Flux cored arc welding (FCAW), also know as dual shield welding, is a semi-automatic arc welding process that is similar to metal active gas (MAG) welding. FCAW uses a continuous wire fed electrode, a constant-voltage welding power supply, and similar equipment to MAG welding.
The process was first developed in the 1950s as an alternative to manual metal arc (MMA) welding which is also called stick welding. FCAW overcomes many of the restrictions associated with MMA, since it uses a continuously fed wire electrode.
Flux core arc welding usually uses a shielding gas similar to that used by MAG welding, but it can also be performed without a shielding gas. It is more productive than MAG welding.
How Does Flux Core Arc Welding Work?
Flux cored arc welding uses heat generated by an electric arc to fuse base metal in the weld joint area. This arc is struck between the metallic workpiece and the continuously-fed tubular cored consumable filler wire, with both the wire and the metallic workpiece melting together to form a weld joint. This is similar to MAG welding, except that FCAW welding uses a hollow, tubular electrode filled with flux rather than a solid metal electrode.
The FCAW process can be divided into two types depending on the shielding method; one that uses an external shielding gas and one that solely relies on the flux core itself for protecting the weld area.
MIG FLUX CORE WIRE FLUX-CORED WELDING WIRE
The shielding gas, where used, protects the weld pool from oxidation and is usually provided externally from a high-pressure gas cylinder. Weld metal is also shielded by the slag formation from flux melting. Thus the process informally known as ‘dual shield’ welding and was primarily developed for the welding of structural steels. The most commonly used shielding gases are carbon dioxide or blends of argon and carbon dioxide. The most frequently used blend is 75% argon and 25% carbon dioxide. This dual shield method is preferred for welding thicker materials or for out of position welding. This process, when used in identical settings, delivers welds with more consistent mechanical properties and with fewer defects than with MMA or MAG processes. The continuously fed tubular electrode also allows for higher production rates than with solid wire or stick electrode. However, the gas shielded method may not be suitable for use in windy conditions as the disturbance to gas shielding could result in reduced weld metal properties.
The second version of this process doesn’t use an external shielding gas, but instead relies on the protection offered by the flux cored electrode itself. This electrode provides gaseous protection and also forms a slag that covers and protects the molten metal in the weld. The filler wire core contains slag forming fluxing agents and materials that produce shielding gases when burned by the heat of the welding arc. The shielding flux means that this process can be easily used outdoors even in windy conditions without the need of external shielding gas. This makes the process extremely portable and hence suitable for outdoor welding applications.
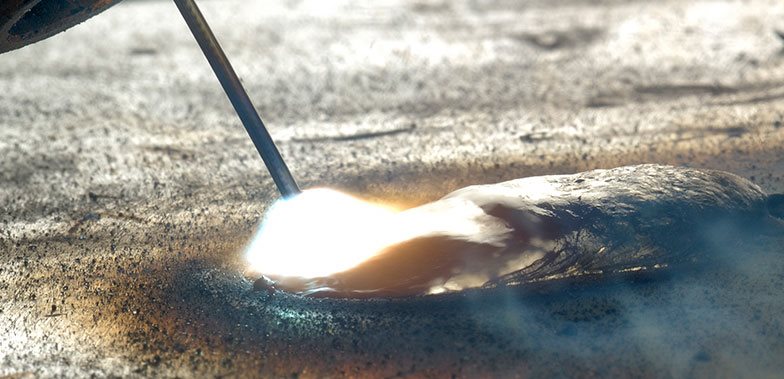
Which Metals Can Be Welded with FCAW?
Flux cored arc welding works well with most carbon steels, cast iron, stainless steel and hard facing / surfacing alloys.
However, nonferrous exotic metals, such as aluminium, cannot be welded using this welding technique.
What are the Advantages?
The flux core welding technique provides several advantages over other methods. FCAW is preferable to MAG welding for outdoor use as well as for joining of thicker materials. The built-in shielding provided by the filler wire can endure strong breezes and, if used without an external shielding gas, FCAW is portable and convenient. This welding process also provides more flexibility with alloy compositions than MAG. It also offers higher wire deposition rates and improved arc stability, allowing for high speed applications without adversely affecting good quality weld.
Flux cored arc welding can be an ‘all position’ process and also requires less skill among operators than MMA and MAG. It also requires less precleaning of metals than other processes. The chances of porosity are also very low if FCAW is applied correctly.
What are the Disadvantages/Limitations?
There are few disadvantages of the process compared to other welding techniques, including production of noxious smoke that can make it difficult to see the weld pool. FCAW generates more smoke than other processes such as MMA or MAG.
Porosity can also be a problem if the gases from the weld metal are not able to escape out before the weld metal solidifies.
FCAW electrodes require better handling and storage procedures compared with solid wire electrodes. Because of tubular nature, filler material can be sometimes more expensive than the solid counter parts.
The correct filler metal needs to be chosen to ensure the required mechanical properties. Also, consistent wire feeding needs to be ensured to avoid related weld problems.
Another disadvantage is the slag formation that needs to be removed prior depositing each subsequent layer. Finally, while FCAW is excellent for joining thicker metals, it is not recommended for use on materials thinner than 20 gauge.
What is FCAW Used For?
It is a flexible welding process suitable for all position welding, given the correct filler material and flux composition. Being highly productive due to the high deposition rates, it provides high quality welds with a good appearance. The high welding speed and portability of this welding method means that it is widely used in construction. This is further supported by the fact that the process can be readily performed outdoors, even in windy conditions.
Since it can be used to for a range of alloys, plain carbon, stainless and duplex steels, flux cored arc welding is also frequently used for surfacing and hardfacing.