numerous base metals, ranging from steels to bronzes.
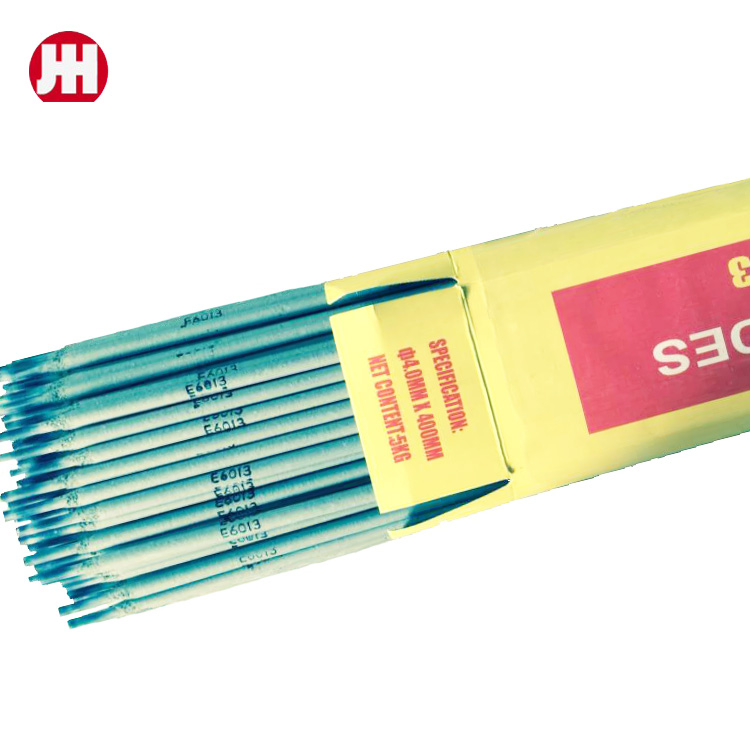
Years of collaborating with fellow industry experts have underscored the importance of selecting the right type of welding wire according to project needs. Copper welding wire, with its diverse alloy compositions, caters to specific welding requirements, such as TIG, MIG, or even oxy-acetylene welding. This versatility allows welders to achieve efficient results, whether they are working on delicate electronics or heavy machinery.
copper welding wire
In the realm of expertise, it's notable that using copper welding wire can significantly impact the efficiency and cost-effectiveness of a project. Its ability to withstand harsh environments without losing structural integrity reduces maintenance needs and prolongs the lifespan of welds. This reliable performance is a testament to copper's superior properties over other welding materials, establishing it as a trusted choice among seasoned welders.
Authoritativeness in the domain of welding materials assesses not only material performance but also supplier reliability. The best copper welding wire suppliers offer thoroughly tested products that adhere to industry standards, providing assurance of quality. They also equip professionals with technical documentation and support, fostering informed decisions and success in complex welding tasks.
Trustworthiness, a critical factor in the adoption of any material, particularly in safety-essential applications such as welding, hinges on consistent product performance and transparency from the supplier.
Copper welding wire has been rigorously tested in varied environments, proving its integrity time and again. Moreover, suppliers who offer comprehensive customer service, including expert advice and prompt support, enhance trust and ensure that welders can achieve optimal results.
In conclusion, copper welding wire is not merely a consumable product; it is a cornerstone of successful welding operations. Its unique properties, coupled with the backing of reputable suppliers, provide a solid foundation for effective and lasting welds. Professionals are empowered to take on complex projects with confidence, knowing that the integrity of their work is supported by this exceptional material. As the welding landscape continues to evolve, copper welding wire remains a vital component, bridging the past's expertise with the future's innovations.